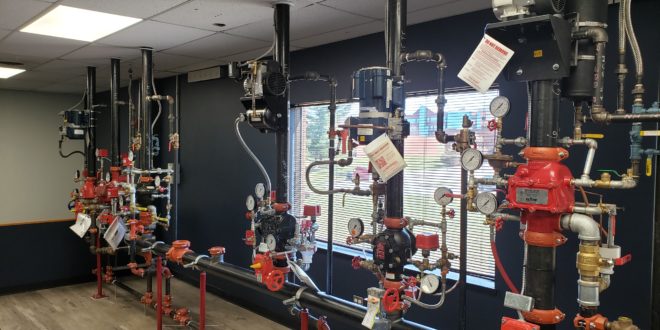
Selecting Air Compressors
What You Need to Know
Fire protection air compressors are not often looked at closely by designers and installers, but when the wrong type of compressor is used the facility manager gets very familiar with them. A little work and a little education on the front end of an installation will ensure a long and problem-free life for the compressor. That is what this article is designed to provide.
Below is a list of questions that will serve as a guide to help you choose the correct type of air compressor for your fire sprinkler installation. Hint: “Stop by Home Depot and grab the cheapest one” is not the answer to any of the questions.
• What is the size of the largest system size in gallons? Sizing by horsepower wastes money!
• How many systems will the air compressor be serving? Three systems per compressor is ideal.
• Should you use a riser mount or a tank mounted air compressor?
• Does the facility have a solid maintenance schedule in place for the air compressor?
• In what type of environment will the air compressor be installed?
• Who is taking ownership of the electrical responsibilities of the air compressor at installation?
If you can answer all or most of these questions before the installation takes place, you can be sure to have provided a long-lasting, trouble-free air supply solution for your project.
What is the largest system size in gallons? The primary driver of air compressor selection is the NFPA 13, Standard for the Installation of Sprinkler Systems, code requirement for a “30-minute fill.” Most information on fire protection air compressors in the market will provide a capacity rating in gallons (i.e., OL12516AC is a common model that is rated to fill a 125-gallon system or less to 40 psi in 30 minutes or less). The capacity rating in gallons is calculated using an equation that takes into account flow and pressure over time. It is the flow part that is key here.
Fire protection air compressor manufacturers are concerned with high flow, not horsepower. Conversely, a retail type of air compressor—the type you would find at a home improvement store—is concerned more with pressure and horsepower, not flow. This is because these compressors are built to different quality standards and for different purposes.
A fire protection air compressor is designed to last for the life of the system and will typically have a run life of 5,000 to 8,000 hours. Retail-quality compressors have a run life between 500 to 1,000 hours. Also, a fire protection air compressor will typically have a very high flow when compared to the retail type. The reason for this is that a fire protection air compressor is designed to fill the sprinkler system to pressure in 30 minutes with the smallest possible horsepower. Next time you are at Home Depot, look at the flow for one of the compressors they sell, then pull up a cut sheet for your favorite fire protection air compressor and look at the cubic foot per minute (CFM) compared to the horsepower – you will see a sizeable difference.
So, why does knowing your largest system size in gallons save you money? Because there is a big difference in price between a one-horsepower retail type air compressor and a one-horsepower fire protection air compressor. When you make sure that you have sized your fire protection air compressor by flow and system size, the price difference is often small – and as an added bonus you will get a piece of equipment that will last the life of the system as opposed to one that will struggle to last the life of the install warranty.
How many systems will the fire protection air compressor be serving? There is no restriction in NFPA 13 on the number of systems that one fire protection air compressor can serve. If you want to put one air compressor on 20 dry systems, no one can stop you. Someone should, but technically they can’t. The reason to consider the answer to this question is to ensure long-term performance and reduce regular maintenance.
The more systems that are attached to one air compressor, the more it will need to run to keep up with the leak rate of each system. If you were to put one compressor on 20 systems, be aware that your air compressor will be running constantly to keep up with demand – expect it to become problematic fairly rapidly. Also be aware that this issue is magnified significantly with the use of a nitrogen generator – important to know but a separate topic.
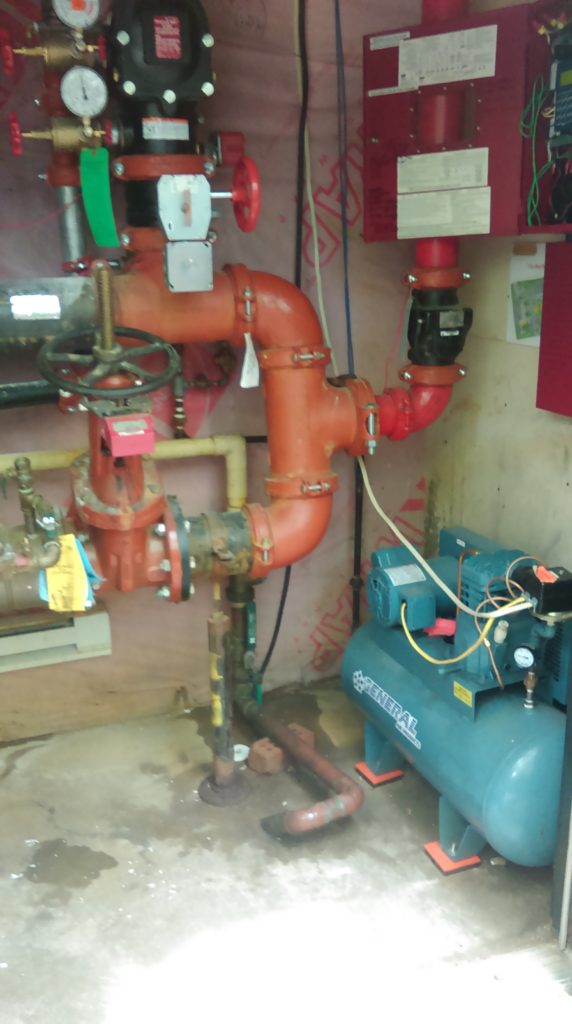
FM Global offered a recommendation for one air supply unit per three systems when it came to freezer rooms. This is a good guideline to carry over into all dry and pre-action sprinkler systems as it will protect the life expectancy of the air compressor. Furthermore, the more a compressor runs, the more maintenance will be required. By putting no more than one air compressor per three systems you will keep the run time of the air compressor to a manageable amount as the system ages.
When should you use a riser mounting versus a tank mounted fire protection air compressor? If you are connecting one air supply to multiple risers it will require the use of a tank mounted air compressor and code states that each system attached to the air compressor requires its own air maintenance device. Really, a tank mounted air compressor is the best option when it comes to air supply no matter the number of systems.
When should you use a riser mounting versus a tank mounted fire protection air compressor? If you are connecting one air supply to multiple risers it will require the use of a tank mounted air compressor and code states that each system attached to the air compressor requires its own air maintenance device. Really, a tank mounted air compressor is the best option when it comes to air supply no matter the number of systems.
When you use a tank mounted type air compressor it allows you to introduce extra volume to your systems. Consider this set up – three risers, two require 20 psi and one requires 40 psi. The use of a tank mounted air compressor allows first for the use of one air compressor, where as the use of riser mounting compressors would require three. Furthermore, you have the ability to set the tank mounted air compressor for its highest setting – 60 to 100 psi is common. Then, use the air-maintenance devices to regulate down to the pressure required for each system. The increased stored pressure means that the air compressor will run less frequently and this will help the unit to last for a long time before replacement is required.
Riser mounting air compressors are best for riser rooms where there is no space for a tank mounted unit. Typically, they perform very well on new, small systems. Also, note that riser mounting air compressors do not have to be mounted on the riser. Check with the manufacturer’s instructions for proper orientation but understand that in situations where the riser is not ideal for mounting contractors should consider mounting the compressor on the wall or the floor.
Does the facility have a solid maintenance plan in place for the air compressor? A solid maintenance plan is the key to a successful operation of all durable goods – a fire protection air compressor is no different. Answering this question before choosing an air compressor for a new installation will tell you if you should be purchasing a lubricated or an oil-less type unit.
Oil-less and lubricated are the terms used for the two primary types of compressors seen in the fire sprinkler industry. Lubricated type air compressors are less expensive than oil-less types on the initial purchase. Under usual circumstances, if maintenance is not performed on a lubricated air compressor it will break quickly. One of the most common failures of these units is simply neglecting oil changes. If the oil is not looked at regularly and changed appropriately, the pump will seize and the unit will fail.
If your customer has a good track record for maintenance, a lubricated type of air compressor can be a good choice. If the maintenance record for the facility or building owner is in question, an oil-less type compressor is the best choice. While oil-less units are not “set it and forget it” by any means, they are designed to run optimally with far less maintenance.
Be sure to ask yourself this question before you select a compressor type: a neglected lubricated air compressor that runs regularly will require an oil check inside of the first year!
In what type of environment will the air compressor be installed? This question goes hand-in-hand with the question of maintenance. Is the environment dirty or clean? If it is dirty, an intensive maintenance regiment is recommended. Clogged intake filters are another common failure point on air compressors – this affects both oil-less and lubricated type air compressors equally. Also consider the environment from the standpoint of what the compressor is intaking – is it in a janitor’s closet with chemicals? How will those chemicals affect the compressor? Ammonia and air compressors are not friends. Is it near a body of salt water? That is as corrosive to the inside of the air compressor as it is to the outside of the sprinkler piping. Is the compressor installation heated area? An air compressor needs to be installed in a part of the building that never goes below freezing.
If the compressor installation area is clean, you should also look into the intended use of the area. If it is going to be in or around an area where people will be living and working, a quiet fire protection air compressor should be used.
Who is taking ownership of the electrical responsibilities of the air compressor at installation? When we talk about fire protection air compressor issues we can not leave out electrical issues. The air compressor is the crossroads for the mechanical and electrical disciplines on a dry pipe or pre-action sprinkler system. The competence of the electrician is as critical to a fire protection air compressor installation as the competence of the sprinkler tech. At initial installation, if the electrician improperly wires the air compressor, nine times out of 10 the fire sprinkler contractor will be paying for it. Often, an electrical problem with the compressor will not produce a failure of the unit until weeks or months later.
It’s not fair; it’s just real life. Without delving too deep into that unfortunate reality, a good practice to avoid electrical problems all together is to find out who is doing the electrical installation and touch base with them. Make sure they have someone with experience wiring industrial equipment. Be there when they are wiring the compressor and make sure to have the phone number for the manufacturer of the air compressor on stand-by so that you can consult them should any problem arise.
So, for a piece of equipment that usually appears in design drawings as a square with “COMPRESSOR” written inside, this is a long article. Believe it or not, this is a summary. There is a lot to cover on the proper selection and use of fire protection air compressors. We are all working to be better at what we do, so the number one thing to take away here is that training is vital – there is a lot to know about the less glamorous components of a fire sprinkler system. Learn more. Train more. Work smarter.
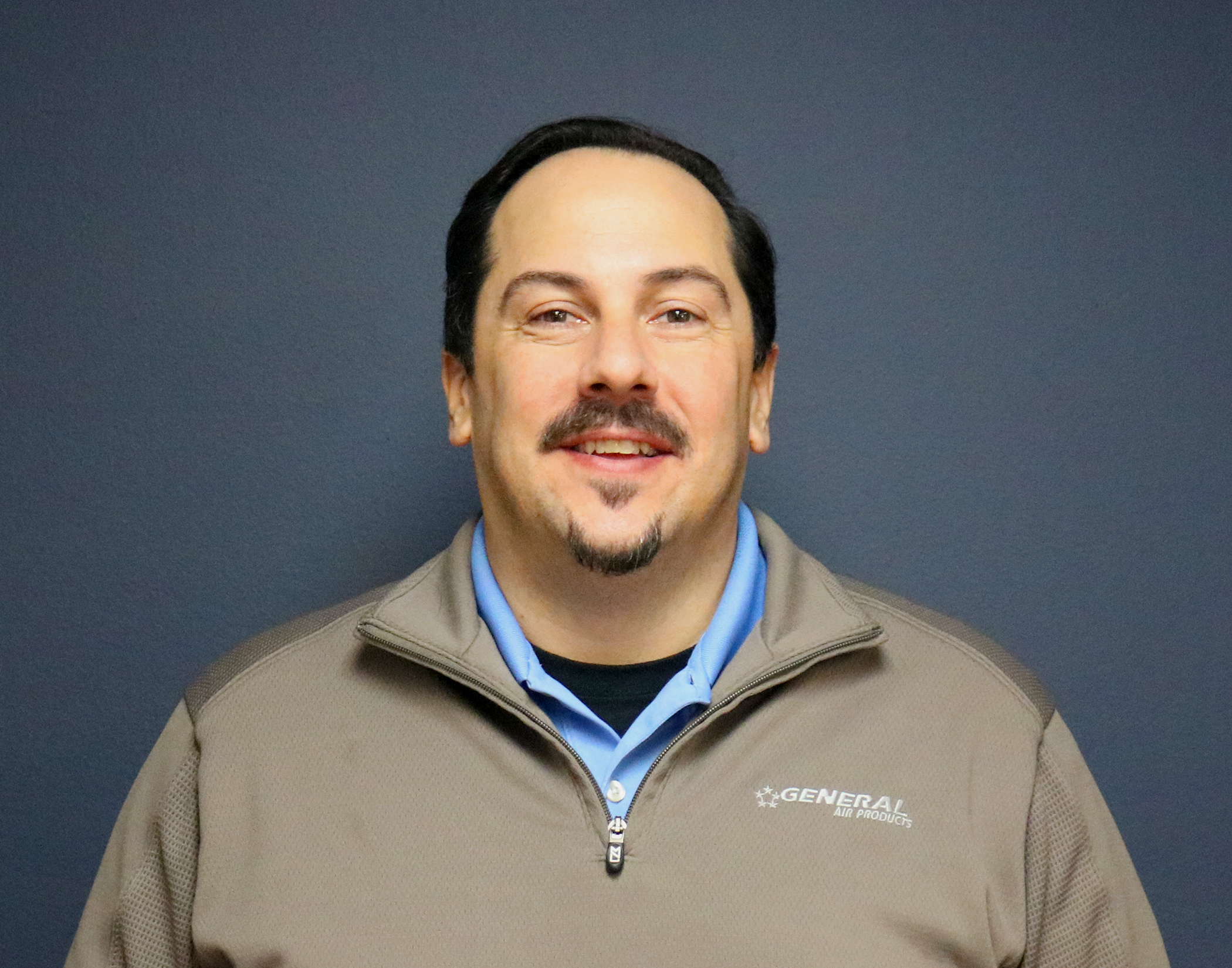
ABOUT THE AUTHOR: Ray Fremont, Jr. is the national sales and marketing manager for General Air Products, Inc., Exton, Pennsylvania, and a member of AFSA’s Manufacturers/Suppliers (M/S) Council. He can be reached via email at rmfjr@generalairproducts.com.
IMPORTANT NOTICE: The article and its content is not a Formal Interpretation issued pursuant to NFPA Regulations. Any opinion expressed is the personal opinion of the author and presenter and does not necessarily present the official position of the NFPA and its Technical Committee.