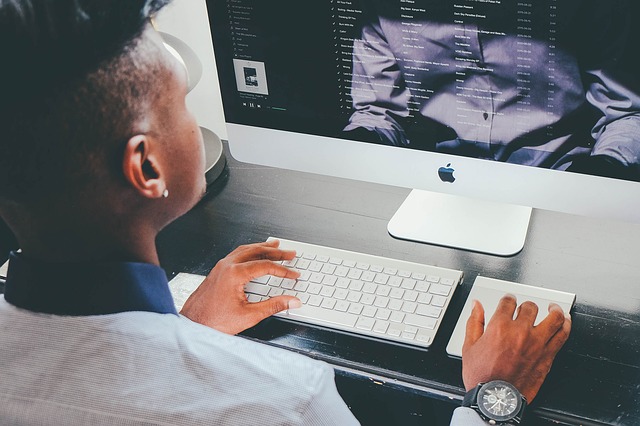
Getting the Design Basis Right
Understanding the Modifiers
There comes a time when many ask, “What does NFPA 13, Standard for the Installation of Sprinkler Systems, mean by that?” This is especially prevalent with some of the modifiers that affect the commodity classification, the single most important aspect of the design. This came to my attention again recently when asked about changing wood crates to plastic ones for storing fresh fruit. The storage arrangement was solid pile, nonexpanded, exposed Group A plastic at 20 ft of storage with a 32-ft ceiling. The density for a stable pile is 1.1 gpm/ft2. If the pile was considered unstable, it would be a density of only 0.6 gpm/ft2. Such a difference has a rather significant impact on the cost, especially if driven to an on-site tank with a fire pump. Getting it wrong, though, has a big liability hanging over one’s head for the life of your company. There’s also the issue of being able to explain why the modifier applies to the Authority Having Jurisdiction (AHJ) if questioned during the plan review.
In reality, there are two basic groups of modifiers: those that change the commodity classification and those that impact the design basis. From a fire dynamics perspective, the commodity classification is the amount of heat that is released due to the material itself as well as the form it takes (surface area to mass ratio). The variables impacting the design basis (density or size of remote area) otherwise assigned to a specific commodity classification are mostly about how the setting affects the amount of heat released. To keep it from being too simple, variables like surface area fall into both camps. The difference, though, will be apparent.
In the broad sense of things, we have eight commodity classifications made up of Class I-IV commodities and the family of Group A plastics (subdivided into four groups). These sub-categories are: expanded, nonexpanded, cartoned, and exposed. One could argue that cartoned is more a setting/environment factor instead of being a material characteristic. Keep in mind, though, that we look at pallet loads in a cumulative or overall perspective. From a pure heat release perspective, the minimal amount of paper presented by the carton is irrelevant. It’s the location of the paper and its impact of increasing the time required for the plastic in the adjacent packages to start burning that creates the difference. Nonetheless, with it being such a common aspect of an entire pallet load, it’s not a modifier but a material aspect of the commodity.
To ensure this is still a little confusing, there is a modifier for cartons that changes the commodity classification – cartons that have multiple layers of corrugated cardboard. See the note in the decision tree in Chapters 15 and 17. On a very literal sense, if you take a cross sectional view, there is a layer of paper, a layer of folds or alternate furrows and ridges (the definition of corrugated), a layer of paper, a layer of corrugation, and a final layer of paper sandwiching the corrugation. (See Figure 1 on page 19.) This was pretty common in the past where products were heavier and the cartons needed more strength and more likely it was there to provide a degree of protection against impact damage. Now with Styrofoam protecting the components in the carton, this feature is not very common. I’ve seen cardboard walls a 1/2-inch thick. I’ve also seen a very lightweight double corrugation no more than 1/8 in. Unfortunately, this variable is not quantified (like we do for defining combustible paper on insulation in Section 8.15.1.2.12 being limited to 1,000 BTU/ft2). It has to be thick enough to significantly delay the growth of the fire. When it is, a product that is otherwise a cartoned, Group A plastic becomes a Class IV commodity. This reduction also applies to cartons where – “the amount and arrangement of Group A plastics within an ordinary carton would not be expected to significantly increase the fire hazard.” This doesn’t mean a standard compartmented carton (where there are single ply cardboard dividers separating the items in the carton). Such a compartmented carton is the standard test assembly used for cartoned nonexpanded Group A plastics. This one is even harder to determine if applicable. At least with the multiple layers of corrugation one need only be a little conservative on the overall thickness, but this one leaves nothing to hang your hat on. There is one point that should be emphasized regarding this allowance. Both the allowances appear in one note that says – “under the following conditions.” This leaves it a little murky as to whether they are separate allowances or that both must occur together. Fortunately, note (2) says within an “ordinary” carton meaning a single layer of corrugation. Since a carton can’t be both, we have our answer.
Moving to the product itself, we have solid unit load. This one applies only to Group A, nonexpanded plastics. It’s effectively solid blocks of plastic whereby the fire burns just on the exterior (and burns slower due to a lower surface area to weight ratio). It only applies to solid pile storage. It is not an aspect of the pile, but of the pallet load within a pile. It allows a very large reduction in density.
The next modifier that can affect the commodity classification is the well-known plastic pallet. With this being so well known (and well addressed by NFPA 13), there are only a couple of aspects I want to touch. One is that for ceiling-only protection, plastic pallets are ignored when using spray sprinklers with a minimum K-factor of 16.8. Another is that, although we don’t use the term “stability,” a modifier to be discussed shortly, an unreinforced plastic pallet presents an unstable load thus requiring a smaller increase. A final point is that even though the plastic constitutes a fairly small percentage of the overall pallet, its exterior location combined with the optimum burning configuration presented by a pallet, causes a big impact on the classification. When applying the unreinforced classification, consideration should be given to whether or not the client will know if there is a future change to reinforced pallets.
Location of the material is an item that doesn’t get a lot of attention but, as indicated by the plastic pallet, can greatly impact the commodity classification. The challenging part is that this characteristic conflicts with the allowance for some Group A plastics in the definitions for Class III and IV commodities. You can have a block of steel incased in Styrofoam that meets the definition of a Class IV commodity (contains Group A plastic that is no more than 15 percent by weight and 25 percent by volume), but it will burn like an exposed, expanded Group A plastic. This is explicitly addressed when it comes to plastic crates as shown in the examples in Table A.5.6.4.1 for milk containers in a plastic crate being assigned as a nonexpanded, Group A plastic but is easy to overlook in when evaluating general products.
A final modifier impacting the commodity classification is chemical additives. We are used to embracing fire retardants as a modifier such as when used to omit sprinklers in combustible concealed spaces. Its acceptance is more elusive, though, when addressing material characteristics, since these compounds are generally more a matter of reducing the potential for ignition without reducing the heat released once it’s burning. That’s one reason why A.5.6.4 says that fire retardants should not be relied upon as a sole basis in the reduction of classifications.
Let’s now look at modifiers that impact the design basis that aren’t functions of the material itself. Although we don’t think of it as such, the category of storage arrangement is a modifier. Rack storage presents a more demanding fire than solid pile since there is more exposed surface area. The aspect of surface area though is not simply based on what you can see, but what can readily burn. As such, it is what you can see that can get an adequate supply of air. Racks allow a lot more air flow to surface areas (while still having the material close together in an optimum vertical orientation thus increasing the rate of fire growth as shown by fires flying up the flue space) than solid piles. This is indicated by Section 15.2.2.6 that allows Chapter 17 criteria to be applied in place of Chapter 15 criteria. This is a little surprising because it allows a remote area of only 2,000 ft2 instead of the standard 2,500 ft2 required by Chapter 15. It should be noted that there isn’t a similar allowance between Chapters 14 and 16 on Class I-IV commodities. This was discussed at the technical meetings for the 2016 edition and I thought it was being added but that didn’t happen (at least not yet). A more subtle air flow factor is between double row racks and multiple row racks. With aisles next to all the pallets, the double row racks are more challenging. That’s why we have to provide additional protection for double row racks with solid shelving but you can have the same amount of obstructed rack area between the transverse flues in a multiple rack, and it’s considered an open rack. On the other hand, through not burning as vigorously, less water is reaching the fire so this variable increases the requirement for in-rack sprinklers. Within the solid pile arrangement, the impact of air flow is a less significant factor as indicated by it impacting only the criteria for Group A plastic. It is addressed by the pile being either an open or closed array as defined by the presence of vertical flues (greater than 6 in. is classified as open). A closed array allows a slight reduction in the size of the remote area (2,500 ft2 to 2,000 ft2), making it more a concern regarding flame spread versus increased fire hazard.
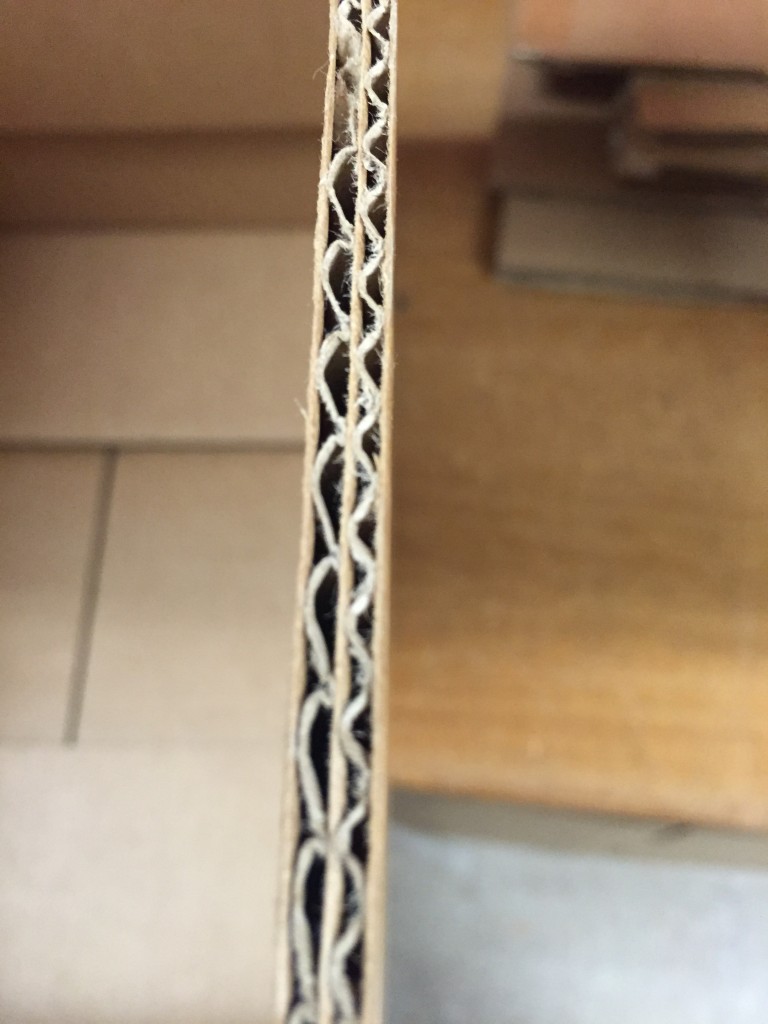
Let’s now move to the well-known issue of encapsulation. Per its definition, it’s a pallet load of combustible products that are enclosed in plastic. A critical aspect is that the top of the load must also be covered. Otherwise, it’s just a wrapped pallet. As would be expected, it includes a pallet full of products that are individually wrapped in plastic. When applicable, the density takes a big jump. For 20 ft of solid pile, Class I with high-temperature sprinklers, the density is 0.153 gpm/ft2 whereas when encapsulated it’s 0.46 gpm/ft2. For 20 ft of Class I in racks (8-ft aisle, high temperature sprinklers, and no in-rack sprinklers) in double row racks it is 0.29 gpm/ft2 versus 0.47 gpm/ft2 respectively. In multiple row racks, it’s 0.37 gpm/ft2 versus 0.463 gpm/ft2. It’s interesting that each storage arrangement follows a different approach for increasing the density. Solid pile uses a curve without encapsulation, but a single point without a difference for height or sprinkler temperature rating. Single and double row racks use two different curves. Multiple row racks uses a single curve with a 25 percent increase for encapsulation of Class I-III and 50 percent for Class IV. This big jump in density implies that the hazard is greatly increased. To be candid, that is not the case. The Sprinkler Handbook talks about how much more difficult it is when the product is encapsulated. That’s a valid statement. It also says that it presents too difficult of a fire to go beyond 20 ft. That’s a less-than-valid statement. The reality is that the tests were conducted back when only K-5.6 and K-8.0 sprinklers were available. It isn’t that encapsulation presents a hazard that we are barely able to control with today’s sprinklers, but that the older smaller K-factors could barely control it. Today, we knock down the fire whereas before with higher challenges, the sprinklers were either chasing the fire or just keeping it from getting any bigger and simply burning itself out. An example of this difference is the already identified allowance to ignore plastic pallets when using a K-16.8 or greater spray sprinkler. For those interested in more information on the degree of improvement, see “Evolution for the Protection of Storage” in the February 2010 issue of Sprinkler Age. Although the standard requires the use of a K-11.2 or greater when the density is 0.34 gpm/ft2 or greater, there’s never been a reevaluation of the limits imposed on encapsulation.
Pile stability impacts only solid pile Group A plastic. As identified by its definition, an unstable pile will collapse, have spillage of contents, or lean across the flue spaces early in the fire. In effect, it cuts off the flues slowing the growth in that portion of the pile and pushes the fire to predominately the pile exterior, reducing the exposed surface area. Although this sounds much like a closed array, stability allows a greater reduction in the required volume of water. This modifier is not just about blocking the flues, but also incorporates the high likelihood of generating some reduction in the height of storage. This is a difficult characteristic to evaluate. It is certainly easier when the load is not cartoned and plastic wrapped. It still requires that the product provides marginal structural capability without the wrap. If you have thick plastic cartons, they are typically viewed as not losing their stability early in the fire. This doesn’t mean that this characteristic applies only to pallets that can’t remain standing without their plastic wrapping. It can be applied to cartoned products, though it isn’t a given. We gather this guidance from the definition of compartmented (for cartons) that states it presents a stable unit under fire conditions. This is also repeated in the annex under pile stability. It also states that when not compartmented, cartons tend to be unstable. This doesn’t mean that all cartoned piles jump to unstable. It depends on the contents of the carton, along with the overall weight and height of the pile. If the interior arrangement of the product is capable of carrying the load, the loss of the exterior portion of cardboard is not going to cause collapse or leaning. If the load is basically carried by the carton, but you only have three pallets of a very light product, it’s likely to remain stable. If it is heavy enough that the cartons are already showing signs of buckling, it’s an easy call. The taller it gets (ignoring the obvious increase in carried weight), the less deflection it takes for the pile to lean. A final aspect is that this event must occur early in the fire. Though early in the fire is not quantified, the Sprinkler Handbook tells us it is in the first minute or two after activation of the first sprinkler. I’m not sure if enough data can be gleamed from fire modeling, but the American Fire Sprinkler Association (AFSA) will be doing a study to see if this characteristic can be better quantified.
The last modifier to be addressed is free flowing. It is another item that impacts only Group A plastics but applies to both solid pile and rack storage. The definition provides a really good starting point by stating that it consists of small products that will fall out of their container during the fire. It even provides examples such as flakes, pellets, and small objects like razor blade dispensers or up to 2-oz bottles. Unfortunately, the remainder of the definition contributes to confusing the issue by stating that it will fill the flue space, creating a smothering effect. This implies that there must be a massive amount of material flowing into the flue, along with the assumption that it must occur early in the fire (as actually stated for unstable piles). Otherwise, how can this reduce the fire hazard? This leads to very restrictive interpretations such as thinking it must be very large containers that open quickly when exposed to fire (aka big plastic bags). If you start with the question, “How can small bottles flow out fast enough to fill the flue?,” it opens the door to the rest of the story. As the exterior of the container fails, if most of the contents spill out, that will put the Group A plastics down on the floor (or slowly filling the flue). The fire up in the rack or pile (where the conditions to burn vigorously are far more optimal than a pile on the floor) has both less available fuel and less demanding fuel. Thus, it is treated as a Class IV commodity instead of a Group A plastic. This tells us several things. One is that it doesn’t have to be big containers. Two, it can apply to non-compartmented cartons. Three, it was not an oversight that it does not say “must occur early in the fire.” It’s also worth pointing out that this modifier applies to both nonexpanded and expanded plastic including exposed expanded. This did not become clear until the 2016 edition. In prior editions, there was a difference between Chapter 15 and Chapter 17 whereby rack storage located this issue further down the decision tree (after the decision was made on exposed expanded). Now Chapter 17 correlates with Chapter 15 where it’s addressed, immediately after the Group A plastic decision.
The modifiers that affect the assigned commodity classification or design basis have been around for quite a while. Considering how critical this part of the design is, we’re fortunate that most of them are pretty straightforward. For those that are ambiguous, if more clarity cannot be provided by the technical committee, there will be a discussion on deleting them (much like what previously occurred with the 11/2-ft to 3-ft clearance modifier).
Roland Huggins, P.E. is the vice president of engineering and technical services for AFSA. He is a graduate of the University of Maryland and a member of the NFPA. Huggins has served on the NFPA Standards Council and is a member of multiple NFPA technical committees, including NFPA 13, NFPA 25, and NFPA 5000 (Building Code). NFPA activities include participating on the editing of the Sprinkler Handbook and Fire Protection Handbook. Other national activities involve the NFPA Research Foundation, UL Standard Technical Panels, and NICET. Huggins is a veteran.
IMPORTANT NOTICE: This article and its content are not a Formal Interpretation issued pursuant to NFPA Regulations. Any opinion expressed is the personal opinion of the author and presenter and does not necessarily present the official position of the NFPA and its Technical Committee.