Continuing With the Z Dimension
That’s right… you read the last paragraph of my previous article in the September/October 2016 issue of Sprinkler Age correctly (see page 44 of that issue, or click here to see the blog post). Sensitivity and discharge are not equal in the eyes of the hazard. Oh sure, we use them together in our everyday conversations. Even Chapter 8 of NFPA 13, Standard for the Installation of Sprinklers, starts off by saying that sprinklers shall be spaced with regard to sensitivity and distribution. Sure, these are both important characteristics of fire sprinkler systems. So, where is the rub? What’s the big deal? Why do I think we need to separate these two characteristics and prove their inequality? Well, to answer that let me ask you a question. Why do we consistently have issues with Authorities Having Jurisdiction (AHJs) and other approving entities when it comes to interpreting this chapter? Why does every sprinkler association and NFPA get hundreds, if not thousands, of questions every year from practitioners and AHJs alike, asking for informal and/or formal interpretations regarding where you put the dot? Why the constant struggle with interpreting the rules of Chapter 8? Well, I’ll tell you why… money! That’s right… money!
I bet you thought it was going to be something deep and technical, even philosophical. But, alas, grandma was right! Money is the root of all [fire sprinkler] evil. Now, while I am incredibly tempted to dive into the entire subject of contracting at this point, I will exercise self-discipline, invoke every ounce of energy I have, and focus on the topic at hand. I told you that sensitivity and discharge are not equal. And I can prove it. But, more importantly, I want you to understand why this is such an important concept to grasp, especially when interpreting and applying these (sometimes ridiculous) rules.
Almost always, when teaching a new class, I start off by asking the question, “What are the two things that fire sprinklers do?” After the brief pause that everyone takes to evaluate if this is a trick question, someone will speak up and say “spray water.” Good answer. Yes, fire sprinklers spray water. That’s one thing they do. But what else? What is the second thing they do? What else happens as a result of them spraying water? Is it just about water hitting the floor? Sure, the water spray will pre-wet areas around the fire helping prevent or retard its growth, but what else is happening? I would even argue that it is even more important than the water hitting the floor! Give up? Okay, I’ll tell you…cooling! Yes, cooling! And in our world of light and ordinary hazard occupancies, the act of cooling is more important than water hitting the floor. This is not obvious at first glance or even the one hundredth glance. You have to be looking for it to see it.
Now, for some of you the idea of water not hitting the floor may be a new concept for you to consider or you may flat out disagree, which is okay because I am Sicilian and I learned at an early age that it takes some non-Sicilian people a little longer to catch on to new ideas sometimes. All I ask at this point is that you keep reading and hear me out before you decide to jump to the next article in this magazine.
Let me break this down more. Proving my point begins in the building codes, not NFPA 13, Standard for the Installation of Sprinkler Systems. The majority of the occupied space in the United States is light and ordinary hazard. That being the case, proving the hierarchy of sensitivity over discharge begins with where or what we use to identify these hazard levels. While most of us “dot spotters” started in the business by being handed a red book and told to learn it, most of us rarely ventured out of this red book. Why would we? Everything we need with regard to spotting the dot is in NFPA 13, so reading any other code or standard would be a waste of time since the majority of those “other” standards reference NFPA 13 anyway. There are two major building codes in the United States now, those being NFPA 5000, Building Construction and Safety Code, and the International Building Code (IBC), published by International Code Council. While there are several jurisdictions in the world that use NFPA 5000, the most popular ascribed to here in the United States is the IBC. All buildings that require a permit to be built are going to fall under some type of minimum code or standard and, more often than not, it is IBC. Not to get any deeper into this code than necessary, realize that the use of this building code begins with defining the occupancy. Sound familiar? It should, because that is exactly the first step we take in fire suppression system design as well – defining the hazard. And once the occupancy is defined, you find that all of the rules regarding that occupancy are in the chapters to follow. Rules like construction type, occupancy limits for overall area and height, separation from other occupancy types, etc. As you go further in, you find rules and limits for egress and exiting, and fire protection systems as well.
Now let me direct you to Chapter 3 of IBC which is the definitions chapter. Sound familiar? Yep, same as most every NFPA standard including 13… ironic for sure. You will see that each occupancy defined in this chapter is assigned a “Letter” designation. For example, the very first occupancy group defined is Assembly or “A” occupancy. There are several sub-categories for this occupancy (i.e., A1, A2, etc.). The next is “B” occupancies which represents “Business” occupancies and so on. Obviously, the letter designation coincides with the name of the occupancy group for the most part. Once the user determines the occupancy, the following chapters outline the rules, limitations and design guidelines allowed for each occupancy type. There are several topics that could be written from this point on with regard to the building code and fire sprinklers, but for the purpose of this article, I want to focus on the occupancy load. That is to say, the minimum number of people that the occupancy must be designed to or allowed in a given area of a specific occupancy group. That’s right, sensitivity versus discharge has everything to do with how many people are going to be in the room.
Earlier, I said the codes would prove my point. This is where it happens. If you look at Chapter 10 of IBC you will find the egress and exiting rules of which occupancy load is determined. The egress and exiting systems are designed and sized based in large part off the occupancy load (IBC 1004.1.2). There is a minimum number of people that these systems must be designed for of which can be augmented with the installation of sprinklers of course. IBC Table 1004.1.2 displays the minimum square foot per person that must be used based on occupancy type. For example, for business areas the minimum is 100 ft2 per person. But for a warehouse, it is 500 ft2 per person. So, what does this have to do with sensitivity? Well, this is where we will find the disparity behind sensitivity and discharge.
Let’s start with a B or business occupancy for our example. What hazard level is a business occupancy in NFPA 13? For most business occupancies, we can say it is considered a light hazard classification. That being the case, what are some of the rules in NFPA 13 that are specific to the sprinklers we use in light hazard occupancies? Well, among several the one I want you to get to is NFPA 13, section 8.3.3.1. In general, sprinklers installed in light hazard occupancies shall be fast response. Commonly we associate this with quick response but it can also mean residential, some CMSA (control mode sprinkler application) and ESFR (early suppression fast response) sprinklers. What does fast response mean? Un-technically speaking, it means that while you may have two sprinklers side by side – one is fast response and one is standard response – and they are both 165°F temperature sprinklers, the fast response will activate before the standard response. Or in other words, the fast response sprinkler will “feel” the heat faster than the standard response will. Another way to look at it: if you have two copper pots and fill one full and one half full and put them on the stove with the same amount of heat under each, which one boils first? Obviously, the one half full. Hence, the “skinny” red glass bulb versus the “fat” one. Same red color, meaning same temperature rating, just one will see 165°F quicker than the other. Again, the book says “shall,” meaning mandatory. So light hazard occupancies shall be fast response sprinklers.
Okay, now contrast that with an “S” occupancy from the building code: a storage or warehouse occupancy. We normally associate warehouse occupancies with “special” or extra hazard classifications. If you look at the occupancy load factor for that type in Table 1004.4.2 you find the minimum load to be 500 ft2 per person. This means a warehouse load is significantly lower to that of business occupancy. And what does NFPA 13 say about the type of sprinklers that shall be used in warehouses with this type of hazard classification? That’s right… you shall not use fast response sprinklers! So, think about this with the characteristics of both these types of occupancies. In fact, if you look at this table with the hazard definitions side by side, you’ll find the correlation between these two documents, even though they were not necessarily written to work with each other.
What you’ll find is that the occupancies that coincide with NFPA 13 for light hazard are occupancies that have very high occupancy loads and vice versa. Those occupancies that are high hazard occupancies if much lower occupancy loads. Another way to say this would be light hazard is a lot of people without a lot of stuff and extra hazard is less people with a lot of stuff. But, more importantly is look at the sprinkler requirements! Light hazard (lots of people) shall have fast response sprinklers and extra hazard (lots of stuff) shall not have fast response sprinklers.
Get it? There it is, we want fast response sprinklers or a higher level of sensitivity when we have lots of people and we want a lower level or, more prudently, a more deliberate level of sensitivity when we have lots of stuff but not a lot of people.
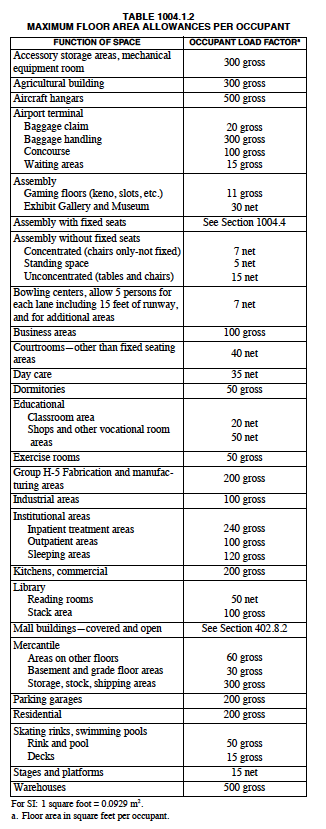
So, to bring this back around full circle… now you see that NFPA 13, while certainly looking for both sensitivity (sprinkler activating within an acceptable time frame) and discharge (a decent and as unobstructed spray pattern as possible) certainly is more concerned about the sprinkler going off when it comes to occupancies with lots of people, than water on the floor. Why?… cooling. We want to keep the space tenable for as long as necessary to give this higher occupancy load a chance to exit.
To further prove my point regarding the weight of sensitivity versus discharge, let’s look at a few of the obstruction rules (obstruction to spray pattern not obstructed construction) that show this imbalance even more. First, let’s be very clear the what is about to be discussed is with regard to light and ordinary hazards only! Don’t go running off and applying this to extra or special hazards because it is a different mind set when you get into these higher hazard occupancies.
Those who know me know that my most favorite rule in all NFPA 13 is the one associated with distribution obstructions, commonly and lovingly known as “the 4-ft rule.” Paraphrased, this rule says, “thou shalt put a sprinkler under ‘anything’ that is greater than 48 inches in width.” Now, I would love to expound on where this rule originated, and if you want to know and you have 30 minutes, call me. I’ll be happy to tell you the story. Save it to say, the rule has been around since the 19th century edition of this standard! So, obviously, it has survived only because no one has died and no buildings have burned down due to a fire under an obstruction less than or equal to 4 feet, even though the rule is being applied way outside of the scope to which it was originally intended to be used. Be that as it may, in the world of codes and standards, this means the rule must be a good rule. This is why codes and standards always get bigger and not smaller. Keeping this in mind, let’s review the rules associated with the pattern development obstructions, commonly referred to as the “3 times rule.” Paraphrased, this rule says that an obstruction that is below the plane of the deflector but within 18-in. down from the plane of the deflector is considered a pattern development obstruction and must be a minimum of 3 times the greater dimension of the obstruction away from the deflector in order not to be considered an obstruction. The interesting part of this rule is that it stops after 24 inches (except for vertical obstructions added in the 2016 edition). That’s right, after you are more than 24 inches away from the object measured directly from the closest edge of the obstruction to the sprinkler deflector the rule stops, meaning NFPA 13 does not consider it to be significant enough to hinder the formation or adequacy of the sprinkler discharge. I prefer you just say, “It’s not there!” Think about that a moment. Seriously. This is huge for inspectors if you would just stop and think about it for a moment. What this means is that, as you walk around during your rough-in or final acceptance testing looking at sprinkler locations and you see ducts, fixtures, structural components, etc. that are located around a sprinkler, you simply ask yourself:
- “Is the obstruction within the first 18 inches down from the plane of the deflectors or the sweet spot?”
- “If yes, then is it more than 24 inches away?”
- “If yes, then poof… it’s not there!” and go onto the next sprinkler.
If it is less than 24 inches, then time to gear up and get your tape measure out or have the fitter get on a lift and spot check those for compliance with the 3 times rule. I think you’ll find that your degree of accuracy for these all-important inspections will step up tenfold just by memorizing this pattern development rule. (See Figure 1 below).
But, now comes the best part. By combining the 4-ft rule (discharge obstruction) with the 3 times rule (pattern development) you will see the imbalance or weight of importance that is placed on these two sprinkler characteristics. If we have an HVAC duct that is 48-in. wide (not greater than 4 ft) and all or a portion of it penetrates our sweet zone or 18-in. sensitivity zone below the plane of the deflector, the top of which is not higher than the plane of the deflector, meaning we can throw water over the top and under the bottom of it and it is 25 in. away? That’s right, it is not there! Our own NFPA 13 rules are telling us to what degree or level of significance discharge or water on the floor is when it comes to light and ordinary hazard occupancies. Obviously, there is going to be a shadow on the floor. But, because it is (shall be) a fast response sprinkler, its sensitivity will be the life saver. Given this occupancy full of people has obstructions to spray patterns does not mean my life is at risk. As long as the sprinklers are installed in the Z dimension correctly, the mere activation of the sprinkler is going to begin the process of cooling and pre-wetting, whereby the fire growth is retarded, allowing the occupant-loaded space ample time for safely exiting as well as time for the fire department to arrive with their big, strong firemen carrying big hoses to actually extinguish the fire. This is why I am making the point that maybe we spend our time together passionately discussing the sensitivity of a sprinkler in a certain location rather than the whether or not water is going to make it to the floor. Again, light and ordinary hazards.
For sure, great care should be applied to obstructions to spray pattern in the higher hazards. In fact, many a test has been conducted proving the failure of sprinklers, even big bad K25s, etc., in warehouse hazards with the spray pattern of just one sprinkler being obstructed by the bottom chord of an open web bar joist, prompting special rules for storage and higher hazard sprinkler applications.
So, again, here is the challenge. We all want to save lives and property. But recognize that those goals are weighted with guidance based on occupancy (determined by the building code) and associated hazard (determined by NFPA 13). Hence, no matter what capacity your involvement is with spotting the dot, make sure you can recognize the construction definition and sleep well knowing that you paid attention to the Z dimension, giving all of us the best possible chance for the sprinkler to activate when needed.
ABOUT THE AUTHOR: Steven Scandaliato is executive principal and managing director at SDG, LLC. He has over 35 years’ experience in fire protection engineering, design and project management covering all types of fire protection and life safety systems. He serves on the Technical Advisory Committee for the American Fire Sprinkler Association (AFSA) and represents AFSA as a member of the NFPA 13, 101 and 5000 committees. Nationally recognized, Scandaliato has become one of the most popular and sought after speakers on fire and life safety systems in the United States. He is published in several periodicals including articles for the NFPA Journal, Fire Marshals Quarterly and American Society of Plumbing Engineers. He is also a contributing author to the text published by NFPA/SFPE titled “A Designers Guide to Automatic Sprinkler Systems.” Over the last 18 years, he has presented seminars to thousands in contracting and professional associations including AFSA, the American Society of Plumbing Engineers, the American Institute of Architects, SFPE, the American Society of Sanitary Engineering and the International Fire Marshals Association. Scandaliato is a member of AFSA, NFPA, and SFPE.
IMPORTANT NOTICE: The article and its content is not a Formal Interpretation issued pursuant to NFPA Regulations. Any opinion expressed is the personal opinion of the author and presenter and does not necessarily present the official position of the NFPA and its Technical Committee.
EDITOR’S NOTE: Part 1 of this article appeared in the September/October 2016 issue of Sprinkler Age.