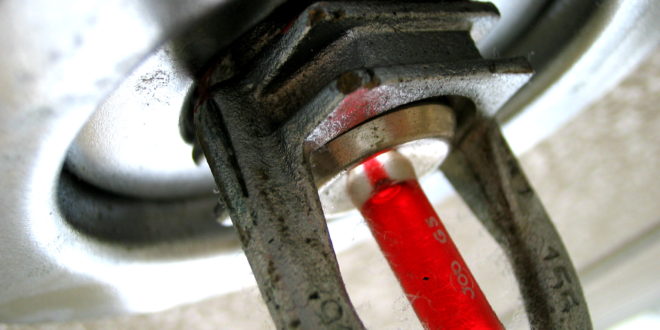
Listed Spray Sprinklers
What Else the Testing Tells Us
A common part of our industry is the use of Listed components. Other than the general understanding that this requirement provides a level of confidence that the devices will work, we typically don’t give the subject a lot of thought. There are multiple aspects of the underlying tests, though, that can shed light on other sprinkler discussions. Since spray sprinklers are the workhorse of our industry, this article will focus on UL 199, Standard for Safety: Automatic Sprinklers for Fire Protection Service. There are over 100 pages in this document and an amazing number of characteristics tested, of which only a small portion will be addressed. To further help reduce the information, the focus is pendent sprinklers with a 5.6 K-factor.
Let’s start the discussion looking at the exposure to pressure. Have you ever had someone express concerns about exceeding 175 psi when doing the hydrostatic test? Typically, we simply say that NFPA 13, Standard for the Installation of Sprinkler Systems, dictates doing it. Now you can add that it is exposed to much greater pressures for its listing. As part of the leakage test, the pressure is increased quickly (not greater than 300 psi/minute) to 500 psi (all values are for sprinklers with a rating of 175 psi), it’s held for one minute, and then checked for leaks. It’s also tested for rupture (which includes its operating or releasing any operating parts) by exposing it to 700 psi for one minute. If you think a minute is too short, there’s also a 30-day test at 300 psi. The rate of exposure is controlled since resisting water hammer is a separate test. It exposes the sprinkler to pressure spikes of 500 psi at a rate of 60 cycles per minute. This goes on for 100,000 cycles (almost 28 hours). There can be no signs of physical damage nor observed leaks during the test. In addition, at the conclusion of the test, it’s exposed to the leakage test. In closing this piece of the discussion, allow me to emphasize that this is not a basis for arguing that it is okay to design to pressures slightly higher than the rating of the components. Although the sprinklers won’t fail, the rating should be viewed as a wall versus a line drawn in the sand.
Next let’s look at the K-factor. For those who have been at the game a little while, back in the 1996 edition, we calculated the flow with a specific K-factor that was defined in the manufacturer’s cut-sheet. This perceived precision allowed some sprinkler models to require less pressure. In the 1999 edition, this was changed to a nominal K-factor. Considering how it’s determined, it’s interesting that it was ever so specifically defined. The K-factor is calculated by measuring the flow at a multitude of pressure points. It starts at 7 psi, goes to 10 psi, then increased in 5 psi increments to 50 psi, and finally increased in 10 psi increments to 100 psi. Since 15 test points is obviously not enough, the test is continued by decreasing the pressures in the same pattern. The K-factor is calculated at each point then averaged. The values vary and can go outside the range dictated by NFPA 13 but not by very much since all values must be within 5 percent of the average. For example, if the average were 5.3, individual points could be as low as 5.035 and no higher than 5.565. A final note addresses dry-type sprinklers. Although they can be up to 4-ft long, the K-factor is calculated using the shortest length available from the manufacturer.
Another item that occasionally pops up is the discussion on engineering the density needed to control the fire. Ignoring the issue about the ability to fire model the interface between the water droplet and the fire, let’s talk about the ability to identify the density hitting the floor. Let’s first look at how well the water stays within the parabolic shape of the sprinkler discharge. We can answer this question by looking at the 10-pan distribution test. It uses a single row of 12-in. x 12-in. pans located 4-ft below the deflector that rotates at one revolution per minute. At this level, the acceptable discharge pattern is a 16-ft diameter circle. With 15 gpm flowing (for up to a K-5.6 and 21 gpm for K-8.0), the test is run for 10 minutes or until any one pan is full. The density for each pan is then calculated. The criterion for this test is that the density beyond the 16-ft diameter (the eighth pan) cannot exceed 0.03 gpm/ft2. With an average density inside the 16-ft circle of 0.746 gpm/ft2 that means the worst case scenario (that being both the ninth and tenth pans being at 0.03 gpm/ft2 with a cumulative 0.06 gpm/ft2) would be about 92 percent of the water inside the 16-ft dimension. This test, though, doesn’t tell us what the distribution is throughout the area. The pan is rotating so it will tell us the average discharge by distance from the center but it can’t identify if there are dryer or wetter portions throughout each arc of the circle. Additionally, there is no defined tolerance on the density between the pans inside the 16-ft diameter. There is an additional distribution test using 16 pans that identifies the minimum collection across the area. The 12-in. x 12-in. pans are grouped as a 4-ft x 4-ft box located 7-ft 6-in. below the deflector. This test requires a minimum average collection for all the pans (of 0.15 gpm/ft2 for a K-5.6) and no individual pan can be less than 75 percent of the assigned density. This doesn’t help define the density per individual square foot of floor space because the pans are centered between four sprinklers with a 10-ft x 10-ft spacing. As such, it is collecting water only from the outer half of the discharge pattern (with the first pan being a little over 4 ft from the centerline of a sprinkler) and there are varying degrees of overlapping discharge from the multiple sprinklers. The bottom line is that we know we are getting a good distribution of water but we cannot say with precision what is really hitting any particular portion of the floor.
Let’s now turn our attention to tests that look at sprinkler performance. This consists of activation and ability to control the fire. A quick look at activation covers the temperature rating and thermal sensitivity. The temperature rating is verified with a bath test that uses water for lower ratings and oil for higher ratings (>175°F). The sprinkler is placed in the bath which is then heated at a convenient rate (great phrase) until it is within 20°F of the rating (for higher ratings it’s within 30°F). It’s then raised at a sedate one degree per minute until it activates. The criterion is that it must be within 3.5 percent of the rating (for sprinklers rated up to 400°F). So if it’s rated at 175°F, it must operate between 168.9°F and 181.1°F. The next step is the thermal sensitivity. This test uses an air oven (effectively a looped ducted assembly) where the temperature and air velocity are controlled. This allows the response time index (RTI) to be verified based upon the time to activation. A 175°F quick-response sprinkler must activate within 12.1 seconds whereas a 212°F quick-response sprinkler can take 18.2 seconds (both use the same air temperature of 386°F). A 175°F standard-response sprinkler cannot operate faster than 19.4 seconds (that equates to an RTI of 80) nor slower than 84.8 seconds (that equates to an RTI of 350). This puts into perspective how much greater an impact the RTI has on activation than temperature rating.
Finally, let’s move on to the test that evaluates the ability to control the fire. This is just for spray sprinklers (with up to a 8.0 K-factor with larger K-factors being addressed by the storage tests) that effectively address use with the occupancy hazard approach. It’s the 350-lb wood crib fire test. Sprinklers listed for storage are subjected to a larger fire in a rack assembly (granted the lower density storage applications use the standard spray sprinklers without a storage fire test). The wood crib is 4ft x 4ft and 21-in. high and constructed of layers of 2 x 4s, 4 x 4s, and 4 x 6s. There are large air gaps between the lumber and the alternating layers are rotated 90 degrees. This creates a lot of surface area and airflow presenting a robust fire. The impressive part is that there is an atomizing heptane torch beneath the crib that is flowing 0.9 gpm (burning the duration of the test). Just like the 16-pan fire test, there are four sprinklers spaced at 10 ft x 10 ft and the crib is centered between them. The test is run twice with each sprinkler discharging 15 gpm for one and 25 gpm for the other (with larger flows for larger K-factors and extended coverage sprinklers). Although it’s easy to assume that if it passes at the lower flow, it will always pass at the higher flow. That’s not always the case. Though rare, there have been cases where the increase in pressure changes the discharge pattern enough to fail the test. The test is run for 30 minutes with the sprinklers turned on after one minute from igniting the torch or the ceiling temperature reaching 1,400°F. The criteria are that the wood loss cannot exceed 20 percent and the ceiling temperature must be no more than 530°F above ambient within five minutes of starting sprinkler dis- charge. The temperature can oscillate around this value but it cannot exceed it for more than three consecutive minutes and the overall average cannot exceed it.
There are a ton of other tests that provide assurance that sprinklers will reliably operate for a long period of time. An understanding of these other tests can also shed some light on other aspects of the industry such as the basis for the allowed activation times on quick-response sprinklers for the 20-year field service test.
ABOUT THE AUTHOR: Roland Huggins, PE is senior vice president, engineering & technical services for the American Fire Sprinkler Association (AFSA). As part of the executive team he provides guidance on external operations regarding technical elements within the industry. His primary roles include defining technical positions for AFSA, direct- ing the effort to improve the NFPA standards that drive the installation and maintenance of water-based fire protection systems covering 28 NFPA standards and 38 representatives, as well as oversight on all technical services in support of AFSA members. Roland is a graduate of the University of Maryland and registered in Fire Protection Engineering. He is a member of the National Fire Protection Association (NFPA), has served on the NFPA Standards Council, and is a member of multiple NFPA technical committees. Other NFPA activities have included participating on the editing of the Sprinkler Handbook and the Fire Protection Handbook. His national activities involve the NFPA Research Foundation, UL Standard Technical Panels, and NICET. Additionally, Roland is a proud United States military veteran.