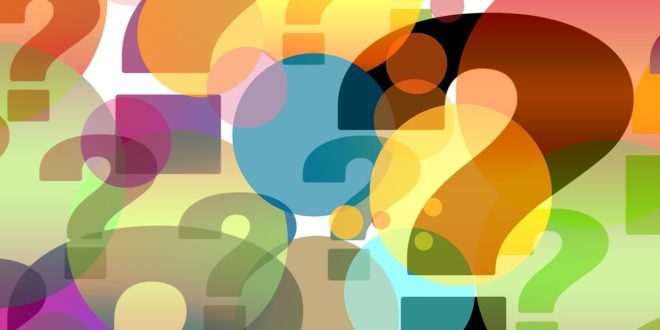
Have Issues with ITM?
Members Save Time and Money with Informal Interpretations
The informal interpretations featured in this issue of Sprinkler Age address inspection, testing, and maintenance (ITM) issues. Informal interpretations are prepared by the American Fire Sprinkler Association’s (AFSA) Technical Services Department— John August Denhardt, PE, FSFPE, vice president of Engineering & Technical Services; Jason Williams, CET, manager of ITM Technical Training; and Tom Noble, CET, CFPS, CWBSP, technical programs specialist. This is provided with the understanding that the AFSA assumes no liability for this opinion or actions taken on it and they are not to be considered the official position of the NFPA or its technical committees.
Subject: Hydrotesting of FDCs
QUESTION: In NFPA 25, 2014 edition, it states in section 6.3.2.1 that the fire department connection (FDC) shall be hydrostatically tested every five years. I would like to know the proper way to test the FDC. If the FDC and its piping are above ground and inside the building, this is not a problem. If the FDC is over a vault and has a wafer check installed, this creates a safety concern for testing. Being in a pit and cutting the bolts off a wafer check valve is a destructive means of testing the system and potential water engulfment in the pit. We also have FDCs that the check valve has been buried. What are your recommendations; would using a camera with a scope work to meet this code?
ANSWER: In response to your question, we have reviewed NFPA 25, Standard for the Inspection, Testing, and Maintenance of Water-Based Fire Protection Systems, 2014 edition as the applicable standard. Our informal interpretation is that an internal visual with a camera of the FDC and piping would not meet the requirement of the standard.
That said, I want to point out and discuss two different requirements for the FDC and its associated components. If we are discussing an FDC that is tied to an automatic sprinkler system, then we have to refer to section 13.7.4. Here we are told that every five years we must hydrostatically test from the fire department connection to the FDC check valve. This test requires that the piping and components be tested at 150 psi for two hours. This requirement does not place any additional pressure on the components that they are not listed for. Also, you could isolate the system controls valves to limit your test from the FDC to the manifold. The hurdle here is to get access to the automatic drain to plug for the duration of the test. It’s worth noting here that there is no guidance in the standard, annex, or the handbook for that matter, on how much pressure loss is allowable. In section A.6.3.2.1 for a very similar hydrostatic test for standpipe system FDCs that allows pressures over 175 psi, we’re told that even minimum leakage does not warrant repair. So, we have to ask what is our purpose? Are we looking to pressurize with water a normally dry portion of piping and hope to get all the water out once we have completed our test? Our history with dry systems tells us that a little bit of water and a lot of air can cause catastrophic damage to metallic system piping. With the approval of the Authority Having Jurisdiction (AHJ) or fire department, would a simple air test of 40 psi for two hours suffice testing the integrity of the piping? This test is acceptable for a dry system, to reasonably ensure that the dry piping is of good integrity. Now for section 6.3.2.1, I would argue the same as far as introducing water into normally dry piping. The concerns for safety in a confined area (pits) are warranted and all safety procedures shall be followed when entering. But these areas are not exempt and if water is a concern, then procedures should be taken to sump out the water during the process. Again, isolating the piping prior to draining and preparing for the test should minimize the amount of water. Other factors that should be considered are the frequencies for the forward flow test of the underground found in section 7.3.1 and the five-year internal inspection of check valves. These additional inspection, testing, and maintenance (ITM) functions may be the driver on how you approach these type of system configurations.
You should also note that this is a relatively new requirement and we don’t believe the committee adequately reviewed the challenges associated with this simple-sounding test nor did they provide adequate guidance regarding allowed leakage. As such, we will be bringing it up at the next NFPA 25 committee meeting.
Subject: Sprinkler Testing Sample Areas
QUESTION: The questions are in reference to NFPA 25, 2014 edition in section 5.3 for testing of sprinklers. (1) In the case of a multi-building apartment complex built concurrently in a single phase, is it appropriate to consider the entire complex as the sample area? (2) If the sample area is determined to be a single building and not the entire complex, and any sample fails would this necessitate replacement of the heads only in the building with the failed sample and not the entire complex? Our concern is that we are treating multi-system warehouses differently than we are treating apartment complexes and are looking to develop standard procedures for all our inspectors and offices. Relative references are: section 5.3.1.1.1 – Where sprinklers have been in service for 50 years, they shall be replaced or representative samples from one or more sample areas shall be tested. Section 5.3.1.1.1.6 – Dry sprinklers that have been in service for 10 years shall be replaced or representative samples shall be tested and then retested at 10-year intervals. Section 5.3.1.2 – A representative sample of sprinklers for testing per 5.3.1.1.1 shall consist of a minimum of not less than four sprinklers or 1 percent of the number of sprinklers per individual sprinkler sample, whichever is greater. Section 5.3.1.3 – Where one sprinkler within a representative sample fails to meet the test requirement, all sprinklers within the area represented by that sample shall be replaced.”
ANSWER: In response to your questions, we have reviewed NFPA 25, 2014 edition as the applicable standard. Our informal interpretation is as follows. To answer your first question as to if it is appropriate to consider the entire complex as your sample area, the answer is that it is allowed, but I would not say it is appropriate. If just one of those sprinklers were to fail, then all sprinklers throughout the complex would need to be replaced. That approach would create a lot of risk whereby one sprinkler in a localized harsher environment could force the replacement of sprinklers in other areas that may not have failed. Since we have the option of defining the area covered by a single sample, the method to minimize that risk would be to obtain your samples from as many different exposing environments that exists throughout the complex. This would avoid allowing a single area to dictate the overall outcome. This methodology would certainly increase your sample areas (upfront cost), but in return minimize the impact of any failures and better reflect the influence of the localized environment on the activation of the sprinkler. It really boils down to involving the customer and explaining the cost and potential outcomes by increasing your sample area versus minimizing your sample area.
To answer your second question in regard to whether a single building if defined as your sample area could require replacement of all the sprinklers within a complex with multiple buildings, the answer is no. The only sprinklers that are required to be replaced are those within the area represented by that individual sample. To expand this further, when you have multiple sample areas within a single building, a failure in only one sample does not require the replacement of sprinklers for the entire building.
It is worth mentioning that there are some cost-saving measures that can be applied to limit the number of sprinklers in your samples. For instance, if the same manufactured sprinklers are of the same family, for example, a 155°F GBQR sidewall installed within a living area could represent also a 155°F GBQR pendent also installed within living areas. The same could apply for an industrial plant that might have the same manufacture and family of sprinklers with like characteristics but with different orientation.
Subject: Private Fire Service Flow Tests
QUESTION: We have done a test of the underground per section 7.3.1 of NFPA 25 (2014 edition). We performed the flow test by using a single fire hydrant to obtain the residual pressure, static pressure, and flow. The code official states that the test must be done per NFPA 291, Recommended Practice for Fire Flow Testing and Marking of Hydrants, (using separate hydrants for reading the gauges and flowing water). I feel our process is adequate since NFPA 291 is not referenced in the standard but only mentioned in the annex. It also shows doing the test from the main drain or the fire department connection without the check valve.
ANSWER: In response to your question, we have reviewed NFPA 25, 2014 edition as the applicable standard. Our informal interpretation is that the flow test is not required to be conducted per NFPA 291.
Chapter 7.3.1 states that a flow test shall be conducted of the underground and exposed piping serving hydrants. Section A.7.3.1 of NFPA 25 references acceptable methods other than just through yard hydrants to verify supply flow and pressure. The intent of the test is to ensure that there is still adequate flow and pressure to meet the demand for fire protection, including but not limited to the fire sprinkler system, that the private mains serve. NFPA 25, 2014 edition expands on the requirement in sections 7.3.1.1 and 7.3.1.2, where it states if there are no means to conduct a full flow test, then the maximum available flow shall be permitted. The reason for the multiple options in testing is because the NFPA 25 committee understood that a vast amount of private fire service undergrounds would not have hydrants. What this tells us is that the committee had no intent for the test to be a real high level of accuracy (such as that required for flow tests used for system design). By allowing test methods through main drains, FDCs, and hose connections, where there is only a single means of measuring flow and the static and residual pressures, tells us that the acceptable level of accuracy is lower than a flow test conducted per NFPA 291. Furthermore, in the 2011 and 2017 editions the verbiage “serving hydrants” is not present, with the intent to include all underground and exposed piping servicing fire protection. Few, if any, of the individual supply mains have hydrants and the intent is to provide a reasonable degree of assurance that the system demand can be met. As such, extending a higher degree of accuracy to a minuscule portion of the underground piping is not warranted.
Subject: Testing of Different Sprinklers
QUESTION: In NFPA 25, 2017 edition section A.5.3.1.2, it suggests adding additional sprinklers to test if the samples are of different manufacturers with the use of “would” and not “will.” Is this similar to the use of “should” and “shall” in NFPA standards? For my fast response pendent samples, there are both Reliable and Tyco sprinklers installed. Do I take the minimum four or 1 percent of each? The language suggests to me to take samples in addition to the minimum. What would be an acceptable number of additional sample sprinklers from a different manufacturer? For example; Reliable sprinklers were originally installed, but the replacement sprinklers installed were Tyco. Now, the majority are Reliable sprinklers 20 or more years old. Do I take four Reliable sprinkler samples and two Tyco sprinklers samples or equal numbers of each to meet the minimum? Furthermore, what if I have more than two manufacturers of similar characteristic sprinklers? How would I base the numbers of additional sample sprinklers?
ANSWER: In response to your question, we have reviewed NFPA 25, 2017 edition as the applicable standard. Our informal interpretation is as follows. Section 5.3.1.2 tells us to take a representative sample of the sprinklers within an area. Typically, areas are divided by environmental conditions. For example, a loading dock/storage area is different area compared to the office space of a high-rise, or the office area of a warehouse from the storage area due to a likely difference in corrosion potential. This avoids having sample sprinklers from harsher locations dictating replacement of sprinklers in a more environmentally controlled area. In determining the makeup of the sample within an area, we have to represent all sprinklers within that area. To answer your first question about “would” versus “will,” the entire annex is explanatory material, and should only be considered as such. It is not considered a part of the body nor the enforceable portion of the standard.
Having said that, the annex provides guidance of what is intended and typically enforced. Section A.5.3.1.2 tells us that multiple sprinklers with different orientations (by the same manufacturer) but have similar frames, response, etc. and installed in the same environment could be considered representative of those sprinklers. If all the sprinklers were effectively one model, then you take the assigned minimum number of samples (1 percent or four whichever is greater). If you have multiple models (that are effectively different types or families of components) by the same manufacturer, those must be included in the sample.
There is no minimum number per model and said family can be represented by a single sprinkler, though logic tells us a proportional relationship makes sense. If you have multiple manufacturers with multiple models of each, you have to have at least one from each family. This can create a sample that is larger than the minimum-defined size. That why the section says not less than and the annex says additional sprinklers would be included within the sample.
As for different installation dates, as long as the newer replacement sprinklers are included in the sample, they become a part of the whole and their clock becomes aligned with the older sprinklers. Attempting to make them a separate sample would quickly become a logistical nightmare.
The bottom line is in defining the size of the sample. If you try to minimize the cost for testing by having just one sample, you run the risk of having to replace all the sprinklers throughout the facility. It really boils down to including the customer in the process and allowing them to be a part of the decision making and understanding the cost to benefit.
Subject: Sprinkler Position and Missing Escutcheon
QUESTION: We’ve been notified by an AHJ that the missing recessed escutcheon(s) within our customer’s building is considered an impairment and should be “red tagged.” We are in disagreement based on table A.3.3.7 due to the correct positioning of the sprinkler and the definition of impairment. Are we as the inspecting contractor missing something here with regard to the intent of NFPA 25?
ANSWER: In response to your question, we have reviewed NFPA 25, 2014 edition as the applicable standard. Our informal interpretation is that there can be a difference in classification of the deficiency based on the ability to control the fire.
We can all agree per section 5.2.1.1.6, if the escutcheon is missing from a recessed or flush sprinkler it shall be replaced and is a deficiency. Equally, if the coverplate is missing from a concealed sprinkler, it too must be replaced. The reason is that the coverplates and escutcheons are considered an integral part of the listing for the sprinkler(s) of concern. As far as defining the type of deficiency, a missing escutcheon or coverplate is. The wording on this issue is split up in table A.3.3.7 and was done for good reason. It is a little muddled, so it can be easily misinterpreted. One finding and I’m paraphrasing, is “deflector and operating element in correct position.” If the deflector and element look to be in the correct position, then the deficiency is noncritical. The other finding below that, in regard to “escutcheons and coverplates” states “deflector and operating element not in correct position.” Note the addition of “not” within the stated finding. What does it mean by the deflector and operating element not in correct position? For instance, if the deflector is far enough above the lower plane of the ceiling, whereby the water will not likely discharge into the room, then it would be an impairment. There’s also a related concern regarding the ability to activate (thus the reference to the operating element), but it’s a lot easier to focus on the location of the deflector. That is what the annex is attempting to address—the positioning of the deflector and the capability to operate.
To be classified as an impairment per section 3.3.21, the deficiency would have to be a condition where the fire protection system or unit or portion would be out of order and not function in the event of a fire. A pendent sprinkler(s) in position, merely missing the outer ring of the escutcheon could in no way be deemed out of order.
EDITOR’S NOTE: AFSA members can access past informal interpretations online at firesprinkler.org. Click on “Technical Services” and then “Informal Interpretations.” (Member username and password required to gain entry.)