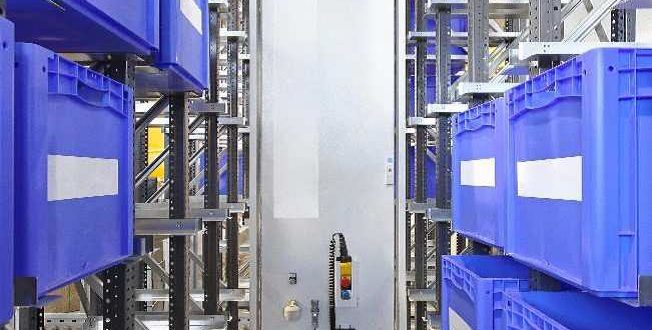
Fire Sprinkler Protection for Automated Rack Assemblies
Are You Ready For This Latest Challenge in Fire Protection?
The methods of warehousing of various products and how to protect them from fire has always been a challenge for the fire sprinkler industry. Automated warehouses are the latest challenge in fire protection, and in many ways automation technology is outpacing fire protection technology. This article will attempt to explain some of the new challenges the fire sprinkler industry faces with the continued advancement of automation in warehouses with a specific emphasis on automated storage and retrieval systems (ASRS). ASRS are used for many different storage arrangements and retrieval methods and the fire sprinkler industry should become familiar with terms like mobile racks, stacker cranes, trilateral stacker cranes, miniload systems, pallet shuttles, pallet conveyor systems, box conveyor systems, and of course autonomous mobile robots. Most of the giants in the manufacturing and distribution world are leading this technology including Walmart, Coca-Cola, Netflix, Amazon, FedEx, Nike, Ikea, and UPS to name a few.
Automation is taking warehousing to new heights and creating tightly packed storage arrangements. There is no doubt that the future state of warehousing and distribution will continue to include more and more automation and higher and higher automated racks and retrieval systems. There are many advantages to automation. Fewer people in the warehouse removes the human elements of fatigue and other factors that lead to reduced productivity and human error. Automation reduces the need for the same levels of climate controls and lighting that are needed for occupied warehouses. Automation also reduces some of the risk factors historically tied to fire sprinkler systems. Sprinklers and piping are less susceptible to damage by fork lifts or pallet loads since the retrieval systems operate within very close tolerances. However, total automation may bring in other factors that affect fire sprinkler systems such as freezing conditions because the warehouse may no longer have to be heated. (See Figure 1.)
Complete fire protection for an automated warehouse involves many components. It begins with the building site and the infrastructure including access for fire emergency vehicles, and electrical and water supplies. It includes passive fire protection features in the construction of the building itself, the protection of the structural elements, and draft curtains where required. Active fire protection features can include heat and smoke vents, fire detection and notification systems, shunt trips for automation shutdown, and of course automatic fire sprinkler systems.
Emergency response procedures must be considered. One discussion in a recent International Code Council (ICC) Fire Code Action Committee conference call centered on what should happen in a fire event in a tall rack building if the ASRS is the only means to access the rack loads. Will firefighters have to climb into the racks to reach a deep-seated fire in a pallet load? Should the ASRS remain in operation in case it is needed for firefighting and access to the burning commodity? If the ASRS remains in operation, is there an electrical hazard exposure for the firefighters? The 2018 edition of the International Fire Code (IFC) requires a “manually activated emergency shutdown switch for use by emergency personnel,” which puts the decision on the first responders, who may or may not have sufficient information to make the decision to shut down the automated system or not. A proposal for the 2021 edition of the IFC adds new text requiring an approved automatic shutdown process when the fire detection system senses a fire or when water flow is detected, plus a switch to manually initiate shutdown. By requiring an approved process, the local fire officials must be included in the conversation and must agree with the shutdown process. Hopefully this proposal will be accepted into the 2021 edition of the IFC.
While consideration for the first responders is not usually on the minds of fire sprinkler contractors it emphasizes the need not only for fire control but for fire extinguishment when possible from the sprinkler system. Fire control requires follow-up from first responders to manually attack the fire where it is being contained. Fire extinguishment only requires removal of the damaged goods and general cleanup after the fire event is over.
Sprinkler protection needs to be customized to the automated warehouse. Fire protection is a vital and desired component of the overall building operation. A properly designed, installed, and maintained fire sprinkler system is arguably the most important part of the fire protection plan. There are numerous variables and combinations that determine the sprinkler system design criteria, and most of those are addressed in NFPA 13, Standard for the Installation of Sprinkler Systems, 2016 edition. Chapters 12 through 21 include the general and specific requirements to protect the most common storage arrangements. To begin establishing the design criteria for an automated warehouse there are numerous factors that must first be determined. Some of those factors include:
- The commodities being stored and the packaging of the commodities. Is it cartooned and if so is it compartmented?
- The percentage of expanded and unexpanded plastics in the commodity and the packaging.
- The ceiling height at the eaves and at the peak and the maximum storage height.
- The clearance height from the top of storage to the ceiling.
- The method of storage. Is it solid pile, on pallets, in crates, in boxes, in bins, on shelves? Are the pallets wood or plastic? Are the pallet loads encapsulated or not?
- The type of rack as defined by NFPA 13 (single-row, double-row, or multi-row). What are the aisle widths? Are there open-topped containers? Are there horizontal barriers?
Once the storage arrangement and all of the various factors that affect the design criteria have been determined, the decision can be made if sprinkler protection can be achieved using the requirements of NFPA 13. Following the requirements in NFPA 13 is not easy, but at least it is possible to establish the proper protection scheme. Unfortunately, ASRS have not been specifically addressed in NFPA 13 and many automated warehouses store their materials in ways that exceed the limitations of NFPA 13 criteria. The use of open-topped containers, the height of the racks, the construction of the racks, narrow aisle widths, and the limited clearances within the racks (horizontally for flues or vertically for distance between in-rack sprinklers and the top of the load) are some of the factors that exclude the use of NFPA 13 for the design criteria. Also, NFPA 13 does not address what needs to happen to the automation when a fire is detected or when sprinklers activate. Should the ASRS shut down is the potential for fire spread also eliminated? When NFPA 13 cannot be used, where do the design professional and the sprinkler contractor go for the proper protection scheme?
There are a couple of avenues to take when trying to provide sprinkler protection for storage configurations not covered by the current edition of NFPA 13. Keep in mind that the “latest technology” available in NFPA 13 is at least two years old when the newest standard is published. Updating the standard takes three years from start to finish, and any new protection schemes must be submitted during the first draft which is toward the beginning of the revision cycle. For example, the 2019 edition of NFPA 13 will be presented and acted on by the NFPA membership at its June 2018 Technical Meeting and then issued by the NFPA Standards Council in August 2018. Changes for the 2019 edition had to be submitted to the NFPA by June of 2016, over two years prior. Sprinkler manufacturers are submitting new sprinklers for testing to Underwriters Laboratories and FM Global on a regular basis that successfully protect commodities and hazards not currently covered by NFPA 13. The New Technology section in Chapter 1 would allow for the use of those new protection schemes. Sprinkler manufacturers will gladly help determine if one of their listed sprinklers will protect the storage configuration in question.
Another avenue to consider is the new guidelines published by FM Global in their Loss Prevention Data Sheet 8-34 “Protection for Automatic Storage and Retrieval Systems (ASRS).” This data sheet is the result of a recently concluded series of full-scale fire tests by FM Global to determine how to protect these challenging storage arrangements. Within this data sheet is guidance for the construction of the racking system, the weight considerations based on sprinklers discharging, the width of transverse flue spaces, provisions for interior hose stations, and the automatic shutdown of the ASRS when smoke or heat detectors activate.
The basic concept of sprinkler protection in Data Sheet 8-34 is to keep fire growth to a minimum by surrounding the commodity in the rack with closely spaced sprinklers that will not allow the fire to spread horizontally or vertically. 160°F nominally rated quick response in-rack sprinklers with a minimum K11.2 are strategically placed in the flues, between loads, along the face, and at maximum distances vertically. In-rack sprinklers are provided at or just below the horizontal rack member above the load at each tier level where sprinklers are required. The spacing of sprinklers in the racks and the number of sprinklers calculated in the remote area are based on the depth of the row of storage, the material used for the tray or container, the container type, the vertical distance between in-rack sprinklers, and the height of the tier levels. The number of in-rack sprinklers in the remote area calculations can range from 4 to 12 depending on these factors and the minimum flow from each remote in-rack sprinkler can range from 30 gpm to 120 gpm. The overall in-rack sprinkler demand can be as low as 120 gpm to as high as 1,440 gpm plus a hose demand of 250 gpm. Overhead sprinklers are required to protect the top tiers of storage in the racks, but the water demand is separate for the ceiling sprinklers meaning that it does not have to be balanced or combined with the in-rack sprinkler system.
While the protection criteria in Data Sheet 8-34 may require a significant number of in-rack sprinklers at each level where in-rack sprinklers are required, there are advantages that offset that cost by not needing horizontal barriers in the racks, not needing additional overhead steel or column steel protection, reducing the overall water flow requirements as well as suppressing the fire as opposed to simply controlling it.
More and more warehouses being built will be equipped with automated storage and retrieval systems. Many will be built with ceiling and storage heights that cannot be protected with ceiling sprinklers alone. In-rack sprinklers will have to be installed. Contractors need to be aware of the limitations of current fire protection technology, as well as the most recent advances in sprinkler protection for rack structures. It pays to know your options.
The following are some basic best practices to consider when estimating and executing a contract to design and install a fire sprinkler system in these facilities.
Plan how to do the installation before you submit your proposal. One warehouse built in Switzerland is 144-ft high. There is a YouTube video that takes you through the entire construction sequence of the warehouse. Single-row rack modules five-tiers high and six-loads wide were hoisted into place using cranes. The racks were assembled to full height at one end of the building and then construction progressed to the other end. While watching this operation I was not sure if there were sprinklers in the racks as these modules were being hoisted into place or not. As the installing contractor you need to ask yourself which would be the most efficient method of installation. Is it installing the majority of the sprinkler pipes and sprinklers in the rack modules before they’re hoisted in place which will require additional protection of the sprinklers, or installing them after the racks are in place? Installation labor is typically the highest costing line item in the estimate.
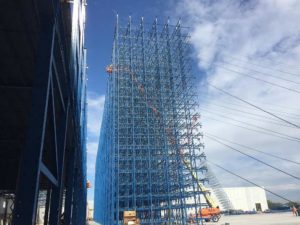
Protect your estimate and your proposal. Team up with the insurance carrier and the local Authority Having Jurisdiction (AHJ). Make sure everyone is in agreement with the protection scheme and get all parties to provide their approval in writing if possible. Getting all parties to sign off on the design criteria is preferred, but a reverse letter detailing the agreements is usually acceptable. Consult with your attorney to make sure. Qualify your proposal to protect your estimate. Specify your installation method and any dependencies you have on the general contractor. Specify the construction schedule as you know it and how your installation fits into the schedule. (See Figure 2.)
Design the sprinkler and piping layout with the installation plan in mind. If branch line piping will be installed in rack modules before they’re lifted in place, the design must allow for piping configurations that fit into the rack modules with the necessary hangers and supports to keep it in place as they’re being hoisted. The design should include protection of the sprinklers and the most efficient method of connecting the branch lines from one rack module to the next. Will a single coupling at the intersection be sufficient or will there need to be a small spool piece? If the branch line piping is being installed after the racks are erected, then the branch line pieces must be designed to be handled and installed within the racks. Shorter pieces may be needed unless full lengths can be fed in from the ends of the racks.
The layout, stock list, and fabrication must be precise. In this age of CAD drawings generated by computer programs, addition errors are eliminated, and pipe cuts can be made as accurate as needed. The placement of sprinklers within the racks is critical with very little room for error. Tolerances are within fractions of an inch in some cases because of the movement of loads and containers within the racks. The contractor should select the piping method that can best be installed within those tolerances.
In conclusion, the fire sprinkler industry faces new challenges every day. We know our industry and our products offer the best solution for life safety and the protection of buildings and contents from fire. However, we are constantly facing new construction practices, new materials, and new hazards. Sprinkler manufacturers with the help of Underwriters Laboratories and FM Global are testing new sprinklers and new applications for sprinklers to meet the needs of our industry and the entire fire protection community. Contractors need to follow suit, embrace the changes and challenges, and be knowledgeable of the latest technologies and advances available to our industry.
ABOUT THE AUTHOR: Terry Victor, senior manager of industry relations at JCI/Grinnell Fire Protection Solutions has over 44 years of technical experience in the sprinkler industry. He is NICET certified Level IV in water-based systems layout and special hazards systems layout. Victor serves on various industry boards and committees, is a member of the CFSI National Advisory Committee and the AFAA Codes and Standards Committee. He is the JCI regional coordinator for codes and standards in the U.S., is the current chairman of the Capital Region Fire Sprinkler Association, and is a member of numerous NFPA technical committees including those for NFPA 3, 4, 13, 13D, 13R, 14, 15, 16, 20, 25, 72, 101, 214, 303, 5000, and the Correlating Committee on Building Codes. Victor received the NFPA Committee Service Award in 2015.
IMPORTANT NOTICE: This article and its content are not a Formal Interpretation issued pursuant to NFPA Regulations. Any opinion expressed is the personal opinion of the author and presenter and does not necessarily present the official position of the NFPA and its Technical Committee.