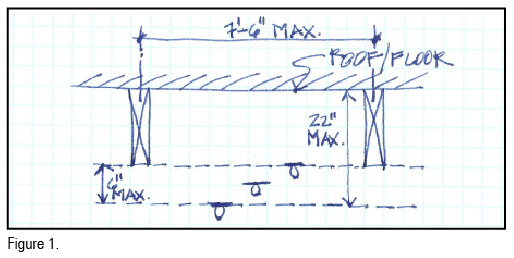
Spot the Dot
Part 1: What About the Z Dimension?
So, there I was, trying to enjoy a nice meal with my family. The restaurant was chosen by my princess because it was “fun” and had “cool things” in it. I should have known. Little did I know that I was going to be made to try and enjoy this family time while eating underneath a ceiling made up of the worst commodity classification found in NFPA 13, Standard for the Installation of Sprinkler Systems, short of flammable liquids and aerosols… Group A plastics.
How does someone in the fire protection industry deal with the never-ending challenges put forth by the architects of the world in their quest to make us “feel” something while we are in a space? For those of us in the sprinkler world, we usually take solace in knowing the mortality statistics that NFPA has published over the years regarding the overwhelming success of life and property that sprinkler installation affords us. As I sat there worrying about how far I was from the entrance that I came in from and where my second exit might be, the thought occurred to me: if a fire should start, what is my best chance of getting out of this place alive? And it was then that my quest for answers became focused on where and why do we put that dot where we do.
NFPA 13-8.1.1 (3) says… “Sprinklers shall be positioned and located so as to provide satisfactory performance with respect to activation time and distribution.” For me, the other eight descriptions listed for sprinkler installation are just side notes. In fact, earlier editions of this section simply said “… with respect to activation time and distribution.” If you think about it, for me, a better way to say this is “… with respect to sensitivity and discharge… ” You may not think there is that big a difference between these two statements, but, when put into the context of sprinkler spacing and location, it just seems more accurate to use the words sensitivity and discharge.
It is at this point that I must confess, my manic compulsive behavior will take over as I type the rest of this article, because you see, I cannot start talking about this topic without being consumed with emotion. For those of you taking the time to read this, you’re telling me that there is some level or degree of interest to know and understand why we put that dot where we do. However, for me, it is a certifiable passion. For those who know me, obsessed would be their description. For over 30 years I have struggled with this love/hate relationship that a designer develops with NFPA 13. While I love the design part and the satisfaction I get when I look at a completed piping plan (which for many designs, like a hospital, could be framed and hung on the wall in the category of eclectic art), I live for the struggle and conflict that I go through trying to follow the many “rules” I am made to follow to get there. You see, I am not good with rules. In fact, if you ask my father, if I had been born first, my sister would never had been born. Are all these rules necessary? Really?
Have you ever stopped to actually look at the pages of definitions there are in Chapter 3? Seriously, stop and look at them and ask yourself how is it you lived this long and not have known what the true definition of a bathroom is. Or, who knew that there was a difference between a flat ceiling and a horizontal one! I have to laugh sometimes when I wonder what other disciplines must think when they are exposed to some of these nuances sprinkler designers have to acknowledge, all in an effort to put the dot in the right spot.
But I digress. The question before us is: sensitivity and discharge – is one more important than the other? To answer this, I think you have to really understand the rules that govern spotting the dot. And a good place to start is with sensitivity. Through the years, I have had my share of “passionate conversations” with Authorities Having Jurisdiction (AHJs) and the like regarding water on the floor. But, the conversation goes silent the minute I bring up the question of sensitivity. The look I get when I ask an inspector, “When is the last time you climbed a ladder or rode in a lift up to the sprinkler to measure the deflector distance down from the deck?” is priceless. Listen to me, you can talk about spray pattern and floor coverage every day and twice on Sunday, but if the sprinkler does not activate what good is a perfect spray pattern! I think there are times we have our head so far buried into this chapter, we lose our focus. The fact is there is a significant weight to these two principles, and while the book puts them in the same sentence as if they are equally important, I would argue they are not. The scale of balance is absolutely tipped when you take a closer look, and to find that imbalance you have to know and understand the construction definitions and the rules that they are tied to
For anyone who has or is learning to spot the dot, a flat sheet of paper with a plan view of a space is staring them in the face begging for protection. And, while we have certainly progressed from the days of drafting boards and light tables, we are still looking at floor plans, even though they are digital. Certainly, the 3D world helps us better understand the space than years before, but the piping plan is still a plan view of a sprinkler system. So, no wonder floor coverage and spray pattern get all the attention. But, what about the Z dimension? What about the elevation of that dot? Seems many look at elevation with regard to centerline of pipe in their quest to “make it fit” rather than to “make it go off”!
So, where is it that we find these “sensitivity rules”? Turn in your book to 13-3.7 – Construction Definitions. That is right, I said construction definitions. It is the construction definitions that dictate the vertical distances involved with sprinkler layout. Here you will find two definitions: Obstructed (7.1) and Unobstructed (7.2). After reading these definitions, you will most likely be thankful for the pictures, especially those in the handbook, because the terms used can be confusing, especially to those not familiar with structural engineering or construction terms. The difference between these two categories may not be strikingly obvious or significant to other disciplines and trades, but for fire sprinklers it is arguably the difference between life and death. In fact, I will go so far as to say that if you do not nor cannot recite these definitions by memory, you have no business designing, plan reviewing or inspecting fire sprinkler systems. It is that important!
The first construction definition defined is “obstructed.” It is the harder one to remember of the two. In fact, learn this one first because “unobstructed” is very easy in comparison. Be careful, though. Do not confuse the use of the word “obstructed” as it refers to construction with that of “obstruction” to discharge. I know the annex and handbook supplements use the words spray pattern and obstruction in the same sentences and paragraphs, but this means two different things when it comes to sensitivity and discharge. When talking about construction, obstruction is a good thing. That’s right. I would rather be in a building of obstructed construction than that of an unobstructed one during a fire. Combustible or not. This is not obvious on the surface, because this is where many users tend to compartmentalize the standard and do not search for the connection between definitions and rules. If you put this together with the rules that reference these construction definitions, you will see that construction definitions actually define the vertical spot for the dot. Keep your finger in 3.7.1 and flip over to chapter 8.6.4.1.2. Here you find that in obstructed construction, you are given five options for deflector location depending on the type of obstructed construction you have. They are:
• 1-in. to 22-in. maximum from the roof deck and no further than 6 in. down from the bottom “plane” of the beams/joists/trusses that are considered obstructed construction. (See Figure 1.)
• 1-in. to 22-in. maximum from the roof deck with the deflector at or above the bottom “plane” of the beams/joists/trusses that are considered obstructed construction but only in the cases where you can meet the Beam Rule (8.6.5.1.2). (See Figure 2.)
• 1-in. to 12-in. maximum from the roof deck inside of every bay (or structural pocket created by the individual solid webbed members themselves) regardless of depth. (See Figure 3.)
• 1-in. to 6-in. maximum from the bottom of composite wood joists to a maximum of 22 in. below the roof deck. The only condition here is that the composite wood joists are firestopped into structural pockets of not more than 300 ft2. (See Figure 4.)
• 1-in. maximum below the bottom plane of concrete tee stem legs spaced less than 7 ft-6 in. on center. The nuance here is that the depth of the concrete tee leg is not considered. The deflector cannot be more than 1 in. below nor above the bottom of the stem legs unless, similar to number two, its horizontal location from the stem leg meets the Beam Rule (8.6.5.1.2). (See Figure 5).
So, if you draw this, it would look something like Figure 6.
As you can see, the deflector is below the bottom of the structural member considered to be obstructed construction. And, except for the case of deep chord bar joists, (top and bottom chords greater than 4 in.) all of them are solid webbed. Think about it. We are allowed to bring the sprinkler down as far as 22 in. from the roof deck! That is almost 2 ft! So what is it about this type of construction that lets us drop the “sensitivity” that low? The answer: solid webbing. Think about it. If heat is what we need to activate a sprinkler, then what better way to capture that heat than to create structural pockets using the solid webbed members to create boundaries, aiding in the collection of this heat, slowing it down, allowing the ambient temperature to raise whereby the sprinkler feels the heat and activates. It’s a beautiful thing for sure! The nuances or “exceptions” (a word we are not supposed to use anymore) to this telling feature are fire proofed bar joists and the deep chord bar joists. The rest are solid web. Oh, and keep going… realize that combustibility does not play a role here. We are talking about steel, concrete or wood.
Now, when applying the obstructed construction rules for deflector distance, you can end up with the deflector above the bottom of the lower chord or solid member, which is ok… but, it is then that you have to consider spray pattern or discharge, and move into the other use of the word “obstruction.” This will be discussed later in this series. For now, let’s just concentrate on the uncomplicated examples. As a picture is worth a thousand words, Figure 2 would be the illustration of obstructed construction and the rules that govern and rely on it.
Now, for the exceptions or nuances, if you will, that go along with this section. First is what I call the panel exception. That is, if the structural pocket described earlier, created by obstructed construction members, constitutes an area of 300 ft2 or less, then the spacing of the members can exceed the 7-ft-6-in. maximum of the basic definition. (See Figure 7.)
Another unique construction type found in obstructed construction is concrete tees. Years ago they were standalone but eventually found their way into the obstructed definition. Interestingly though, the “rule” that governs this type of construction remained the same. That being, the deflector shall be located a maximum of 1 in. below the bottom “plane” of the bottom of the tee legs. It can be up into the “channel” created by the tee legs, but only as much as the beam rule will allow. Keep in mind that this is regardless of tee leg depth. So, save yourself some grief and just install the deflectors at the 1-in. plane below the tee legs and move on. We will come back to this description later in this article but for now, memorize this rule. (See Figure 4)
So to summarize, the definition for “obstructed construction” can be refined to these three points with one nuance:
• Solid webbed member except for fire proof bar joists and deep chord open webbed joists,
• Maximum of 7 ft-6 in. spacing of these members and,
• Member spacing greater than 7 ft-6 in. when the structural pocket or panel created by the solid webbed members and associated girders or larger beams is no larger than 300 ft2.
When I teach this live, I include a little limerick to help commit it to memory. It goes like this: “one to 22, maximum of six; solid web to seven foot six.” And remember the nuances. Those being fire proofed and deep chord joists and the 300 ft2 panel pocket.
So, that’s the hard one. “Unobstructed construction” is much easier. One way to look at this is, if it is not obstructed then it is unobstructed. And the rule is very simple. The deflector distance is 1-in. minimum to 12-in. maximum below the ceiling plane above. (See Figure 8).
It is that easy. So, you would think that given the relative simplicity of these two rules, it would not be that big a deal to follow them. Unfortunately, I do not believe this is the case. In fact, I can walk into any big box store or light to ordinary hazard occupancy that does not have a ceiling and find at least three or more sprinklers that are not installed in the correct vertical distance from the ceiling plane.
Let me state the issue again just in case I was not clear enough earlier. We are not paying attention to deflector distance. Period. I am still confronted with installers, fitters and inspectors who think the only rules they need to pay attention to are for sprinkler spacing, that being 7 ft 6 in. off a wall and 15 ft between sprinklers. Those days were over more than 20 years ago!
I suspect this is because they view centerline of pipe only for installation purposes rather than the centerline being set because of required deflector distances and sensitivity. All too often I see typical grid branch-lines running in bar joists off a cross main and inevitably there will be a riser nipple that has been cut back because the centerline landed on a bar joists web. It is simple, it is faster and easier to cut back and rethread one end of a riser nipple than to cut a long one and prep and thread both ends with a new fitting. What happened when the riser nipple got cut back? Sure, the branch-line runs straight through the bar joist now, but my question is what happened to the deflector distance? Does that fitter understand what he has just done to the sensitivity of the system?
If the designer set that centerline at 12 in. using the size of the sprinkler to get him within the 12-in. maximum, there is a good chance that the deflector is going to be well past that distance now that the riser nipple has been cut back. Now we have an entire grid branch-line of sprinklers too far down from the deck.
Just a few weeks ago I was in a conversation with a fitter/foreman who could not remember where and when the 9-ft rule is allowed. So, why would we think that anyone would have any idea what the rules for deflector distances are let alone the level of importance it plays in the success of a system activating? My perception is that the only people who know and use the construction definitions and their associated rules are the designers. After that, all bets are off. And since the fitters are not being taught them and the AHJs are not checking them, we all go home thinking we have done a good job. Everyone is safe and sound in that occupancy because every square inch of floor space will get some water on it! OMG! Once again… the sprinkler has to activate in order for lives to be saved and buildings not burn down!
So, here is the challenge. For the next few days, wherever you go, look up and determine the construction definition on the spot. Then look at the deflector locations and ask yourself, are the dots in the right spot… or should you be looking for that second exit!
You will notice that in the 2016 edition of NFPA 13, even more rules regarding allowed “shadows” or dry spaces are being defined. It is borderline ridiculous, in my opinion, that we are going to this level of detail all because people are so hung up on water on the floor. Light and ordinary hazard occupancies, which make up well over 90 percent of our built and occupied environment, are weighed much more towards life safety than property protection. Let’s continue this discussion in the next edition, where we will discover that sensitivity and discharge are not as equal as they appear. One is more important than the other… and NFPA 13 and the building codes will prove it.
ABOUT THE AUTHOR: Steven Scandaliato is executive principal and managing director at SDG, LLC. He has over 35 years’ experience in fire protection engineering, design and project management covering all types of fire protection and life safety systems. He serves on the Technical Advisory Committee for the American Fire Sprinkler Association (AFSA) and represents AFSA as a member of the NFPA 13, 101 and 5000 committees. Nationally recognized, Scandaliato has become one of the most popular and sought after speakers on fire and life safety systems in the United States. He is published in several periodicals including articles for the NFPA Journal, Fire Marshals Quarterly and American Society of Plumbing Engineers. He is also a contributing author to the text published by NFPA/SFPE titled “A Designers Guide to Automatic Sprinkler Systems.” Over the last 18 years, he has presented seminars to thousands in contracting and professional associations including AFSA, the American Society of Plumbing Engineers, the American Institute of Architects, SFPE, the American Society of Sanitary Engineering and the International Fire Marshals Association. Scandaliato is a member of AFSA, NFPA, and SFPE.
IMPORTANT NOTICE: The article and its content is not a Formal Interpretation issued pursuant to NFPA Regulations. Any opinion expressed is the personal opinion of the author and presenter and does not necessarily present the official position of the NFPA and its Technical Committee.
EDITOR’S NOTE: Part 2 of this article will appear in a future issue of Sprinkler Age.