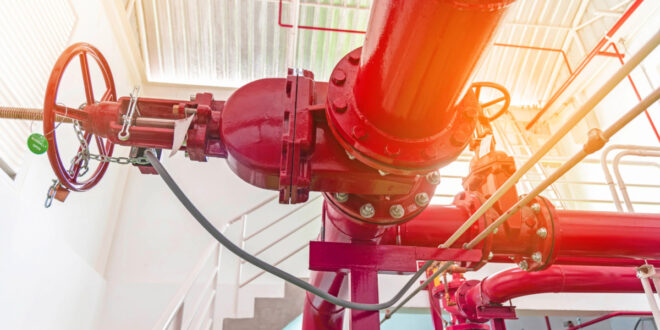
THE IMPORTANCE OF ANNUAL FIRE PUMP TESTING
ENSURING YOUR FIRE PUMP SYSTEM IS READY WHEN YOU NEED IT MOST
Fire pumps are critical components of water-based fire protection systems; however, pumps can look like intimidating pieces of equipment to those who need to become more familiar with them. Fire pumps are installed in facilities where the available water source cannot meet the flow and pressure demands of the most demanding water-based fire protection systems onsite. They provide, or help to provide, the necessary pressure and flow for the water-based fire protection systems to work as designed to contain, suppress, or extinguish a fire occurring within the facility. Like any mechanical device, fire pumps can wear down and deteriorate over time and may not function properly when most needed. That’s why annual fire pump testing is essential for ensuring that your fire pump is in good working condition and is ready to protect your property and the lives of your occupants.
WHAT IS AN ANNUAL FIRE PUMP TEST?
The annual fire pump test comprehensively evaluates a fire pump’s performance and condition. The fire pump will receive a thorough inspection, additional testing, and preventative maintenance on components compared to the regular no-flow (churn) testing done periodically throughout the year to ensure the pump can continue operating as designed and installed.
WHY IS ANNUAL FIRE PUMP TESTING IMPORTANT?
There are many reasons why annual fire pump testing is critical, including, but not limited to:
- Ensure compliance with NFPA 25, Standard for Inspection, Testing, and Maintenance of Water Based Fire Protection Systems: Locally adopted fire codes require fire pumps to be inspected, tested, and maintained in accordance with NFPA 25.
- Reduce the risk of fire pump failure: Early detection of problems and preventative maintenance can prevent fire pump failure, which can have devastating consequences.
- Minimize property damage and loss of life: A properly functioning fire pump can help to minimize property damage and loss of life in the event of a fire.
- Lower insurance costs: Insurance companies may offer lower premiums for properties with well-maintained fire protection systems.
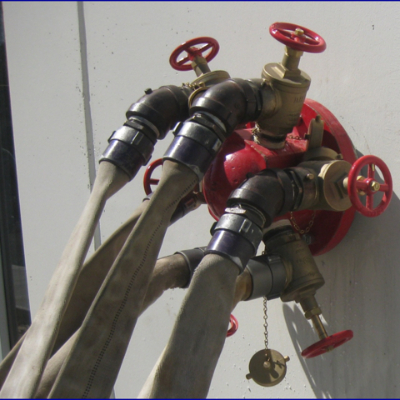
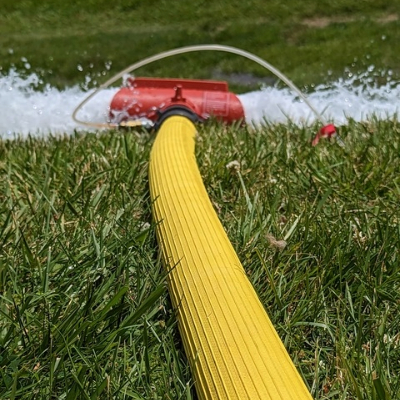
WHAT TO EXPECT DURING A FIRE PUMP TEST
The fire protection contractor will arrive at your property with the necessary equipment to conduct the test. The test will typically take a few hours to complete as preventative maintenance items are also typically conducted with the annual flow test, depending on how your service contract is structured. The minimum frequency for a fire pump to be flow tested is annually. It is flow tested at a minimum of three different flow conditions: no-flow (churn), 100 percent of rated flow capacity, and 150 percent of rated flow capacity. If a variable speed pump configuration is present, there will be additional test points, and the pump will run in both variable speed and fixed speed configurations. For variable speed pumps in the variable speed condition, data needs to be collected at six different flow conditions: no-flow, 25 percent, 50 percent, 75 percent, 100 percent, 125 percent, and 150 percent of rated flow capacity. When the variable speed pump is in the fixed speed condition, data must be collected at the same three flow conditions as a regular fixed speed pump outlined above. With the need for additional test points, annual flow testing of a variable speed pump will require more time and a larger volume of water to flow throughout the duration of the annual test compared to a traditional fixed speed fire pump test.
Some pumps may not be able to be tested to 150 percent of the rated flow mark. There can be a few reasons for this, but it typically comes down to either safety stop rules put in place by the local water purveyor or the way the piping for the test header is configured. Safety stops put in place by the water purveyor will limit how low the suction pressure is allowed to go for pumps supplied by city water lines. This is to protect the integrity of the water supply piping and prevent debris and contaminants from being entrained into the potable water supply. If it is due to the piping configuration for the test header, then the raw data points from the test header may be misleading until they are adjusted by a qualified individual to account for pressure loss due to friction through the test header piping. In these cases, the pump is run to the point where it discharges the most water at the lowest permissible suction pressure.
DATA COLLECTION
The pressure readings from the suction and discharge gauges on the appropriate sides of the pump will be recorded at each flow condition. Pump speed (in rpm) will also be recorded. For electrically driven pumps, voltage and amperage readings will be taken on all lines if the reading can be taken without opening the pump controller. Engine oil pressure, speed, and temperature (water and oil) will be recorded periodically but do not have to coincide with reaching each flow condition.
PASS AN FAIL CRITERIA
NFPA 25 has a few criteria that the pump is evaluated against to determine whether the pump and water supply as a whole are considered acceptable and performing as designed.
8.3.7.2.3 The fire pump test results shall be considered acceptable if all of the following conditions are satisfied
8.1.5.1 The suction supply for the fire pump shall provide the required flow at or above the lowest permissible suction pressure to meet the system demand.
Simply put, the pump is checked to make sure that it is doing the work it was designed to do and that the pump, coupled with the water supply, is able to meet the demands of the water-based fire protection systems it is serving. The work the pump is doing is considered the net performance of the pump. This is the discharge pressure minus the suction pressure at each flow point to determine how much work the pump is doing to achieve that result at that flow point. The gross performance of the pump is the discharge pressure curve of the pump. Gross pump performance is what the systems downstream are seeing. This is a more inclusive performance measurement as it incorporates both the water supply performance and the pump performance. Both net and gross performance should be evaluated.
Suppose the pump does not meet the above conditions to be considered acceptable. In that case, the building owner will be notified in writing, and an investigation into the cause of the unacceptable results will be performed. Looking at the net and gross performance curves can help determine why a pump may not have met all of the passing test criteria. It is possible for a pump to perform appropriately on the net performance curve but not pass when comparing gross performance to the most demanding water-based fire protection system. The incoming water supply could have deteriorated, and although the pump is still performing as designed, without as strong of a water supply coming in, it is unable to meet the demands of the fire protection systems. Depending on the cause of the unacceptable results, the pump will receive a deficiency classification (impaired, critical deficiency, noncritical deficiency). A pump receiving an unacceptable test result should be repaired, or the cause corrected, as quickly as possible due to the criticality of the fire pump to the overall performance of the water-based fire protection systems within the facility. In some cases, the qualified person analyzing the results may deem the change as acceptable simply due to age.
ANNUAL FIRE PUMP REPORTS
The fire sprinkler contractor will provide you with a written report of the test results, identifying any problems that need to be addressed.
8.4.1.1 At a minimum, the report shall contain the following information:
- All raw data necessary for a complete evaluation of the fire pump performance, including suction and discharge pressures, voltage and amperage readings to the extent that such work can be completed without opening an energized electric motor–driven fire pump controller, and pump speed at each flow rate tested
- Fire protection system demand as furnished by the owner
- Pump performance, whether satisfactory or unsatisfactory
- Deficiencies noted during the testing and identified during analysis, with recommendations to address deficiencies as appropriate
- Manufacturer’s performance data, actual performance, and the available pump discharge curves required by this standard
- Time delay intervals associated with the pump’s starting, stopping, and energy source transfer
- Where applicable, comparison with previous test results
In addition to annual testing, there are several other things that you can do to keep your fire pump in good working condition, including:
- Performing the periodic no-flow testing on your fire pump.
- Paying attention to changes in pump conditions (vibration, noises, smells) during the no-flow testing throughout the year.
- Performing preventative maintenance observed by your testing and inspecting contractor.
- Quickly addressing any deficiencies noted during any inspections or tests of the pump.
Interested in learning more about fire pump inspection, testing, and maintenance? Want to get more hands-on with performing no-flow and annual fire pump testing and evaluating the results? New in 2024, AFSA will be offering a two-day hands-on fire pump class. Click here to learn more about this class, register, or learn about other AFSA training opportunities.
ABOUT THE AUTHOR:
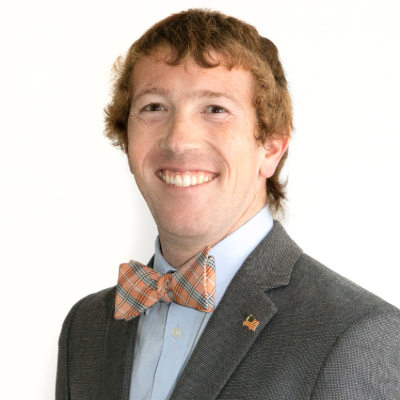
Eric Andresen, WBITM, is the technical training specialist for the American Fire Sprinkler Association (AFSA). He has experience with risk engineering applied to fire protection system analysis and the inspection, testing, and maintenance of fire protection systems for the insurance industry. Andresen has experience in the hands-on training of water-based fire protection systems for risk engineers and facilities management staff. Andresen received his Bachelor of Science degree in fire protection and safety engineering technology from Oklahoma State University.