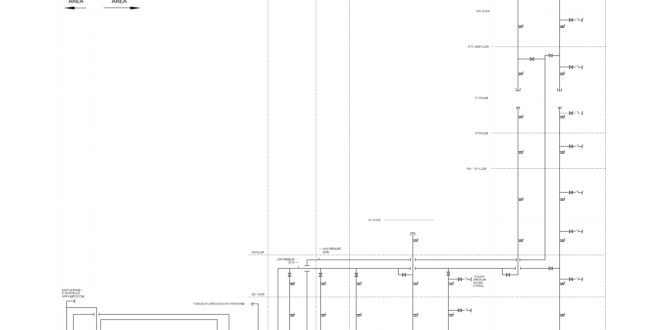
High-Rise Standpipe Design
A Case History
In my previous standpipe article (see the July/August 2016 issue of Sprinkler Age), I discussed the following issues in standpipe system design:
1. When are standpipes required and what are the installation requirements?
2. What type of standpipe system is required?
3. Where are the required hose outlets located?
4. What is the required pressure at the hose outlet(s)?
5. What is the required flow rate of the system?
6. What are the requirements for the Fire Department Connection (FDC)?
7. Which outlets are flowed in a hydraulic calculation?
8. How is the fire department apparatus defined and used in a hydraulic calculation
In this article I will address issues 2-6 and how they were addressed in a high-rise project currently under design. The project is being designed under the requirements of the Virginia Uniform Statewide Building Code (VUSBC) 2012 edition which is an amendment to the 2012 edition of the International Building Code. As referenced in Chapter 35 of the VUSBC, the applicable version of NFPA 14, Standard for the Installation of Standpipe and Hose Systems, is the 2010 edition. All further references will be to the 2010 edition unless noted.
The subject project consists of an addition to an existing high-rise residential building. The existing building (phase 1) is 17 stories with a height of approximately 174 ft. The addition (phase 2) will consist of a 24-story tower with a height of approximately 262 ft. As is common in high-rise building design there is no programmed 13th floor in either tower. The first three stories of the addition consist of expanded parking and amenities levels with an approximate area of 80,000 ft2 per story. The fourth through 22nd floors of the tower consist of residential units and the 23rd and 24th levels are mechanical spaces, each with an approximate area of 15,000 ft2. The first through fourth floors each have six required stairways, the fifth floor has three, and the sixth through 24th floors each have two. The existing main entrance on phase 1 will be maintained and a new “main” entrance for phase 2 will be provided.
What Type of Standpipe System is Required? As discussed in my previous article, because a high-rise building is required to be provided with automatic sprinkler protection, a Class I standpipe system is permitted. NFPA 14 section 5.4.1.2 requires that the standpipe system in high-rise buildings to be automatic or semi-automatic. So, to meet NFPA and VUSBC requirements a Class I automatic standpipe system was designed for the building.
Where are the Required Hose Outlets Located? For Class I standpipe systems, section 905.4.1 of the VUSBC requires an outlet at the intermediate floor level landing between floors in all “required” exit stairways. Under the provisions of the building code, an exit stairway that is designed as an egress path and is provided with signage designating it as an exit is a “required” exit regardless if it is required or not due to travel distance limitations. As permitted by the same section of the VUSBC, the fire code official is permitted to allow the outlets to be located at the main landings in lieu of the intermediate landings. During design meetings with the fire marshal to review building plans and fire protection requirements, the design team was directed to locate the outlets at the main stairway landings. One of the tower exit stairways extends to the roof and the standpipe in that stairway extends to the highest landing to provide a hose outlet on the landing. This outlet satisfies the requirement in section 905.4.5 of the VUSBC for a single outlet that serves the roof.
What is the Required Flow Rate of the System? My previous article detailed the methodology for determining the required flow rate of the standpipe system. Basically, NFPA 14 requires that the hydraulically remote standpipe flow a minimum of 250 gpm at the highest outlet and an additional 250 gpm from the next highest outlet. Each additional standpipe is required to flow 250 gpm to a maximum of 1,000 gpm for buildings protected with an automatic sprinkler system. For the sixth through 24th floors a total flow rate of 750 gpm was required due to the two standpipes, one in each exit stairway. As can be seen on the system riser diagram in Figure 1, the first through fourth floors are provided with six exit stairways and the fifth floor is provided with three exit stairways, with each stairway containing a standpipe. Therefore, these floors have a required flow rate of 1,000 gpm.
What is the Required Pressure at the Hose Outlet(s)? The VUSBC section requires a minimum residual design pressure of 100 psi at the most remote 21/2-in. outlet on a Class I system. Based on the floor plan of the building, this would require that the remote outlet on the 24th floor main stairway landing maintain a residual pressure of 100 psi. To attain this pressure at the required flow rate would result in a residual pressure of approximately 210 psi on the first level based on elevation head alone. This pressure is above the 175 psi working pressure of the standard components of a standpipe or sprinkler system. To account for the required residual pressure at the 24th floor while maintaining a pressure below 175 psi on the lower floors a two-zone (low pressure and high pressure) system utilizing a single fire pump was designed for the building. This system is a modification to the one detailed in NFPA 14 figure A.7.1.(b).
Starting with the design parameter that a maximum working pressure of 175 psi was permitted on the system components a calculation was completed to determine how high (which floor) could be supplied from the low-pressure system starting with 175 psi at the first floor (ground level). Using an elevation loss of 0.434 psi/ft and approximately 30 psi friction loss through the system it was determined that the low-pressure system could supply the required 100 psi residual pressure to the first through 11th floors. The high-pressure system was then designed to supply the 12th through 24th floors.
The final fire pump rating of 750 gpm at 215 psi was based on meeting the standpipe system pressure demand of 100 psi at the hose outlet on the 24th floor while also meeting the flow requirement of 1,000 gpm for the lower five floors. To supply this demand while not over pressurizing the low-pressure zone, a pressure-regulating valve assembly was designed into the building standpipe supply and located in the building fire pump room after the fire pump assembly and prior to the fire department connections. The assembly followed the extensive requirements of NFPA 14 section 7.2.4 and figure A.7.2.4. The fire pump test header is located on the exterior wall of the fire pump room. The header is provided with four 2½-in. outlets in lieu of the three that are required under NFPA 20, Standard for the Installation of Stationary Pumps for Fire Protection, for a pump rated at 750 gpm as it also serves as the backflow preventer test header.
The option of designing the system by locating a pressure regulating device at each sprinkler system floor control valve assembly and standpipe connection on the lower pressure system in lieu of one assembly in the fire pump room was discussed during the project design stage but was not selected as multiple pressure regulating devices within the building was considered to be a maintenance and testing burden by the owner.
What are the Requirements for the Fire Department Connection? With the building now having two “main entrances” and separate but connected towers with independent standpipe systems, the fire marshal was concerned that responding apparatus may stage at the “wrong” entrance. To address this issue, each tower was designed with two separate fire department connections that would supply each tower. Signage at each of the connections will direct the fire department as to which tower standpipe system that FDC serves. Each new FDC that serves the new tower is provided with four inlets per the requirements of NFPA 14 section 7.12.3 of one inlet for each 250 gpm of design flow.
ABOUT THE AUTHOR: Rick Alpert is a senior fire protection engineer with Clark Nexsen, Inc., an architectural and engineering firm, in its Virginia Beach, Virginia office. He has over 35 years of experience in the design, construction management, and commissioning of public, private and commercial projects including projects for high-rise residential and office buildings. In addition to his engineering career Alpert has been involved with the volunteer fire service for over 43 years and has served in many leadership positions within local fire departments including those of vice president and chief. He holds several national certifications including ICC Building Plans Reviewer and Pro Board Fire Officer II.
IMPORTANT NOTICE: The article and its content is not a Formal Interpretation issued pursuant to NFPA Regulations. Any opinion expressed is the personal opinion of the author and presenter and does not necessarily present the official position of the NFPA and its Technical Committee.