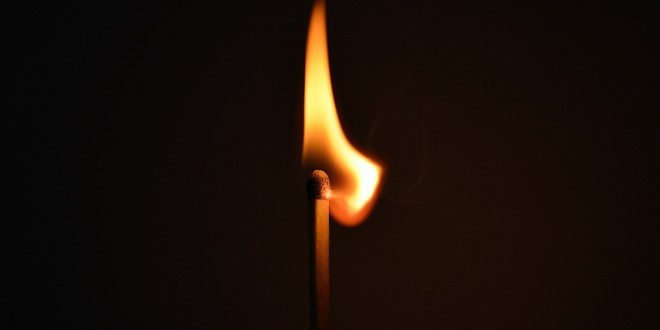
AHJ Perspective: Ratings, Fire Testing and Standards – Part Four
“Rode hard and put away wet.” That was a cliché that I have heard many times when witnessing something that had undergone a severe test and was just about ready to fall apart. The cliché started out describing horses that were put away without proper grooming, but the imagery matches up to almost any exhaustive effort that results in either fatigue or failure.
We might be able to use the cliché in describing the level of testing that is used to make sure that automatic fire sprinklers are capable of operating under the most difficult of circumstances. We install them to be a proactive response to a fire. Therefore, there are considerations to make sure that happens. Of all of the proactive technology we install in buildings, sprinklers are probably the most heavily stressed when they are called upon to perform.
There are sprinklers that have been installed for over 100 years and are very likely to perform just as expected if a fire occurs tomorrow. Sprinklers were designed to be a robust solution for fires from the very start. I find it very interesting that the detractors of automatic fire protection always focus on the possibility of water damage by malfunctioning sprinklers instead of the reality of their reliability. The reliability of fire sprinkler systems is also based on the attention given to periodic testing of installed sprinklers.
It pays to be knowledgeable of how sprinklers are tested at two different stages; the first of these is during manufacture, and the second is after installation.
The first standard you should be familiar with is Underwriters Laboratories’ UL 199, Standard for Automatic Sprinklers for Fire-Protection Service. The scope of this standard covers the requirements for automatic sprinklers intended for installation for commercial or industrial use. This class of sprinklers are those that are installed in accordance with NFPA 13, Standard for the Installation of Sprinkler Systems.
There is a different approval standard for “residential automatic sprinklers” than there is for a commercial sprinkler. UL has an additional standard for residential sprinklers for fire protection service entitled UL 1626. The scope of this document covers residential sprinklers that are used in the installation of sprinkler systems in one- and two-family dwellings and manufactured homes (NFPA 13D) and low-rise residential occupancies up to and including four stories in height (13R). FM Global also produces a document that defines this difference very well.
Just as a reminder, we should note that there are three different sprinkler standards published by the NFPA. We just mentioned them. NFPA 13; NFPA 13D, Standard for the Installation of Sprinkler Systems in One- and Two-Family Dwellings and Manufactured Homes; and NFPA 13R, Standard for the Installation of Sprinkler Systems in Low-Rise Residential Occupancies. Anyone reading this in Sprinkler Age is already familiar with them. (Or, should be.)
The key to understanding how quality control works with sprinkler technology is to take a look at the table of contents of the FM approval standard for residential sprinklers. This document addresses frame strength, heat responsive element, leakage, operating temperatures, strength of the deflector, thermal shock on glass bulbs, corrosion, vibration, rough use and abuse, high temperature exposure, low temperature exposure, process residue and tests that are used to determine the response time of the head under fire conditions.
There is also a special standard for what are called “Early Suppression Fast Response Sprinklers” (ESFR). These are a very special type of sprinkler for a special type of hazard. It is labeled as UL 1767.
The term that is most often used to demonstrate that a sprinkler has been manufactured to any of these standards is the designation of being “listed.” Various testing organizations produce lists of equipment that we can truly say it has been “Rode hard and put away wet.”
The primary purpose of having the standards and test protocols is to reduce the number of defective sprinklers that could fail during an actual fire. Because fire sprinklers play such a vital role in protecting lives and property from the effects of fire, they must always perform in a reliable fashion. Having a third-party’s listing is intended to verify that the sprinkler meets the intent of being performance oriented. So, why do the detractors place so much emphasis on failure? Well, the simplest answer is that failure can occur. Very infrequently. But, it can occur. I don’t want to spend much time on the negative aspects of this, but we must. The reason for many sprinkler failures is the lack of periodic maintenance. And, there is a standard for that, too.
It is entitled NFPA 25, Standard for the Inspection, Testing, and Maintenance of Water-Based Fire Protection Systems. This document is the baseline for the processes that the Authority Having Jurisdiction (AHJ) should be enforcing to make sure that systems remain functional.
So, why do sprinklers get “bad-mouthed” by the detractors? Let’s move on to a real tough topic. It might be because we (the fire service) are not analyzing the failures thoroughly enough. I would recommend that if you are reading this column to be better informed you might want to go to the Internet and type in the words: fire sprinkler failures. One article that should appear in the search is entitled “Lessons Learned from Unsatisfactory Sprinkler Performance.” It is authored by R. Thomas Long, Neil P. Wu, and Andrew F. Blum. It was originally published in Fire Protection Engineering. It is an eye opener that we need to know about.
The part of the article that got my attention was a table that listed the reasons for system failures. At the very top of the list (38 percent) was the fact that the system was turned off. If that is true I have to wonder how many sprinkler systems are out there that are turned off right now. Could we do something about that? I think so. How about an annual inspection of the systems?
Do you want your fire department to be a “case study?” I would think that your use of the testing standards to install the best technology possible, backed up by a documented inspection and maintenance program can go a long way towards keeping your agency off the front page of the local newspaper – or off the 10:00 p.m. news on TV.
If we want sprinklers to be proactive, then we have to be proactive, too.
EDITOR’S NOTE: This is part four of a six-part series that will be continued in future issues of Sprinkler Age. Part one, part two and part three appeared in the April 2015, June 2015 and August 2015 issues, respectively.
ABOUT THE AUTHOR: Ronny J. Coleman is currently the president of Fireforceone. He is a past president of the IAFC and CFAI. Over his lifetime, he has received numerous awards including the AFSA’s 1989 Henry S. Parmelee Award, the 2011 Mason Lankford Award from the Congressional Fire Services Institute, and the Tom Brennan Lifetime Achievement Award from Fire Engineering in 2014. He continues as a contributor to the fire service in many ways.