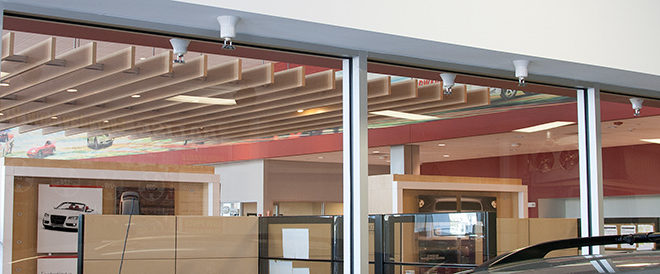
Window Sprinkler Design
Application and Pitfalls
When reviewing a set of contract documents, I often find myself gravitating to the life-safety drawings. These drawings spell out several items which help me in evaluating the overall sprinkler needs for a project. Among the most common items identified are the location and rating of the code-required fire separations/walls utilized for that project. When constructed of standard building materials, these firewalls pose little impact on sprinkler design considerations. However, more and more often, fire sprinkler contractors are faced with owners and architects who wish to utilize large quantities of glass separations in their designs. This use of glass is being utilized for applications of security, economic efficiencies, and building aesthetics. Unfortunately, this desire is complicated when coupled with the requirements for fire separation between spaces. While there is an ample amount of fire-rated glass available on the market today, owners and architects are limited to the use of either wired glass assemblies (which deter from the intended design use) or expensive laminated glass. For this reason, engineers and architects often turn to sprinkler contractors to aid in providing the required ratings of the glass assemblies with the application of window sprinkler designs. The intent of this article is to discuss the application and pitfalls of window sprinkler design.
While the applicable use of fire sprinklers for protection of windows appears to be a simple process it is, in actuality, a rather complex consideration. The first thing is to understand exactly what a window sprinkler is and is not, and how to appropriately integrate them into the sprinkler design of a building; this is a much more complicated process than one might assume. NFPA 13, Standard for the Installation of Sprinkler Systems, treats window sprinklers as a type of “special application” sprinkler and while NFPA 13 does not include design parameters in its text, section 8.15.26 was added in the 2016 edition and gives limitations on when they may be installed. For this reason, window sprinklers should be incorporated into the architectural design drawings by the design professional. It is the responsibility of the registered design professional to provide the Authority Having Jurisdiction (AHJ) with the documentation that clearly establishes the basis for compliance for a code modification. This compliance is usually aligned with the adopted building code of the local AHJs. For the purpose of this article, I will refer to the International Building Code (IBC) as it is the local code adopted by all of my local AHJs. Section 104.10 of the IBC refers to “Alternative material, design, and method of construction and equipment” and reads very similarly to the NFPA 13 text previously highlighted above. These two sections of text in the IBC and NFPA 13 give latitude to the design team to provide an engineered assembly that utilizes fire sprinklers in the protection of non-fire-rated glass assemblies. Once a design professional establishes and presents the window sprinkler requirements for a particular project, and it is accepted by the AHJ, these requirements become the design criteria to which a sprinkler system must adhere. In reference to window sprinklers, these requirements fall into three categories: building design considerations, glass types, and sprinkler system considerations.
For a fire sprinkler designer, the use and application of window sprinklers starts with the building design itself. As a fire sprinkler designer, there are a couple of items to look for in these documents.
- First is the required time of separation. A window sprinkler alternative design can only provide up to a two-hour fire-resistance rating. Separations greater than two hours cannot utilize fire sprinklers in its assembly considerations. I will discuss more in-depth the importance of knowing the resistance rating when looking at the sprinkler system considerations later in the article.
- Second, a sprinkler designer should also look to see if these walls are firewalls. Window sprinklers are allowed to be utilized in non-load-bearing fire-rated barriers as described in section 707 of the IBC, and fire partitions as described in section 708 of the IBC. These separations are typically constructed of stud and gypsum board assemblies, masonry, and other common construction type assemblies. In contrast, window sprinklers are not allowed in firewalls. Firewalls are described in IBC section 706, and are defined in IBC section 202 as, “A fire-resistance-rated wall having protected openings, which restricts the spread of fire and extends continuously from the foundation to or through the roof, with sufficient structural stability under fire conditions to allow collapse of construction on either side without collapse of the wall.” If a fire sprinkler designer notices this application is misapplied in the design documents, he or she should request information from the design professional of record.
In addition to gathering these important items about the design intent of the project, a fire sprinkler designer should also look for design pitfalls that are often missed. Again, it is important to remember that the developmental requirements for the use of window sprinklers are the responsibility of the professional of record, but fire sprinkler designers still need to understand when and how we can use window sprinklers.
- Window sprinklers are not allowed to be used in locations where detonation and deflagration hazards are present. An example of this would be in a factory or laboratory where the fire code official has identified a specific space containing product or material that code identifies as such hazards.
- Unless a building is 100 percent protected by an active sprinkler system, window sprinklers may not be used in exit passageways, exit enclosures, or horizontal exits.
The last item that a sprinkler designer must take into consideration before designing their system is the glass assembly type. Again, I caution that the responsibility falls on the registered design professional to make sure that these considerations are included in the specifications and design for a project, but a sprinkler designer should be knowledgeable of all the items that directly affect their individual systems. When it comes to the glass assemblies, there are six items that must be considered. A design must take note of glass size, glazing type, glazing frames, horizontal mullions, and openings and penetrations.
- The size of the glass is based on fire testing and sprinkler limitations. The glass height cannot exceed 13 ft, and there is no limitation to the length of the window as the window sprinkler spacing can meet the installation requirements of the manufacturer’s listing.
- Windows intended to be protected by sprinklers must be vertical. Sloped and curved glass cannot be protected by window sprinklers.
- When window sprinklers are utilized in fire separations, the glass
must be 1/4-in. thick and heat strengthened or tempered. - Window frames shall be listed with the same fire-resistance rating as the glass; this is often an overlooked item.
- When dealing with window sprinklers, horizontal mullions are in essence an obstruction to the sprinkler’s spray pattern and prevent the ability for the water to run down the glass face. The intent of a window sprinkler is to completely coat the glass with a water spray in order to keep the glass from failing due to hot spots. (See Figure 1.)
- Window sprinklers are also only intended to protect fixed glass. Operable windows can not be protected. Doors in these fire partitions must be treated separately.
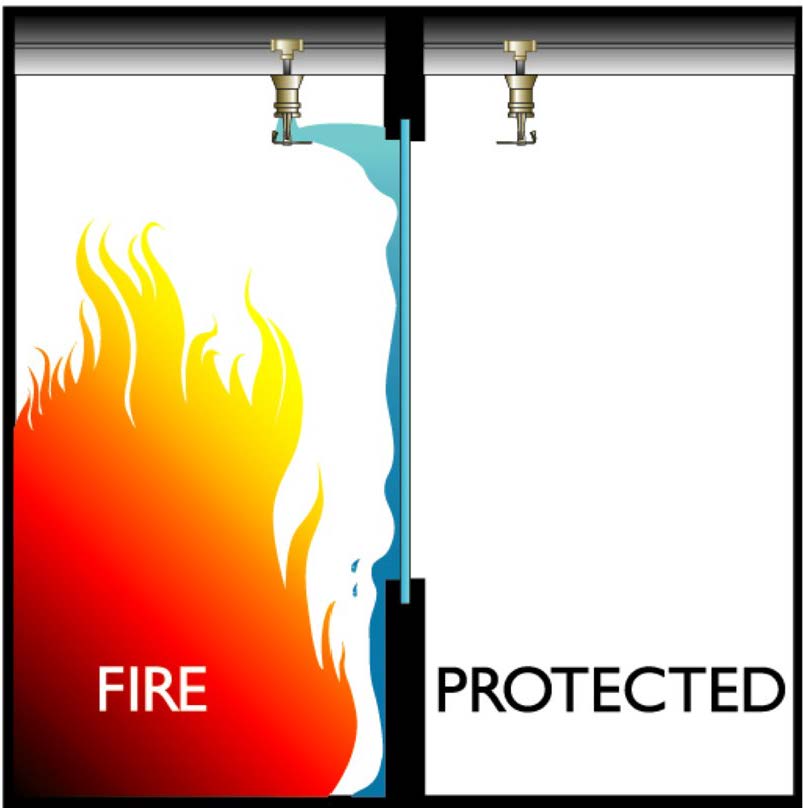
Having discussed building design consideration and glass assemblies, let’s now discuss the sprinkler design side of this. I often see sprinkler designers confuse window protection with atrium glass protection. The IBC 404.6 (1) allows for closely spaced sprinklers to be utilized in conjunction with rated glass and frames as an alternative to the one-hour rated separation required by the IBC for atriums. This allowance by the IBC gives a sprinkler designer the luxury of utilizing sprinkler heads that are not specifically listed for glass protection by utilizing a design as prescribed in NFPA 13 section 11.3.3 for water curtains. While it may be permissible to some AHJs to utilize this in other separations in the building, it is worth noting that the IBC only recognizes this for a one-hour separation specifically in atrium separations. In order to accomplish a two-hour separation, a designer must utilize a specific application window sprinkler.
In designing a system with specific application sprinklers, it is important to follow certain criteria that have clearly been proven successful during fire testing. While window sprinkler design is outside the scope of NFPA 13, it is still part of a functional sprinkler design and must be designed, calculated, sized, and installed per the requirements of NFPA 13. Window sprinklers may be utilized in fully sprinkled and non-sprinkled building in any of the following ways when acceptable to the AHJ:
- Interior fire separation where sprinklers are placed on both sides of a non-operable window in order to provide up to a two-hour fire separation in a non-load bearing wall.
- Exterior fire separation where sprinklers are placed on the inside of the building non-operable glass in order to provide up to a two-hour fire separation where required to protection adjacent buildings from a fire in your building.
- Exterior fire separation where sprinklers are placed on the outside of the non-operable glass as part of a deluge sprinkler system in order to protection your building from an adjacent hazard or building. (See Figure 2.)
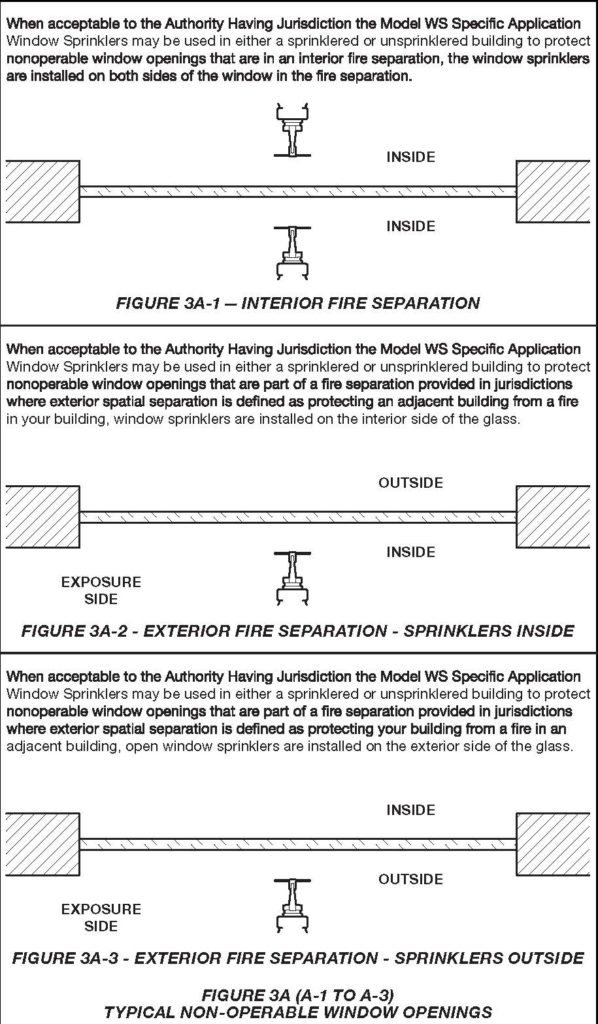
Window sprinklers can be a horizontal sidewall or a pendant vertical sidewall; the spacing considerations for both sprinkler types and all the options above are the same. Sprinkler minimum separation distance is to be 6 ft unless separated mullion of sufficient depth or a baffle and maximum spacing is to be 8 ft. A mullion is considered to be of sufficient depth when it extends to the back of a pendant vertical sidewall’s deflector, or when it extended to the wrench flat on a horizontal sidewall’s body. On window walls that have mullions, sprinkler heads shall be placed in each mullion segment and shall adhere to the spacing rules above. If sprinkler heads require being closer than 6 ft on center, an additional baffle shall be added. (See Figure 3.)
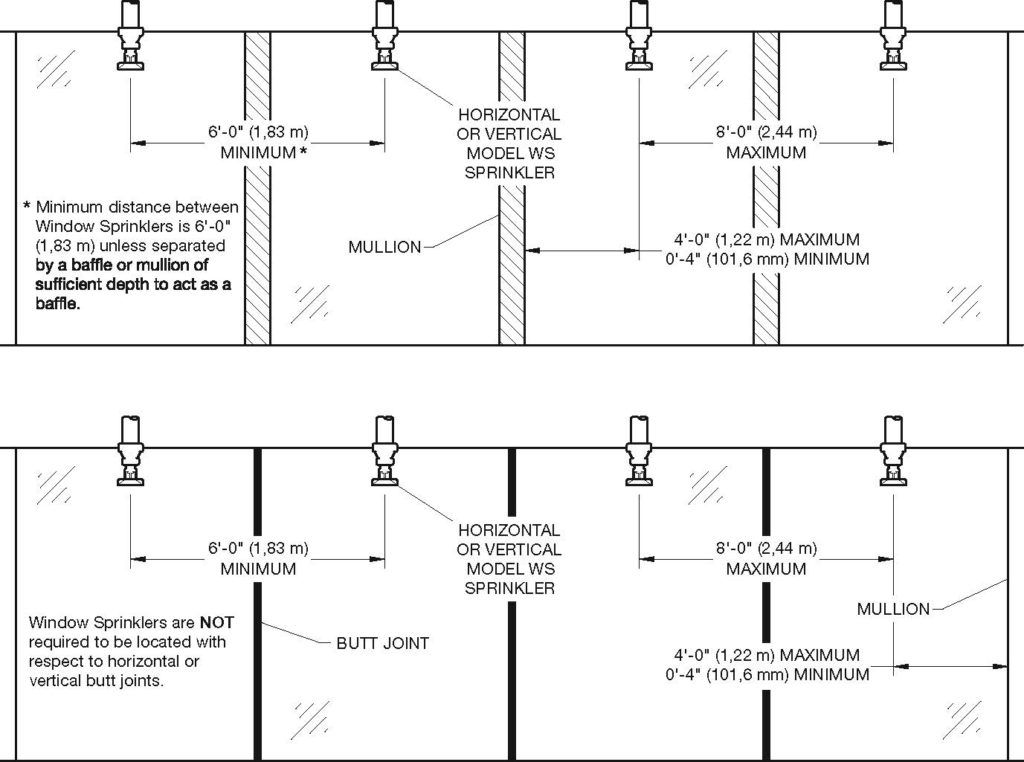
In window assemblies which do not have mullions, sprinkler heads shall be spaced evenly along the face of the window with a minimum spacing of 6 ft and a maximum spacing of 8 ft. The maximum spacing off a mullion is 4 ft. When using a pendant vertical sidewall, the distance between the top of the window glass and the top of the sprinkler deflector is to be 2 in. and the distance to the face of the sprinkler deflector from the glass is to be 1/2-in. minimum and 4-in. maximum. (See Figure 4.)
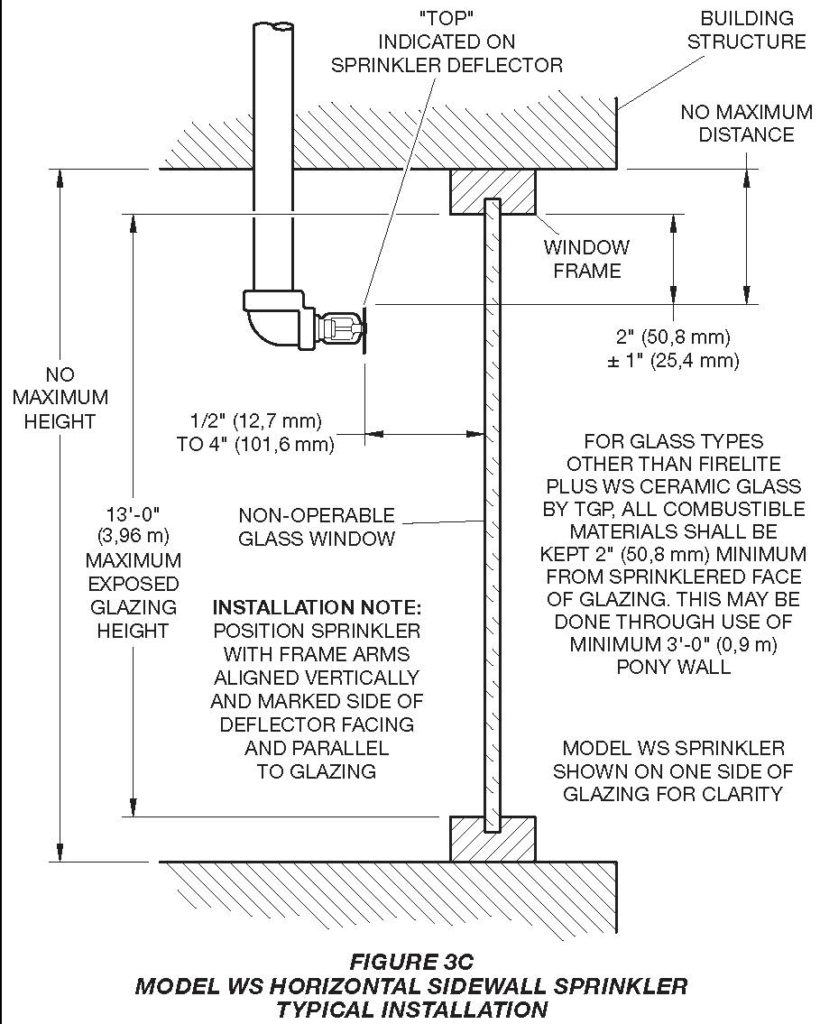
When using a vertical sidewall, the deflector shall be 3 in. from the top of the glass and the centerline of the sprinkler shall be a minimum 4 in. and maximum 12 in. from the face of the glass. (See Figure 5.)
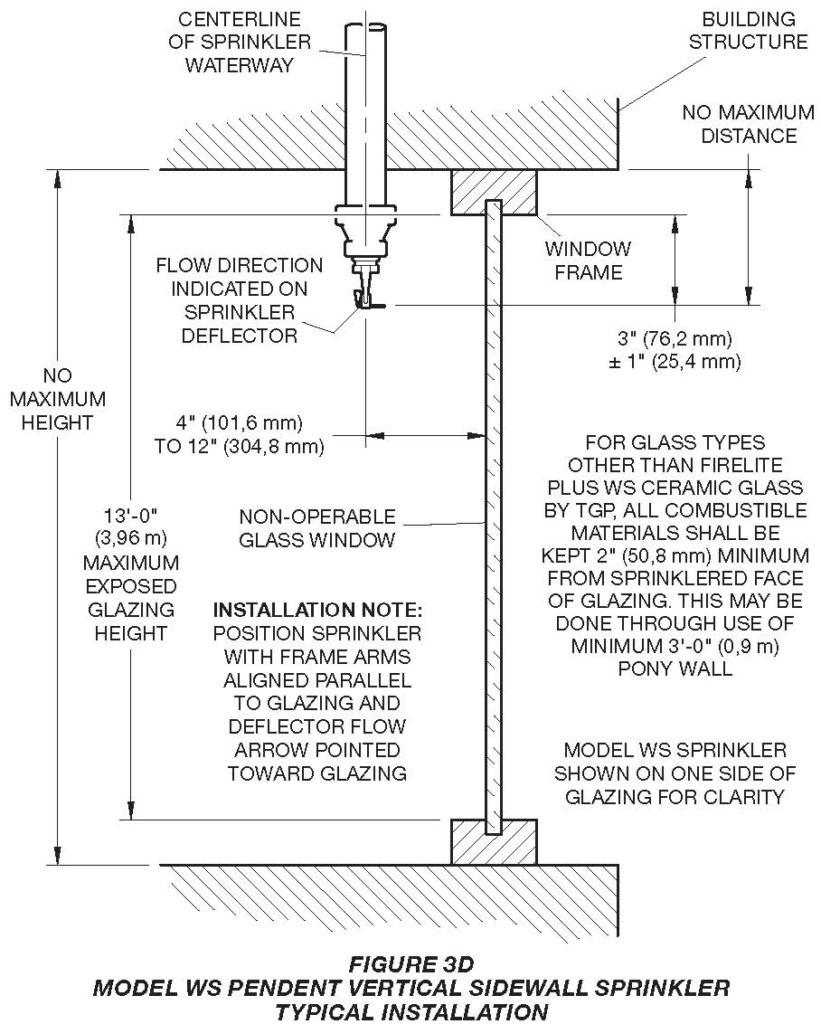
Once all the window sprinklers have been placed accordingly, a calculation must be completed. All calculations should be based on sprinkler heads flowing 20 gpm for sprinklers spaced at 6-8 ft on center or 15 gpm when sprinklers are less than 6 ft on center. Sprinkler pressures cannot exceed 70 psi for horizontal sidewall sprinklers without baffles, and a maximum of 175 psi for horizontal sidewalls with baffles and vertical sidewalls. From this point, the calculations are based on whether the building is sprinklered or non-sprinklered, and the method of protection required.
When a building is 100 percent sprinkled and window sprinklers are being used to provide an interior fire separation, the most hydraulically demanding 46.5 linear feet (LF) of sprinklers are to be calculated. This is based on the NFPA 13 equation of length of a design area of 1500 ft², which is 1.2√(area). It is permissible to reduce this area if the sprinkler system has utilized a reduction in area for the use of quick response heads. The reduction can be no less than 36 LF. If the fire sprinkler system’s most demanding remote area and the most remote window sprinkler area are expected to be activated by a single fire, the window sprinkler must be added to and balanced with the overhead sprinkler demand. While this is not required if the window sprinklers are in a different area than the sprinkler system’s most demanding area, it is still necessary to prove that the sprinkler system area and the window sprinkler area can simultaneously active.
- When a building is not sprinklered and window sprinklers are utilized to provide a rated separation interior to the building, all the sprinklers on the most demanding side of the window shall be calculated.
- When a building utilizes a deluge sprinkler system to provide a separation to adjacent buildings on the outside of the building, all sprinklers controlled by that deluge valve shall be calculated.
The final thing for which a fire sprinkler designer must account for is water duration. While it seems self-explanatory, the water duration shall be equivalent to the separation rating. If the separation rating provided by the window sprinklers is to be two-hour, then the water supply for the window sprinklers shall be capable of providing the calculated volume for that two hours.
Moving forward in construction, it’s clear to see that architects and owners will continue to utilize the esthetical and economic advantages of glass in their designs. Fire sprinkler providers will need to be diligent in determining when and where this glass may infringe on sprinkler requirements for a building. When windows are included in the code-required fire separations, sprinkler contractors are likely to be employed in helping design professionals meet these requirements. While the responsibility to provide the information and design criteria to the local AHJs will be that of the licensed design professionals, fire sprinkler contractors need to be aware of the advantages and limitations of these systems. The utilization of window sprinklers to provide up to a two-hour rating is a useful tool at our disposal when properly incorporated into a building design.
ABOUT THE AUTHOR: Chris Kachura, P.E., is a major projects salesman and project manager for Southeast Fire Protection, L.P., Houston, Texas. He has a bachelor of science degree in Mechanical Engineering and Physics from Texas Tech University, multiple licenses with the Texas Fire Marshal’s Office, and is a registered P.E. in the State of Texas. He is a member of the NFPA 30 Storage and Warehouse of Containers and Portable Tanks Committee, AFSA, NFPA, and SFPE.
IMPORTANT NOTICE: The article and its content is not a Formal Interpretation issued pursuant to NFPA Regulations. Any opinion expressed is the personal opinion of the author and presenter and does not necessarily present the official position of the NFPA and its Technical Committee.