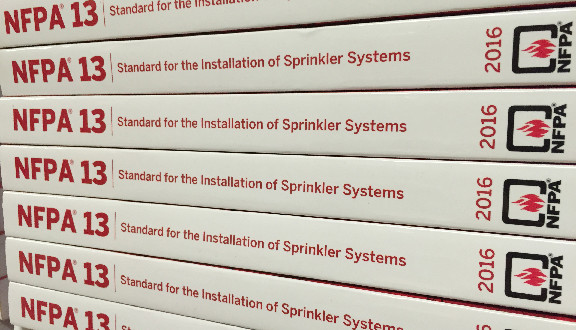
The 2016 Edition of NFPA 13
What Has Changed and Why
I know most jurisdictions are just starting now to enforce the 2013 edition of NFPA 13, Standard for the Installation of Sprinkler Systems. However, the 2016 edition is now officially out and will start being applied over the next few years. Thinking about it, in the next several months, the committee will be starting the process to develop the 2019 edition. The cycle never really stops. One thing is for certain, if you do not keep up with the changes, you will be left behind.
This article will attempt to highlight some of the technical changes in the 2016 edition. I will proceed hitting the high points that directly affect a sprinkler company and where space allows, I will try to explain the reason behind the change.
6.2 Reinstallation of a sprinkler
“6.2.1.1 – When a sprinkler is removed from a fitting or welded outlet, it shall not be reinstalled except as permitted by 6.2.1.1.1.
“6.2.1.1.1. – Dry sprinklers shall be permitted to be reinstalled when removed in accordance with the manufacturer’s installation and maintenance instructions.
“A.6.2.1.1 Sprinklers should be permitted to be reinstalled when the sprinkler being removed from the system remains attached to the original fitting or welded outlet, provided care has been taken to ensure the sprinkler has not been damaged. Flexible hose connections are considered a fitting.”
The change was to allow dry pendent sprinklers to be removed and reinstalled and to clarify that the intent is if the sprinkler stays in the fitting and is protected from damage, it could be reused. However, if torque was applied to the sprinkler by removing the sprinkler from the fitting, it must be replaced.
6.4.8 Extension Fittings (also known as cheaters)
“6.4.8 Extension Fitting.
“6.4.8.1 – Extension fittings shall be permitted to be used with sprinklers K-8.0 or smaller.
“6.4.8.2 – Extension fittings shall be permitted to be used with sprinklers in light hazard and ordinary hazard occupancies only.
“6.4.8.3 – The internal diameter of extension fittings shall have the same nominal inlet diameter of the attached sprinkler.
“6.4.8.4 – A single extension fitting up to a maximum of 2 in. (50 mm) in length shall be permitted to be installed with a sprinkler.
“6.4.8.4.1 – Extension fittings longer than 2 in. (50 mm) shall not be permit- ted unless specifically listed.
“6.4.8.5 – Extension fittings shall be included in the hydraulic calculations.
“6.4.8.5.1 – Extension fittings 2 in. (50 mm) and less shall not be required to be included in the hydraulic calculations.”
Many of us have seen this practice for years and there were large debates whether this was actually allowed by NFPA 13. Now, the committee finally put some rules to this topic. At this time, the author is not aware of any listed extension fittings. Time will tell if any manufacturer develops a listed extension fitting. My educated guess is the market is not big enough to warrant the cost for a manufacturer to bring one to market.
“7.1.5 Air Venting.
“7.1.5 – Air Venting. A single air vent with a connection conforming to 8.16.6 shall be provided on each wet pipe system utilizing metallic pipe. (See A.8.16.6.)
“7.1.5.1 – Venting from multiple points on each system shall not be required.”
“8.16.6* – Air Venting. The vent required by 7.1.5 shall be located near a high point in the system to allow air to be removed from that portion of the system by one of the following methods: (1) Manual valve, minimum 1/2-in.
(15-mm) size
(2) Automatic air vent
(3) Other approved means”
“A.8.16.6 A manual or automatic air venting valve can be a reasonable approach on wet pipe sprinkler systems to reduce corrosion activity. The purpose of the air venting valve is to exhaust as much trapped air as possible from a single location every time the system is filled. The objective of venting is to reduce the amount of oxygen trapped in the system that will fuel corrosion and microbial activity. It is neither the intent nor practical to exhaust all trapped air from a single location on a wet pipe sprinkler system; however, more than one vent can be used on a system at the designer’s discretion. Interconnection of branch line piping for venting purposes is not necessary. An inspector’s test valve can serve this purpose.
“The air venting valve should be located where it will be most effective. System piping layout will guide the designer in choosing an effective location for venting. In order to effectively accomplish venting, it is necessary to choose a location where the greatest volume of trapped air is vented during the first fill and each subsequent drain and fill event. The vent connection to the system should be located off the top of horizontal piping at a high point in the system; however, the vent connection can also be effectively located off the side of a riser or riser nipple at a high point in the system.
“Manual air venting valves should be accessible. The manual air venting valve should be located at an accessible point and preferably not over 7 ft (2.1 m) above the floor. Automatic air valves are not required to comply with the accessibility requirement of manual air venting valves; however, it is recommended the designer locate automatic air vents over areas without ceilings, above a lay-in ceiling, or above an access panel.
“Each wet pipe sprinkler system should be vented every time the system is filled.”
This is one of those items where what is in the standard means little and the annex material is nice but not legally enforceable. What a waste of text unless the owner’s representative wants this and is willing to pay for it to be done properly.
Three options are given. What option do you think almost every contractor is going to use? Think about the following:
(1) Manual valve – A 1⁄2-in. manual valve located “near a high point.” Wow, the cost of a valve that is located somewhere that might not be accessible for service. The annex material does discuss the accessibility requirement of the valve but none of this language made its way into the standard. Thus it is not enforceable. Also can someone please define “near”? What does that mean – in the same building, within 10 ft, within 6 ft? NFPA’s manual of style requires all language in the body of standard to be definable. The cost of this option is minimal and the practicability of this EVER being used – almost never.
(2) Automatic air vent – This is very definable and fairly easily accomplished. Again, the “near the high point” issue still applies. The cost is typically around $500 to install.
(3) Other approved means – Okay, what does that mean? Start talking to the Authority Having Jurisdiction (AHJ) to come up with something. The commit- tee is not helping you and the time you spend talking to the AHJ who probably has no ideas either will be wasted.
Obviously Option 1 will be used 99.9 percent of the time unless someone else requires specifies another method. I’m not saying that the idea of venting the air out of a system is not a good one, but this attempt by the committee to put enforceable language into the standard is worthless.
Hopefully, this will be cleaned up during the 2019 edition process. Until then, the owner’s representative is going to have to specify what they want to be installed. Notes and proper signage should be provided to document the location of all vents, both automatic and manual to ensure they are serviced and used when filling the system.
“7.2.6.6 Automatic Air Maintenance.
“7.2.6.6.3.1 – Each dry pipe system shall have a dedicated air maintenance device.”
The committee has been trying to state this for several cycles but engineers, designers and installers still are not following the intent of the standard. So the committee finally made it as plain as possible: Each dry pipe system (valve) must have its own dedicated listed air maintenance device unless paragraph 7.2.6.6.2 is applicable. Paragraph 7.2.6.6.2 is usually only applicable for the very small dry pipe systems.
“8.2.4 Floor Control Valve Assemblies.
“8.2.4.1* – Multistory buildings exceeding two stories in height shall be provided with a floor control valve, check valve, main drain valve, and flow switch for isolation, control, and annunciation of water flow for each individual floor level.”
“A.8.2.4.1 – It is not the intent of this section to require floor control valve assemblies in all multistory buildings. Where small buildings such as multilevel condominiums or apartments are under the control of a single owner or management firm, a single control valve should be adequate for isolation, control, and annunciation of water flow.”
“8.2.4.2 – The floor control valve, check valve, main drain valve, and flow switch required by 8.2.4.1 shall not be required where sprinklers on the top level of a multistory building are supplied by piping on the floor below.
“8.2.4.3 – The floor control valve, check valve, main drain valve, and flow switch required by 8.2.4.1 shall not be required where the total area of all floors combined does not exceed the system protection area limitations of 8.2.1.
“8.2.4.4 – The requirements of 8.2.4 shall not apply to dry systems in parking garages.”
While the language is not new for 2016, its location is new. This language was added during the 2013 cycle and its location (8.16.1.5) made the language difficult to find and most users missed it. For 2016, the commit- tee moved the language it so it would be much easier to find.
However, what is the committee trying to state in A.8.2.4.1? The body states one enforceable thought and the annex says that it’s not the intent in all multistory buildings… I’m confused!
“8.3.3 Thermal Sensitivity.
“8.3.3.1* – Sprinklers in light hazard occupancies shall be one of the following:” …
“(3) Quick response CMSA sprinklers
(4) ESFR sprinklers”
ESFR sprinklers designed to meet any criteria in Chapter 12 or Chapter 14 through Chapter 20 shall be permitted to protect any of the following:
(1) Light hazard occupancies
(2) Ordinary hazard occupancies
(3) Any storage arrangement in Chapter 13 referencing OH1, OH2, EH1, and EH2 design criteria.
Quick-response CMSA sprinklers designed to meet any criteria in Chapter 12 or Chapter 14 through Chapter 20 shall be permitted to protect any of the following:
(1) Light hazard occupancies
(2) Ordinary hazard occupancies
(3) Any storage arrangement in Chapter 13 referencing OH1, OH2, EH1, and EH2 design criteria.
Options 3 and 4 are new for 2016. While most users of NFPA 13 would not question using ESFR or quick response CMSA sprinklers over a light hazard space, the standard technically did not address this. This requirement was added to clarify this situation.
“8.4.7 Control Mode Specific Application Sprinklers.”
The requirement for internally galvanized steel pipe to be used for preaction and dry pipe systems has been deleted for the 2016 edition.
“8.10 Residential Sprinklers.
“8.10.2.2 – Residential sprinklers shall not be permitted to be used on ceilings with slopes greater than 8 in 12 or ceiling with heights greater than 24 ft unless specifically listed for this purpose.”
With these special construction features, the committee wanted the sprinklers specifically listed for these conditions.
“8.15.8.1 Bathrooms.
“8.15.8.1.1* – Unless sprinklers are required by 8.15.8.1.2 or 8.15.8.1.3, sprinklers shall not be required in bathrooms that are located within dwelling units, that do not exceed 55 ft2 (5.1 m2) in area, and that have walls and ceilings of noncombustible or limited- combustible materials with a 15-minute thermal barrier rating, including the walls and ceilings behind any shower enclosure or tub.
“8.15.8.1.2 – Sprinklers shall be required in bathrooms of limited care facilities and nursing homes, as defined in NFPA 101.
“8.15.8.1.3 – Sprinklers shall be required in bathrooms opening directly onto public corridors or exitways.”
What was deleted was the reference to “motels and hotels.” This is a significant change for NFPA 13 residential designs. Language was added to cover NFPA 101 requirements.
“8.15.8.2 Closets and Pantries.
“8.15.8.2* – Closets and Pantries. Sprinklers are not required in clothes closets, linen closets, and pantries within dwelling units in hotels and motels where the area of the space does not exceed 24 ft2 (2.2 m2) and the walls and ceilings are surfaced with noncombustible or limited-combustible materials.”
What was deleted was the reference to the least dimension 3-ft requirement. A sprinkler in a small closet or pantry does not care what the exact size of the space is. A sprinkler should easily to be able to contain a fire in a small closet or pantry regardless of the least dimension.
“8.15.25 Revolving Doors Enclosures.
“8.15.25 Revolving Doors Enclosures – Sprinkler protection shall not be required within revolving door enclosures.”
This should have been easily understood but questions were being asked.
“8.16.2.4.6* Main Drain Test Connections.”
“8.16.2.4.6.2 – Main drain test connections shall be installed that the valve can be opened wide for a sufficient time to assure a proper test without causing water damage.”
Again, this should have been easily understood but many were not doing this. The main reason a main drain test connection is installed is so that a main drain test can be performed. Usually 60 seconds is used as a minimum to allow the water supply to stabilize. If this is not done at the time of installation, the main drain test that is required by NFPA 25, Standard for the Inspection, Testing, and Maintenance of Water–Based Fire Protection Systems, is usually not completed and possible water supply issues are missed which can lead to failure of the system to control a fire.
“8.17.2 Fire Department Connections.”
“8.17.2.6.1 – The automatic drain valve shall be installed in a location that permits inspection and testing as required by NFPA 25.”
Again, this should have been easily understood but many were not doing this. If the automatic drain valve is not accessible, how can it be inspected and tested?
There are additional changes not covered in this article such as cloud ceilings, changes in annex table for commodities and hazards classifications and obstruction criteria. Look for future articles to cover these and additional topics. I do, however, challenge every one who has a stake in this standard to review the new edition by reading it. Make notes and provide input for the 2019 edition. A public input is always welcomed and more importantly it is needed to produce a quality document.
ABOUT THE AUTHOR: John Denhardt, P.E., is quality control manager for Strickland Fire Protection, College Park, Maryland. He has a bachelor of science degree in Fire Protection Engineering from the University of Maryland, holds NICET Level III certificates in automatic sprinkler system layout and inspection & testing of water–based systems, and is a registered P.E. in numerous states. He is a member of the NFPA 13 Sprinkler Discharge Committee, AFSA, NFPA, and is an SFPE fellow.
IMPORTANT NOTICE: The article and its content is not a Formal Interpretation issued pursuant to NFPA Regulations. Any opinion expressed is the personal opinion of the author and presenter and does not necessarily represent the official position of the NFPA and its Technical Committee.