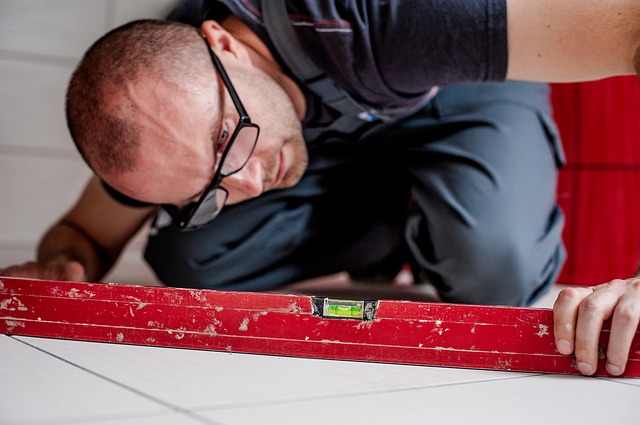
Standpipe Systems: Design and Installation Requirements
Although the requirements for standpipe systems are contained in the adopted building code and the installation requirements are contained within the referenced edition of NFPA 14, Standard for the Installation of Standpipe and Hose Systems, there is often disagreement between the responsible design professional, the fire protection contractor, and the Authority Having Jurisdiction (AHJ) on the proper design and installation of the system. This article will attempt to simplify the requirements for these systems by addressing the following issues:
- When are standpipes required and what are the installation requirements?
- When is a standpipe system required?
- What type of standpipe system is required?
- Where are the required hose outlets located?
- What is the required pressure at the hose outlet(s)?
- What is the required flow rate of the system?
- What are the requirements for the fire department connection (FDC)?
- Which outlets are flowed in a hydraulic calculation?
- How is the fire department apparatus defined and used in a hydraulic calculation?
Required Installation and Installation Requirements
During the design of a building two questions must be answered to determine the requirements for a standpipe system:
- Is a standpipe system required to be installed in the building?
- What are the installation requirements?
The requirements for a building standpipe system are contained within the adopted building code for that jurisdiction. In the majority of states and cities within the United States, the adopted building code will be an edition of the International Building Code (IBC), which may be adopted in full or adopted with modifications and then becomes the state or city building code. In Virginia, the current referenced code is the 2012 edition of the IBC, which Virginia amends into the Virginia Uniform Statewide Building Code (VUSBC). The current edition of the IBC is 2015, therefore all further references to the IBC will be to the 2015 edition.
The majority of installation requirements for a building standpipe system will be contained in NFPA 14 as referenced by the IBC. Chapter 35 of the IBC contains the applicable version of standards referenced within the text of the IBC. In the 2015 IBC the applicable version of NFPA 14 is the 2013 edition. All further references to NFPA 14 in this article will be to the 2013 edition.
When is a Standpipe System Required?
The pertinent section of the IBC is 905.3, “Required Installations.” Most standpipe systems are installed due to the requirement under Section 905.3.1, “Height.” It requires a Class III standpipe be installed throughout buildings where the floor level of the highest story is located more than 30 ft above the lowest level of fire department access, or where the lowest floor level is located more than 30 ft below the highest level of fire department vehicle access. (See Figure 1.)
The level of fire department apparatus access is defined as the actual location of the fire department apparatus relative to the building, not the access level for the fire department personnel entering to the building. (See Figure 2.)
Other uses for which the IBC requires a standpipe system are:
- A building that has an assembly occupancy with an occupant load exceeding 1,000
- Covered and open mall buildings
- Buildings that contain a stage greater than 1,000 ft2
- Underground buildings
- Buildings with a helistop and heliports
- Marinas and boatyards
- Rooftop gardens and landscaped roofs
If the building does not meet any of the eight criteria listed above, a standpipe system is not required by the IBC.
What Type of Standpipe System is Required?
NFPA 14 identifies three classes of standpipe systems: Class I systems designed for use by fire departments with 2 ½-in. hose connections, Class II systems designed for use by trained personnel or fire departments with 11/2-in. hose connections, and Class III systems designed for use by trained personnel or fire departments with both 1 ½-in. and 2 ½-in. hose connections. These systems can then be designed as a combination of a wet, dry, automatic, manual, or semiautomatic system as defined and required by NFPA 14.
Under IBC Section 905.3.1, “Height,” that requires a standpipe be installed throughout buildings as discussed previously, the required type of standpipe is a Class III system.
In most buildings the standpipe system can be designed as a Class I system due the provision of Exception I to Section 905.3.1 of the IBC for buildings protected throughout by automatic sprinkler systems. NFPA 14 permits Class I standpipe systems to be manual wet systems for buildings not classified as a high-rise, therefore all further discussions in this article will be based on the requirements for a Class I wet manual standpipe system.
Where are the Required Locations of Hose Outlets?
Once it has been determined that a standpipe system is required within a building, the next issue is the required locations of the hose outlets. The requirement for Class I hose outlet locations is contained in Section 905.4 of the IBC as follows:
- An outlet is required at the intermediate landings in all “required” interior exit stairways. If the stairway is not a required means of egress stairway, outlets are not required.
- The fire code official is permitted to allow the outlets to be located at the main landings in lieu of the intermediate landings.
- An outlet is required on each side of a wall adjacent to the exit in a horizontal exit.
- An outlet is required at the entrance from an exit passageway to other areas of the building.
- An outlet is required on the roof or at the highest landing of an interior exit stairway with access to the roof when the roof has a slope of less than 4 to 12.
- As required by the fire code official when the most remote portion of a floor is more than 150 ft (nonsprinklered) or more than 200 ft (sprinklered) from an outlet.
- An outlet is required in covered malls adjacent to each exterior public entrance and adjacent to each entrance from an exit passageway or exit corridor to the mall.
- An outlet is required in open malls adjacent to each public entrance to the mall at the perimeter line and adjacent to each entrance from an exit passageway or exit corridor to the mall.
Examples of the second and third locations can be found in the figures from NFPA 14. (See Figure 3 and Figure 4.)
What is the Required Pressure at the Hose Outlet(s)
The minimum design pressure for a standpipe system is contained in Section 7.8, “Minimum and Maximum Pressure Limits,” of NFPA 14. A hydraulically designed system is required to provide a minimum residual pressure of 100 psi at the most remote 2.-in. outlet on a Class I system. The 100 psi minimum requirement is based on the principle that most fire departments operate their interior attack handlines with combination nozzles, which are designed to operate at 100 psi residual pressure. Despite the nozzles being designed for 100 psi, the NFPA 14 requirement is not at the nozzle but at the inlet to the handline (literally at the outlet of the hose connection).
What is the Required Flow Rate of the System?
The required flow rate of a standpipe system is contained in Section 7.10, “Flow Rates” of NFPA 14. A Class I standpipe system is required to flow 500 gpm (gallons per minute) at the most hydraulically remote standpipe through the two most remote outlets. Previous editions of NFPA 14 have required that the most hydraulically remote standpipe be provided with two outlets at the top to provide the required 500 gpm flow. An additional 250 gpm is added for each additional standpipe in the building.
The maximum flow rate is 1,000 gpm for buildings protected throughout with an automatic sprinkler system and 1,250 gpm for buildings that are not. For a Class I horizontal standpipe system with three or more connections on any floor the minimum flow rate for the most hydraulically demanding horizontal standpipe is 750 gpm.
What are the Requirements for the Fire Department Connection?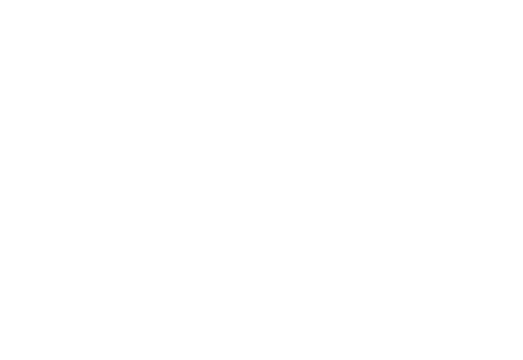
As with the standpipe system itself the requirements for the installation of the fire department connection (FDC) are contained in the IBC and NFPA 14. Section 912 of the IBC contains requirements on the location, inlet fire hose threads, access, and signage for the FDC. The main issue to remember with these requirements is that the final location of and access to the FDC shall be approved by the fire chief, which may not be the same individual as the fire code official mentioned previously.
Section 7.12 of NFPA 14 contains the installation requirements for the FDC. The most commonly misunderstood requirement during the system design and installation by both the designers and the local fire department is the requirement under section 7.12.3 that the FDC be sized based on the standpipe system demand and that one 2-½ inch inlet be provided for every 250 gallons per minute of design flow. Therefore, a standpipe system with a design flow of 1,000 gallons per minute is required to have an FDC with four 2-½ inch inlets.
The author once had a local fire chief state that the designed four 2-½ inch inlets were not correct and it should be replaced by a two 2-½ inch inlet. When the author explained that the four 2-½ inch inlet FDC was required by code, the fire chief responded that his firefighters would not know which two inlets to attach to, as their standard fire ground operations were to provide two supply lines to the FDC from the pumper. After a discussion on the system design and operation, the chief understood the requirement for the four inlets and planned to modify the department’s standard operating procedure and training for supporting buildings with standpipe systems.
Which Outlets are Flowed in a Hydraulic Calculation
The requirements for completing a hydraulic calculation for a standpipe system are contained in Section 7.10.1.2 of NFPA 14. The procedure is similar to the calculation method for a sprinkler system. To perform the system hydraulic calculation the required flow and pressure at the most hydraulically remote hose outlet is determined and the demand is calculated back to the city supply accounting for flows at additional standpipes, elevation changes, and friction loss through the system pipes and fittings, and fixed or mobile pumps.
As stated above, a Class I standpipe system is required to flow 500 gpm at the most hydraulically remote standpipe through the two most remote outlets. An additional 250 gpm is added at the most hydraulically remote outlet for each additional standpipe in the building, to a maximum of 1,000 gpm for a sprinklered building. If the standpipe calculated system demand is less than the supply, the design is acceptable.
An example of which outlets are required to be flowed to conduct the system hydraulic calculation can be found in the following figure. To meet the 500 gpm requirement at the most hydraulically remote standpipe 250 gpm would be flowed from outlets A and B. To meet the 250 gpm additional flow from each additional standpipe 250 gpm would be flowed from outlets C and D.
How is the Fire Department Apparatus Defined and Used in a Hydraulic Calculation?
In a manual standpipe system the local fire department apparatus is used to provide the water supply to attain the required 100 psi at the remote standpipe outlet. Even in a system with an automatic supply, hydraulic calculations are required for the FDC as if it were a manual standpipe. To determine the rated capacity of the pump on the apparatus the designer must contact the local fire department. Standard front line apparatus pumps are rated from 1,000 to 2,250 gpm, therefore if information on the local apparatus is not available a conservative design could use a pump rated at 1,000 gpm. The pump on the fire department apparatus is required to perform at a level of design as required by NFPA 1901, “Standard for Automotive Fire Apparatus.” NFPA 1901 requires that a pump on a fire department apparatus be able to achieve three characteristic points on the pump flow curve:
- 100 percent of rated capacity at 150 psi net pump pressure,
- 70 percent of rated capacity at 200 psi net pump pressure, and
- 50 percent of rated capacity at 250 psi net pump pressure.
Therefore an apparatus pump rated at 1,000 gpm will be able to deliver not less than 1,000 gpm at 150 psi net pressure, 700 gpm at 200 psi net pressure, and 500 gpm at 250 psi net pressure to the standpipe system. This “typical” curve is different from the typical curve for a stationary fire pump under NFPA 20.
The pump on the fire department apparatus is added to the hydraulic calculation after the fire department connection when calculating the system demand as stated above. At the fire department connection the flow is calculated back to the apparatus through the connecting hoses to the apparatus pump. The local fire department must be contacted at this point to determine their standard operating procedure for supporting a building standpipe system. Typical operations are to supply the fire department connection with 2-½ inch lines or 3-inch lines with 2-½ couplings, although some departments are known to use large diameter hose with Stortz connections. One method of determining the friction loss in fire hose for 2-½ inch rubber lined hose is calculated as FL = 2Q2L where:
FL = Friction Loss
Q = Flow rate in hundreds of gpm
L = Length of hose in hundreds of feet
And the friction loss in 3-inch rubber lined hose with 2-½ couplings is calculated as FL = 0.8Q2L
Assuming the local fire department standard operating procedure was to connect to the FDC with 100 feet of 2-½ inch line to each inlet, the friction loss in each line would be 2(2.5)2(1) or 12.5 psi.
These losses can be included in the hydraulic calculation as fixed losses between the fire department connection and the apparatus pump. Other methods of calculating friction loss in hoses are available and the designer should verify which method is acceptable with the Authority Having Jurisdiction.
Conclusion
In determining the requirements for and designing a standpipe system for a building the responsible engineer needs to know the requirements of both the local building code and referenced NFPA standard. In addition to these documents the responsible engineer needs to consult and work with the fire protection contractor and AHJs to ensure that all parties understand the design and installation requirements and that the design supports the responding fire department operational tactics.
ABOUT THE AUTHOR: Rick Alpert is a senior fire protection engineer with Clark Nexsen Inc., an architectural and engineering firm, in its Virginia Beach, Virginia office. He has over 32 years of experience in the design, construction management, and commissioning of public, private and commercial projects including projects for high-rise residential and office buildings. In addition to his engineering career Alpert has been involved with the volunteer fire service for over 40 years and has served in many leadership positions within local fire departments including those of vice president and chief. He holds several national certifications including ICC Building Plans Reviewer and Pro Board Fire Officer II.
What is the maximum pressure (PSI) for Class I standpipe? In nfpa 14,Section 7.8, described: minimum 65 psi at the outlet of the hydraulically most remote 11∕2 in. .on the other hand if piping length is too long, By considering pressure drop in the pipes to the final consumer, the pressure on the first branch will be high.
Is that specified In NFPA 14 maximum pressure limit for class I standpipe?
What is the maximum pressure (PSI) for Class I standpipe? In nfpa 14,Section 7.8, described: minimum 65 psi at the outlet of the hydraulically most remote 11∕2 in. .on the other hand if piping length is too long, By considering pressure drop in the pipes to the final consumer, the pressure on the first branch will be high.
Is NFPA 14 specified maximum pressure limit for class I standpipe?
There are two different pressure limits. One is on the overall system which is restricted to 350 psi. There is an allowance to go higher with the approval of the AHJ and the use of materials with the appropriate listing. The other pressure limit is at the hose connections. Section 7.8 is just the minimum required pressure despite the title also saying maximum pressure. For that, go back to section 7.2.3. It states the maximum pressure for a 2-1/2 is 175 psi and for a 1-1/2 is 100 psi.
Does each stair way requires individual vertical standpipe riser?
Or is it allowed to have single vertical combined standpipe and take horizontal standpipe in each level to connect to other 2 Hose connections by horizontal standpipe?
Each stairwell must have an individual standpipe as stated in section 7.4 (2013 ed). Each individual standpipe must have the ability to be shut down while still flowing water to the other standpipes on that floor level (see section 6.3.2)
NFPA-14 section 6.3.3 states that ” Listed indicating-type valves shall be provided at the standpipe for controlling branch lines for remote hose stations. If I has a hose valve that is tied into the “feed main” which connects the vertical standpipes and it is nearby the “feed main”, is this hose valve still considered to be remote and require a control valve at the “feed main”? And if it is not considered remote, how far or what conditions is considered remote?
please advise, NFPA-14 section 7.10.1 the value 500 GPM in the clause 7.10.1.3.2 for combined system shall be added to the maximum value given in clause 7.10.1.1.5 for non sprinklered throughout which is 1250 gpm, hence the maximum shall become 1750 gpm ?
The max is still 1250 gpm for unsprinklered building. The 500 gpm is assigned to the most remote standpipe then you add 250 gpm for each of the other standpipes until you reach you 1,250 gpm. That would require having 4 or more standpipes. If you only have 2 standpipes then the calculated amount is 750 gpm.
Roland Huggins, PE – Senior VP Engineering
American Fire Sprinkler Assn.
Dallas, TX
http://www.firesprinkler.org
Fire Sprinklers Saves Lives