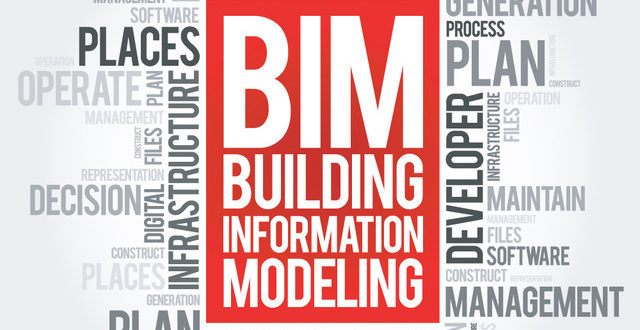
BIM and the Fire Sprinkler Industry
A Sprinkler Contractor’s Perspective
BIM (building information modeling) and 3D coordination. Is it the creative tool that proponents would work to convince you of or is it the albatross weighing down the design departments of most fire sprinkler contractors today? There is no doubt that BIM design and 3D coordination, when managed correctly, can have a positive impact on the installation of our work. But how are we able to manage correctly when others outside our company are actually driving the design process? Are we simply along for the ride? Are we able to accurately account for BIM design in our project estimates? Do we accept design budgets that are disastrous, causing projects to lose money? How many times have you heard, “This project has been BIM coordinated, so we should be able to pick up all kinds of time in the field.” How has it worked for you?
We are all aware that as contractors, we need to be competitive and perform successfully to stay in business. It is a simple, yet complicated, concept. The idea to establish a reputation for our companies of being competitive, efficient, and profitable is everyone’s goal. Some owners and general contractors we work for do value the end result of a successful project and take those relationships to the next project. However, many times those relationships simply mean your company has made the bid list for that next project. You may get preferred treatment in the bid process, but the job is going to be awarded to the lowest bidder. At the end of the day, when a project is awarded, the low bidder has given out pricing to do a job and now is tasked with the responsibility of completing it within budget.
We have all been told that BIM is an effective technique for conceiving, planning, and designing structures of any size and complexity. BIM allows the design team to visualize all the building components and systems before construction ever starts. With MEP clash detection, BIM allows the designers to see potential problem areas and work through fixes. Ideally, this process addresses problems in design, so that they don’t have to be taken care of in the field.
How do we account for, or attempt to account for, the impact of BIM in the design and installation of our projects? Fire sprinkler contractors today face the challenge of having to design projects and participate in the BIM process, all while trying to maintain overall project budgets and schedules. The process of designing fire sprinkler systems has changed dramatically over the last several years. Today, there are several available software programs which provide design options compatible with AutoCAD and allow for BIM. The high cost of design software, whatever your flavor may be, is a cost that we have all come to accept. The additional software required for design and participation in the BIM process (Navis and/or Revit) are costly additions. Then the cost to train and educate our fire sprinklers designers is something that we deal with as well. The costs for learning new software and the time required for training are hard to measure. Rarely does the construction world stop so we can adjust or catch up. We all deal with the impact that training has on our overall workload. Typically, we find training interlaced with meeting the project demands of our workload.
But who really understands and bears the costly burden of this process? Is it the building owner? Is it the installing contractor? Are all building owners willing to spend the time and money required to complete the process?
Fire sprinkler contractors have a huge disadvantage over other mechanical subcontractors. Plumbing, electrical, and HVAC contractors all come to the BIM table with their systems engineered, submitted and, many times, approved. The fire sprinkler designer typically starts with nothing and must produce design drawings while going down two roads around the same mountain.
First, we are required to provide preliminary main, line, and sprinkler head layouts so that the coordination process can begin. Many times, the structural engineer needs to address weight loads for hanging and bracing which can impact the routing of the piping system. As the design process moves forward, the designer must attempt to coordinate the piping system, mains, branch lines, and drops. Then we must address coordination of hangers, splay wiring, and earthquake bracing. Typically, there is limited space left for the sprinkler contractor and little consideration given to the fact that NFPA codes or insurance requirements dictate certain design requirements. The person and trade facilitating the BIM-coordination effort play a huge role in how much time the process will take. So, while the designer designs to miss conflict, they must also deal with the clashes that occur with other trades. We all know this can become a very tedious process. All this preliminary yet coordinated design happens before the plan review process begins which now leads the design down a totally different road.
Now the discussion shifts to road number two or the path never traveled by the other trades. While the BIM process is happening, the designer must also be producing drawings which will be used for submittal purposes to the Authority Having Jurisdiction (AHJ) or other reviewing agencies. When do we stop the coordination and allow the review process to start? Having approvals and permit acquisition to do the work is obviously a big deal. Dealing with the reality of meeting the overall project construction schedule and working the design schedule so that, ultimately, we meet the critical dates, is the objective. Many projects that require BIM coordination are going to encounter a lengthy review process to obtain approvals. If construction is progressing, not having approvals could affect the ability to set hangers, sleeves, or even weld inspections for the piping systems. We always find ourselves coordinating, dealing with design and plan check comments, and making revisions and resubmittals while updating the BIM model. Many fire sprinkler contractors find there may need to be a second designer or additional staff members assigned to the project to maintain the pace. Getting the project designed and attending BIM coordination meetings can then become a real challenge. There are some who want to do these meetings with all trades in the same office. That process seems to reflect the days when everyone sat around that table doing their overlays. We have found the most efficient way to participate in these meeting is to do so online and phone in. This allows the designer to participate in the meetings and yet still be doing something productive while the other trades are addressing their issues.
The transition of planning and design to a better-coordinated field installation is obviously the goal of the BIM process. Being able to translate the overall scope of a project from design to the installing field crew is a key element in BIM-coordinated design. There should be an increased awareness of where the potential problem areas are, creating the ability to plan accordingly. Likewise, we should be able to better recognize areas in a project where we may be able to make better time than originally estimated. We should be able to see increased accuracy with material take off and listing, thus increasing the efficiency of material fabrication for the project. There should be a greater ability to organize and bundle the materials. We should be able to have a better grasp of what extra materials need to be sent to the jobsite. If there are field changes in potential problem areas, having not only extra material but the right extra material can only help to keep the flow of the installation moving. The obvious benefit of having your project better organized in the shop is the ability for the field crews to cut down on the time required to layout and find the materials for the job. Being able to hit the ground running with a fully coordinated project and with materials organized in a much more efficient manner should only translate to labor-cost savings in the field.
In the past few years, the BIM process has started to spill over into the field where foremen are now required to have tablets and need to be educated in the BIM process. If there are issues with the field installation, they must first look at the model, figure out the corrective action, and then document the change. Whatever happened to simply having a set of installation prints on the job? No matter how much BIM coordination there is, things still seem to change when the virtual world meets the real-world application. Are we making things more complicated than they need to be? BIM coordination is and will continue to be an ever-evolving process that must be refined in order to help all trades associated with the coordination effort. This is the only way that BIM coordination can reach its full potential.
I think we could conclude that given all the variables, it is extremely difficult to anticipate the design time and costs that a BIM-coordinated project could require. A project that is going to require BIM-coordinated design may not be for every fire sprinkler contractor. Having the design staff and ability to bring in additional designers if required should be a key consideration before the project is ever bid. Having the ability to properly manage your project and constantly be aware of where your actual project costs are is crucial. Obviously, you cannot go way over the design budget to properly address the BIM requirements and then send the project to the field with the expectations that the installing crew will make everything up.
ABOUT THE AUTHOR: Byron Weisz, SET is co-owner of Cen-Cal Fire Systems, Inc. in Lodi, California and Western Fire Protection, Inc. in Poway, California. He has been involved in the design of fire sprinkler systems for 38 years. He holds a NICET Level III certificate in fire protection engineering technology water-based systems layout. Weisz has trained multiple individuals over the years in fire sprinkler design. The company first started using AutoCAD-based design software in 1991. He involved several of the company’s designers in writing this article.