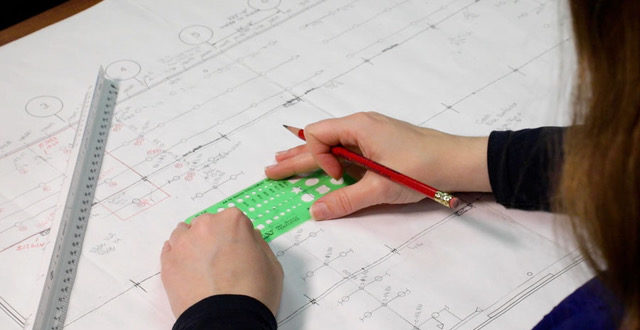
Fire Sprinkler Design
What’s the Building Owner Got to Do with It?
So, there I was opening up a set of construction documents to begin a new fire sprinkler design for a new building being built. Knowing the area, I quickly identified the location and the associated jurisdiction I would be dealing with. Having a long-standing relationship with this Authority Having Jurisdiction (AHJ), I was familiar with their currently adopted codes and standards as well as their amendments that were specific to their area. Nothing too dramatic, just a few items regarding fire department connection (FDC) locations and how their permit fees were determined. Other than that, it was business as usual. Design and install was in accordance with NFPA 13, Standard for the Installation of Sprinkler Systems. Sounds simple enough and, for the most part, it would have been except for one thing. The design criteria for the fire sprinkler system was wrong. I glanced at the name of the project on the title sheet but moved quickly into the guts of the drawings in order to get the design started. It was only after I had built my backgrounds and was ready to begin laying out sprinklers when I stopped to look at the title block again. It read “ABC Retail.” Now, any sprinkler designer or estimator with a few years behind them knows that the word “retail” is a trigger word. Right? You hear that word, and you immediately think ordinary hazard Group 2. You quickly remind yourself of the rules for spacing: 130ft2/sprinkler, density of 0.20gpm/ft2, etc. You get your roof framing plan or reflected ceiling plan up, whatever the case may be, and you start laying out sprinklers.
It was about this time that, as I was paging through the hard copy documents, I noticed a small little box with some notes in it. It read: “Fire Sprinkler system to be designed in accordance with NFPA 13. All areas considered Ordinary unless otherwise noted.” This piqued my curiosity, and I started looking through the drawings with more intent only to find that there was, in fact, a page, completely unrelated to the MEP pages, that had another note pointing to a shaded area on it that had a sheet note that read, “Storage Area.” Ah ha! There was going to be storage in this “retail” building. That is not big news. Lots of retail occupancies have storage associated with them, but then I realized that the shaded area it was pointing to had a roof deck height of 28 ft. Hang on! Something does not add up here. And of course, now is when your heart starts pumping faster, you begin to roll up your sleeves, you put your mouse off to the side, and you really start “looking” at the drawings. The more I looked, the more it became clear to me that this core and shell “retail” was going to need something more than just ordinary hazard design. At least if you intend on using NFPA 13 as the design standard.
After a complete review of the drawings and specifications, I had more questions than answers. Because I knew the mechanical engineer who was acting as the “Engineer of Record,” I decided to call him directly in lieu of writing a half dozen requests for information (RFIs) that would only bog me down and possibly make him look very bad in front of his clients. After discussing this with him, it became clear that this one got past him, and it was, in fact, high-piled storage and ended up being a density of 0.3gpm/ft2 over 2,000ft2. A far cry (not to mention a lot of money) from 0.20gpm/ft2 over 1,500ft2. As the call ended, he thanked me with sincerity. You see, this was an engineering offense punishable by a minimum of a letter of reprimand or a maximum of possible license suspension from the state board of registrants. Longer story short, we got a change order and kept our relationship with the engineer intact. The moral of this story: he who uses the Owner’s Certificate has a long and successful engineering career.
Sadly, none of this had to happen, and the entire issue could have been avoided had the engineer filled out and used the Owner’s Certificate (Figure A.27.1(b)) found in NFPA 13.
The purpose of this article is not to re-open old wounds regarding engineering versus design and layout, but rather to point to this form and how, if used, it can make the design process easier, more accurate, and most importantly, put the liability for the design criteria where it belongs. A form, I might add, that has been available and “required” in NFPA 13 since the 2002 edition. I doubt many, if not most, day-to-day practitioners of this standard have actually never seen one or, if available, ever bothered to look it over or even ask what it was intended to be used for. In my opinion, the Owner’s Certificate is arguably the single most important part of a fire sprinkler design and here’s why.
While sprinkler design is not quite as easy as many estimators and pipe fitters think it is, it can be reduced down to a mathematical formula. This formula has everything to do with the design of the system and how much the system will cost. It looks like this:
The first formula of sprinkler design is:
1. (d) x (A) = Qm
Where: d = density (gpm/ft2).
A = square foot area of the Area of Operation
(remote area) and/or the assigned area of an individual sprinkler (ft2).
Qm = minimum gpm required (gpm).
Once you solve for Qm we can now solve for pressure (P). This is its influence on design. The second formula of sprinkler design is:
2. Qm = K √P
Where: Qm = minimum gpm required.
K = K factor of the sprinkler or other orifice water is flowing through.
P = pressure (psi).
Now that you have solved for P we can now solve for ($). This is its influence on cost. The third formula of sprinkler design is:
3. P = $
Where: P = pressure (psi).
$ = how much the system will cost (material and labor).
Obviously, the higher P is, the higher the cost of the system, both in terms of material as well as labor.
So, knowing how this formula is key to the design and cost of a sprinkler system, it stands to reason that the values established in this first formula need to be right. They need to be correct. If they are not, then every part of the hydraulic calculations is wrong, no matter how correct the math is and the location of one or all of the sprinklers is wrong. They could be wrong in the positive or the negative; but either way, it is wrong. My question to you is, where do (d) and (A) come from? Who says (d) = X? In the good old days, when the only buildings that had sprinklers in them were industrial- and higher-hazard type occupancies and the only people involved with the design were the contractors installing them, (d) came from “someone,” most likely the estimator or designer, looking at the title block. They then referred to a list in NFPA 13 and matched up the name of the project with a hazard/occupancy classification in that list. For example, you see the word “ABC Office Building” in the title block and you run to the list in NFPA 13 for hazards and find that the word “office” is on the light hazard list (13-A.4.3.2). But stop and ask yourself. What was in an office back in the 1950s when this list was first compiled? Was it full of Group A plastics like it is today? Did they work in office spaces that had no ceilings in them and the roof deck was 20-ft high? Did they have open spaces filled with prewired cubicles that have walls well within the 18-in. clearance zone defined by pattern development obstructions?
Another example would be restaurants. Take for instance, “Scandaliato’s Pizzeria.” You think: “This must be a great pizza restaurant!” But, did you know that I cook your pizza out in the middle of where you eat your pizza? If you look at section 13-A.4.3.2 you will see that where you eat this great pizza is light hazard, but, where I cook this great pizza, that is ordinary hazard.
Or, how about retail? What do you think of when you hear this word? Do you think of the strip shopping centers with stores filled with stuff to sell all under a ceiling that is 12-ft high? Or do you think of Walmart; Bed, Bath, and Beyond; or, better yet, Home Depot? They are all retail! Who wants to be first to pronounce these as ordinary hazard occupancies?
Another example is churches. You think to yourself “a church is a church is a church.” Well, if you think that way, you’d be wrong. Again, back in the early days of NFPA 13 development when it was visibly clear if a building was a church, usually given away by the huge white cross in front and the steeple with a bell in it, we would go to our list in NFPA 13-A.4.2 and find, low and behold, it has been deemed to be light hazard. One could argue that some churches are a higher hazard than others, but that would be a topic in another magazine with a different title; nevertheless, it begs the question: Are all churches light hazard? The church I went to at the time was a church on Sunday, but every other day of the week it was a school lunchroom, volleyball/basketball court, and during the “Fall Festival” we would line up hay bales in rows throughout the auditorium complete with cornhusk piles and bob for apples. Not something the framers of our NFPA 13 hazard classification list probably thought would have ever been possible.
These are just a few examples of how determining (d) can go wrong very quickly. The scary part of all of this is not the fact that I am cooking your pizza, but what many contractors and most design professionals do not understand. The name of the project in the title block or the type of business it is claiming to be does not automatically mean that the hazard corresponds to the name.
The good news is that, while it took us until the 21st century to do something about it, we now have a mechanism in place by which this extremely important decision is made, not only with guidance on how to make it but with whom is making it as well.
Before you go any further, I would encourage you to go find the example of an “Owner’s Certificate” in NFPA 13 – Figure A.23.1(b) and reference it as we highlight some of its contents.
To start with let’s first go to the last page of the last section where signatures are required. Notice who is supposed to sign this certificate: the owner’s representative or agent. I can tell you that while this language appears to be vague or generic, the intent is that the design professional or specifying consultant, who is taking ownership of this information for the project and deems themselves qualified to do so, will be the person signing it. There is nothing specific to this document that mandates a particular person or qualification; however, the intent is to have a design professional, capable and qualified to identify and correctly fill this form out, sign it.
Moreover, this certificate should be required by the building and/or fire department (AHJ), to be submitted with the construction documents when applying for the building permit. It should not be handed over to a contractor after the project is already out of the ground and someone remembered to call them to get them started. It should also be noted that this document is supposed to be submitted with the working plans as required by section 23.1.4.
The first section of the certificate pertains to project information—the name and address of the property that is being protected. Then there is the name of the owner. This is important because it identifies who is responsible for this system. This information has far-reaching implications. One strong example to support the importance of this can be found in NFPA 25, Standard for the Inspection, Testing, and Maintenance of Water-Based Fire Protection Systems, section 4.1.
The next three sections are aimed at separating out specific occupancies and hazards that have their own NFPA standard with specific criteria not necessarily found inside of NFPA 13. For instance, aircraft hangar would involve NFPA 409, Standard on Aircraft Hangars, and flammable or combustible liquids would send someone to NFPA 30, Flammable and Combustible Liquids Code, etc. At the very least, the intent is to guide the design professional through a review of the occupancy to identify those hazards that otherwise may not fall neatly into the predominate or easy-to-define occupancy/hazard classification (i.e., light and ordinary).
The next few sections after this are the triggers for storage. Had the design engineer who worked on my project described earlier used this form, he most likely would have identified that storage was involved and been able to provide the correct variables that are needed by the contractor to select the right design criteria. I personally feel that this part of the certificate is weak, but for now it is better than nothing.
The final section, while important, is not the only information intended to be provided with regard to water supply. Yes, knowing about the source and characteristics that would lead to issues of corrosion are important to note, but it would still be on the design professional to do something about it. If they say yes, there is concern for corrosion with this project, then it is also up to them to make the necessary changes in their specifications, including pipe and system types that would mitigate this issue. Again, not something that should be left up to a contractor trying to win a contract to do the work.
The more important part of this section is what is eluded to in the clause “special information concerning the water supply.” What is most important here is the water supply information. Specifically, the static pressure, residual pressure, and flow rate. While this is not included in the certificate, it is included in the list for required information noted in section 4.2.1-4. I am especially fond of #3, a new requirement in this edition. Finally, it is required by the 2019 edition that the water supply information be provided by the design professional. This third requirement references section 5.2.2 which outlines the overall considerations for water flow data and the source providing it (as discussed in the annex). For me, this is one of the top three significant changes made in this edition.
I would strongly encourage you to read through this entire chapter and share it with your local AHJ. It is a chapter that has been overlooked for years. However, thanks to the fact that several important and frequently used sections have been relocated into this chapter, the exposure to these requirements will now be more visible. I hope that AHJs will recognize that not only do these requirements exist, but by them adopting NFPA 13 they can enforce this chapter, including the Owner’s Certificate and the information required along with it. While some states have already developed their own mechanism for design professional accountability, many have not. Here is their chance to do themselves and everyone else involved with the design and installation of the primary life safety system for today’s built environment a huge favor. Bottom line, do not give out a building permit without this information being included in the construction documents submitted for such. Easy as that. Now, let’s go get some pizza.
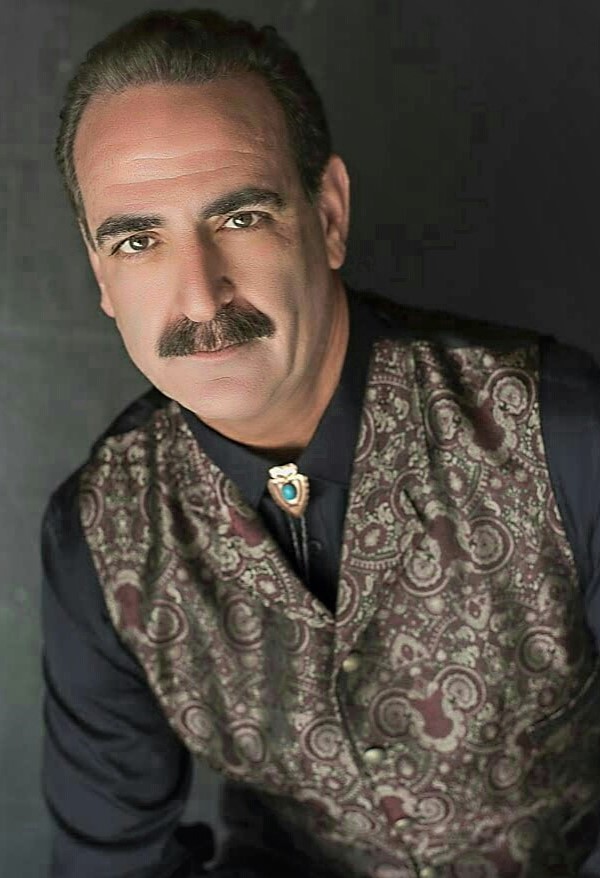
ABOUT THE AUTHOR: Steven Scandaliato is executive principal and managing director at SDG, LLC. He has over 35 years’ experience in fire protection engineering, design, and project management covering all types of fire protection and life-safety systems. He represents AFSA as a member of the NFPA 13, NFPA 16, NFPA 101®, and NFPA 5000® committees. He is published in several periodicals and is also a contributing author to the text published by NFPA/SFPE titled “A Designer’s Guide to Automatic Sprinkler Systems.” Over the last 20 years, he has presented seminars to thousands in contracting and professional associations including AFSA, the American Institute of Architects, the American Society of Plumbing Engineers, the American Society of Sanitary Engineering, the International Fire Marshals Association, and the Society of Fire Protection Engineers. He is a member of AFSA, NFPA, and SFPE.
IMPORTANT NOTICE: The article and its content is not a Formal Interpretation issued pursuant to NFPA Regulations. Any opinion expressed is the personal opinion of the author and presenter and does not necessarily present the official position of the NFPA and its Technical Committee.