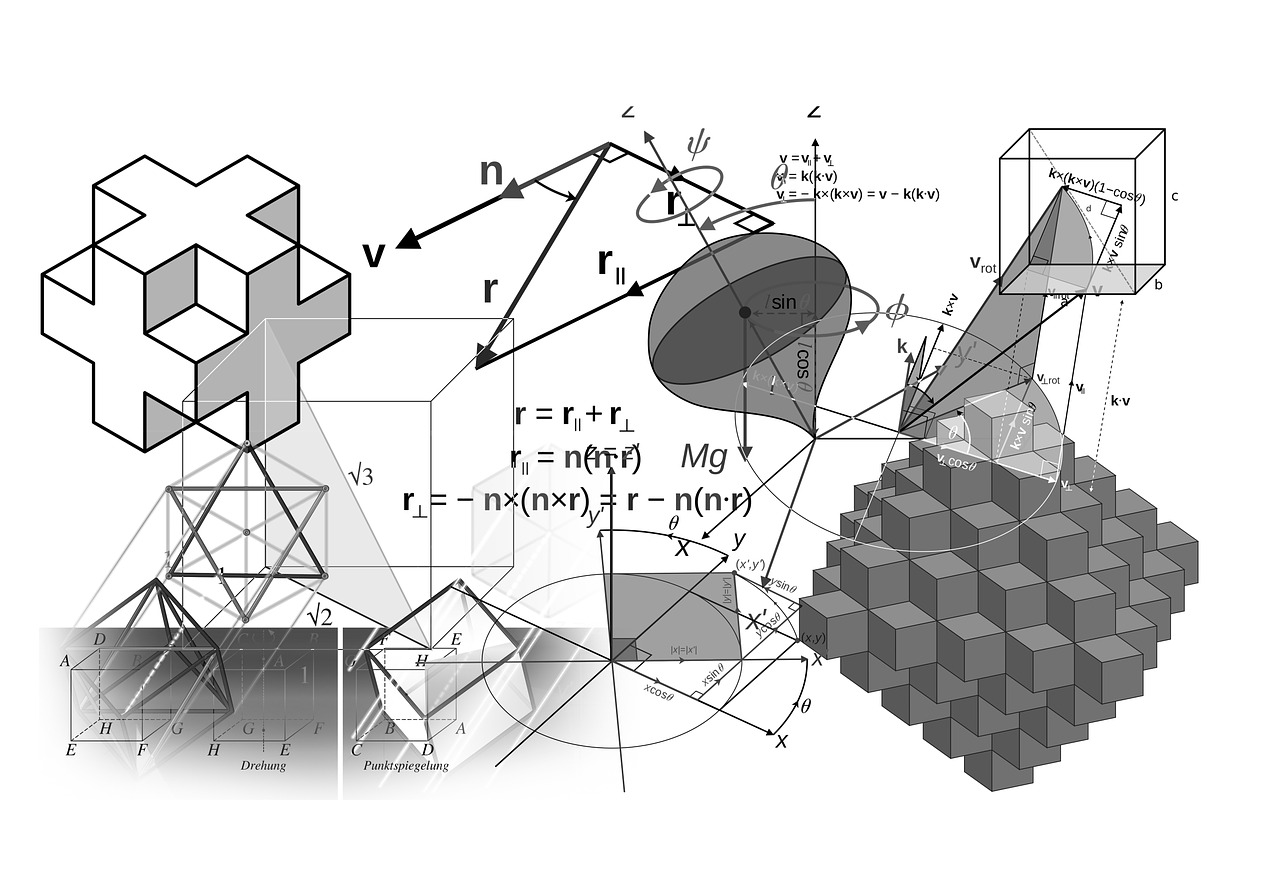
Understanding the Darcy-Weisbach Equation
When Not to Use Hazen-Williams
Any seasoned fire sprinkler designer or fire protection engineer should be familiar with the Hazen-Williams equation. It is the fundamental equation used in water-based fire protection for calculating the friction loss of water flowing through pipe. The Hazen-Williams formula (see Figure 1) is used when doing sprinkler calculations by hand, and it is used by computer-based hydraulic calculation software.
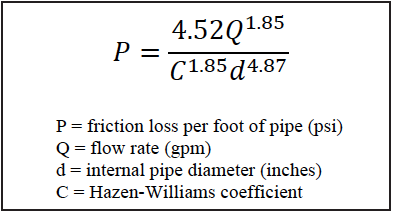
However, the Hazen-Williams equation has its limits since it does not contain a variable for density, viscosity, or temperature. It is assumed when using the Hazen-Williams formula that the fluid is water at room temperature. Having said that, don’t leap to the false conclusion that for other temperatures, you should not use the Hazen-Williams equation. The main point to understand is that when the fire protection fluid’s properties are dissimilar to those of water the Hazen-Williams formula is no longer valid. So, when friction loss needs to be calculated for other fire protection fluids such as foam concentrate, anti-freeze systems exceeding 40 gallons in capacity, or for certain high pressure mist systems, the Darcy-Weisbach formula should be applied instead. In the case of foam systems, once the foam concentrate has been appropriately proportioned with water downstream of the foam proportioning device, it is not necessary to use the Darcy-Weisbach formula for hydraulic calculations. Even in foam-water solutions as high as six percent AR-AFFF (alcohol resistant aqueous film-forming foam concentrates), the Hazen-Williams equation can still be used. Regarding water mist systems, low pressure systems (up to 175 psi) can also still be calculated using the Hazen-Williams formula. In medium and high pressure mist systems, where pressures can be anywhere from 175 psi to well in excess of 1,000 psi, the higher pressures and velocities can impact the physical properties of the water enough that the Darcy-Weisbach equation will need to be used. (See Figure 2.)
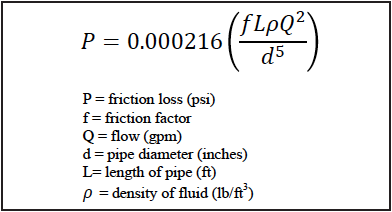
Applying the Darcy-Weisbach equation is a little convoluted because it not only has multiple variables (as shown by Figure 2), but determining the value for some of these variables is not a simple matter. The first step is to determine the friction factor (f). Calculating the friction factor is itself a multi-step process. The first step is to calculate the Reynolds Number (see Figure 3 on page 19) of the fluid. The Reynolds number (R) is a dimensionless number that relates the viscous forces in the fluid to the inertial forces of the fluid’s flow (Principles and Practice of Engineering Examination in Fire Protection Engineering Reference Manual, 4th Edition, SFPE). The density and viscosity of a fluid can be significantly impacted by the fluid’s temperature. Therefore, the anticipated operating temperature ranges of the fire protection system should be known when determining the fluid density and viscosity. The lowest anticipated temperature should be applied since that poses the higher viscosity and density that generates the greatest friction loss. These values can be found by referring to appropriate fluid physical property tables. A word of caution: there are two types of viscosity: absolute (dynamic) viscosity and kinematic viscosity. Make sure you use the absolute (dynamic) viscosity. It does not help that some foam concentrate manufacturers will provide different viscosity types on their data sheets (dynamic for their AR-AFFF concentrates and kinematic for their standard AFFF concentrates).
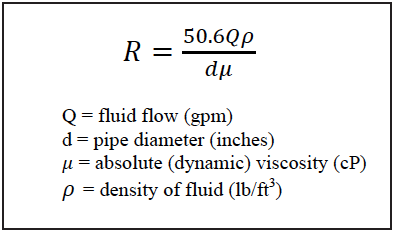
Once the Reynolds Number is calculated, the relative roughness (see Figure 4 on page 19) needs to be determined. Fortunately, suggested values for can be found in the annex of NFPA 13, Standard for the Installation of Sprinkler Systems, (see Table A.23.4.4.8.2). For example, new steel with a typical Hazen-Williams C Factor of 143 has a factor of 0.0018 in. and the typically applied C Factor of 120 has an 0.004 in. This makes solving for relative roughness a simple task.
The friction factor can now be determined from a Moody Diagram (see Figure 5) using the Reynolds number and relative roughness. Moody Diagrams can be found in NFPA 13; NFPA 16, Standard for the Installation of Foam-Water Sprinkler and Foam-Water Spray Systems; and NFPA 750, Standard on Water Mist Fire Protection Systems; as well as in various hydraulic calculation or fire protection engineering handbooks. The Reynolds numbers for water-based fire protection systems will almost always fall into the turbulent flow zone of the Moody Diagram. However, some alcohol resistant foam concentrates (AR-AFFF) may fall into the laminar flow zone due to their high viscosities. The main characteristic of the different flow zones is that the friction factor for the full turbulent zone is fairly consistent whereas the transitional zone sees a good amount of change and the laminar zone an extensive amount of change whenever the flow or pipe size changes across a piping network.
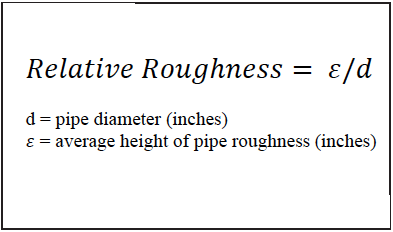
Once the friction factor has been determined, calculating the friction loss in the one section of pipe is simply a matter of plugging the variables into the Darcy-Weisbach equation. The following simple example illustrates the calculation process. Assume the system consists of 100 feet of 2-in. black schedule 40 pipe and that the fluid is a 3 percent AFFF foam concentrate with the following properties: 100 equivalent feet of 2-in. schedule 40 black steel pipe Q = 30 gpm d = 2.067 inches μ = 1.1 cP 63 lb/ft3 T = 68°F
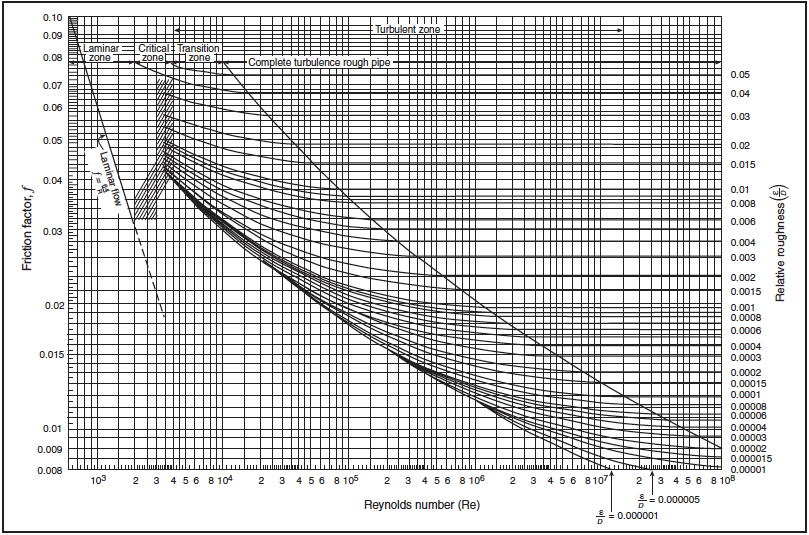
Association, Quincy, MA. This reprinted material is not the complete and official position of the NFPA on the referenced subject, which is represented only by the standard in
its entirety which may be obtained through the NFPA website at www.nfpa.org
Calculating the Reynolds Number yields the following result:
If it is assumed that the pipe would have a C-factor of 100 this would equate to an = 0.015. So the relative roughness can be calculated as shown below.
Now that the Reynolds Number and the relative roughness have been calculated, the friction factor can be determined by referring back to the Moody diagram. The friction factor is found to be 0.0375. Finally, the friction loss through the section of pipe can be calculated.
While the final step may be easy, the overall calculation can be cumbersome and is not for the faint of heart. It should not be assumed that because of the more detailed process required to perform the Darcy-Weisbach calculation, that it is any more accurate than the Hazen-Williams equation for calculations involving water. In fact, there are variables such as seasonal changes in temperature, assumption of the pipe roughness, or error introduced by manually interpolating the Moody diagram that can affect the accuracy of results. Nevertheless, the Darcy-Weisbach method is essential for properly calculating friction losses in piping for viscous fluids. A trustworthy hydraulic calculation program is worth its weight in gold when this becomes necessary.
ABOUT THE AUTHOR: Parks Moore is the CEO of S & S Sprinkler Company in Mobile, Alabama. He has a Bachelor’s degree in mechanical engineering from Vanderbilt University and a Masters in Business Administration from Tulane University. He is a licensed fire protection engineer, a Certified Fire Protection Specialist, and holds a NICET IV certification in automatic sprinkler system layout. He currently serves as an alternate member on the NFPA 13 Technical Committee for Installation and is a principal member of the NFPA 15 Technical Committee for Water Spray Fixed Systems. He is a past president of the Alabama Fire Sprinkler Association and has been actively involved as one of its board members since 2007. Moore is also a member of AFSA, NFPA, and SFPE